Useful Commands for Class-A Surfacing in Rhino 3D
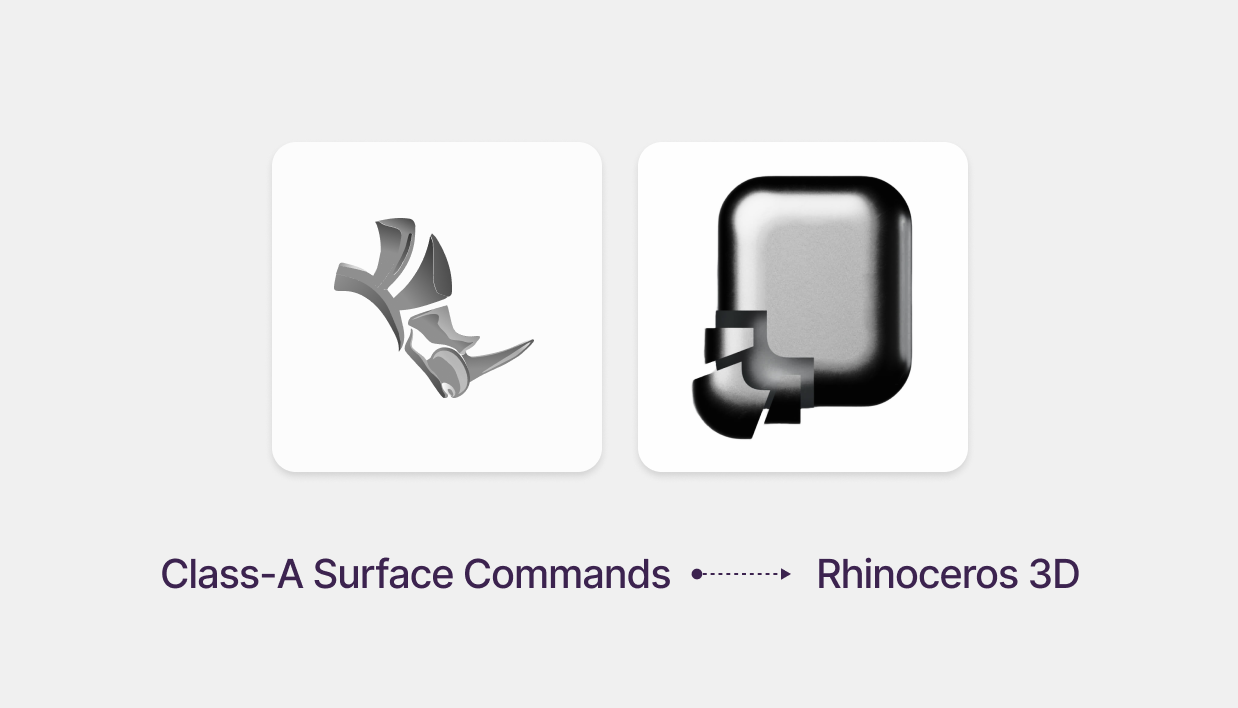
Class-A surfacing represents the highest quality of surface modeling, ensuring superior finish, smooth transitions, and precise continuity. This guide covers foundational and advanced Rhino 3D commands that help industrial designers achieve Class-A surfaces. From basic shape creation to surface refinement, each command plays a crucial role in the design workflow.
1. _ExtrudeCrv
1. Preserves the original curve’s degree and control points along one direction.
2. Creates a degree-one surface in the extruded direction.
3. Ideal for generating simple, untrimmed surfaces with predictable control point distribution.
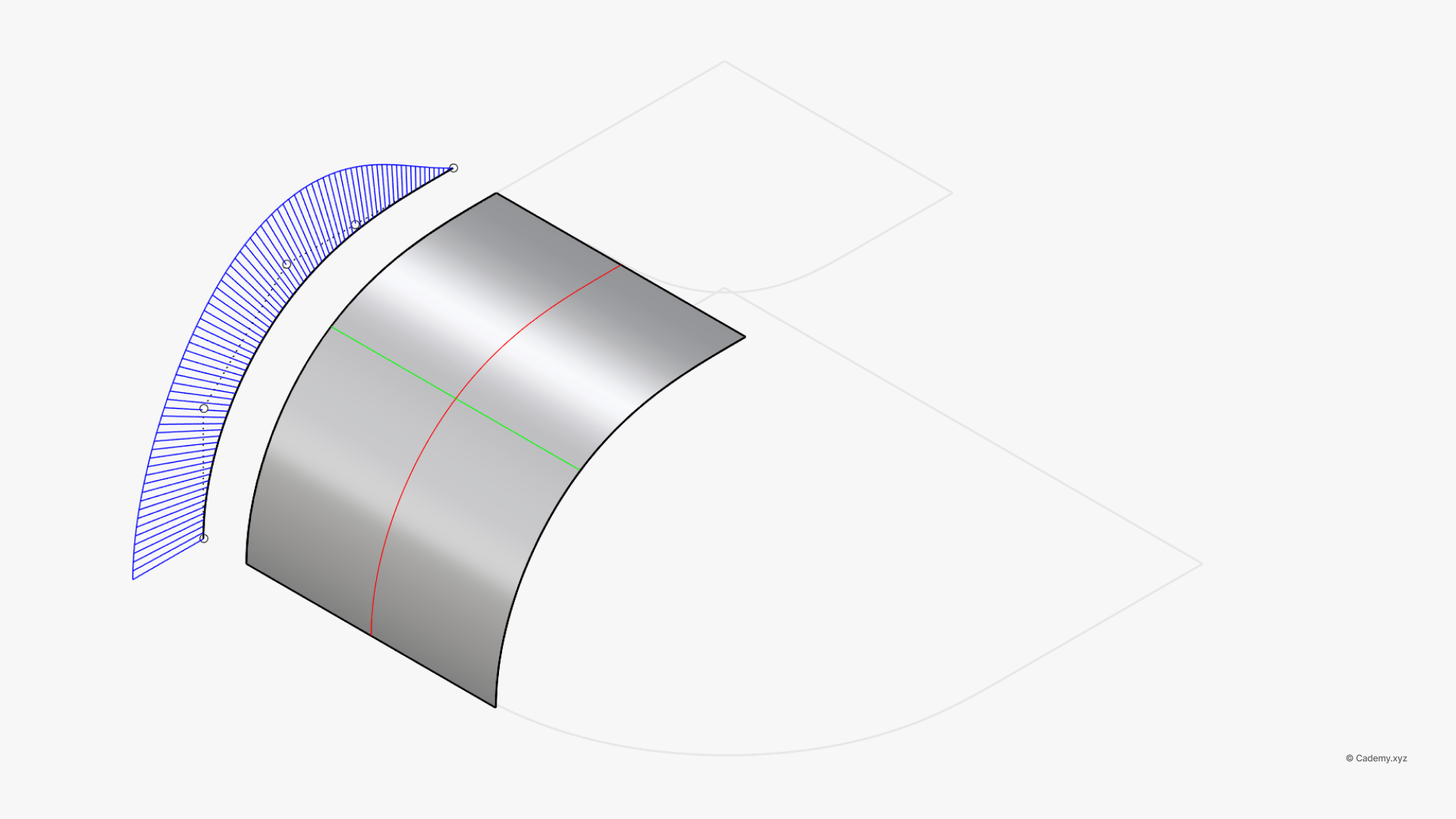
2. _Loft
4. Generates a surface between two or more input curves.
5. Can create single-span surfaces, which are beneficial for maintaining Class-A quality.
6. Complex input curves may lead to multi-span surfaces requiring refinement.
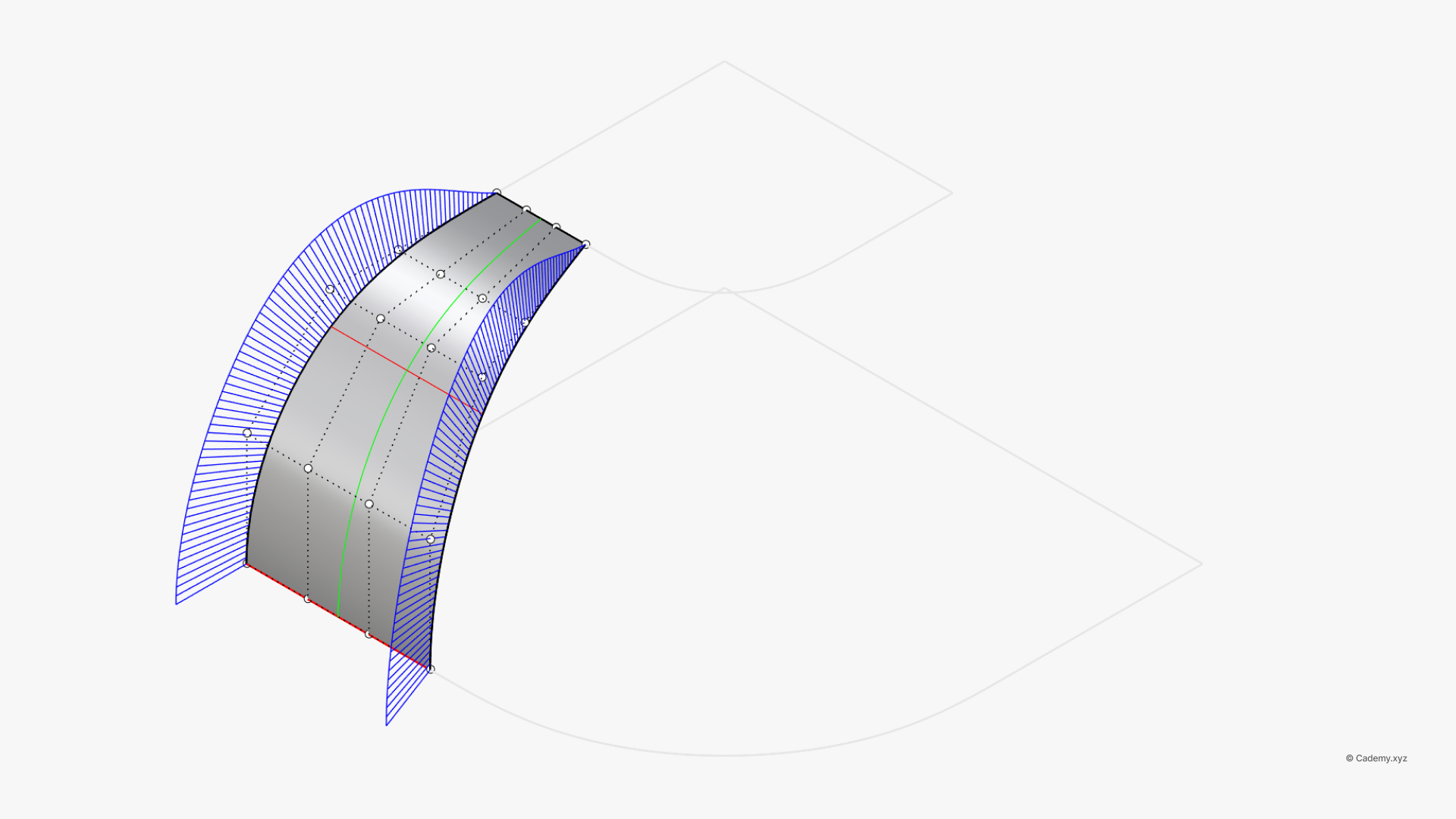
3. _Sweep1 & _Sweep2
7. Follows one or two rail curves to create a surface.
8. Maintains continuity but may result in uneven control point distribution.
9. Suitable for organic forms but may require refinement for primary Class-A surfaces.
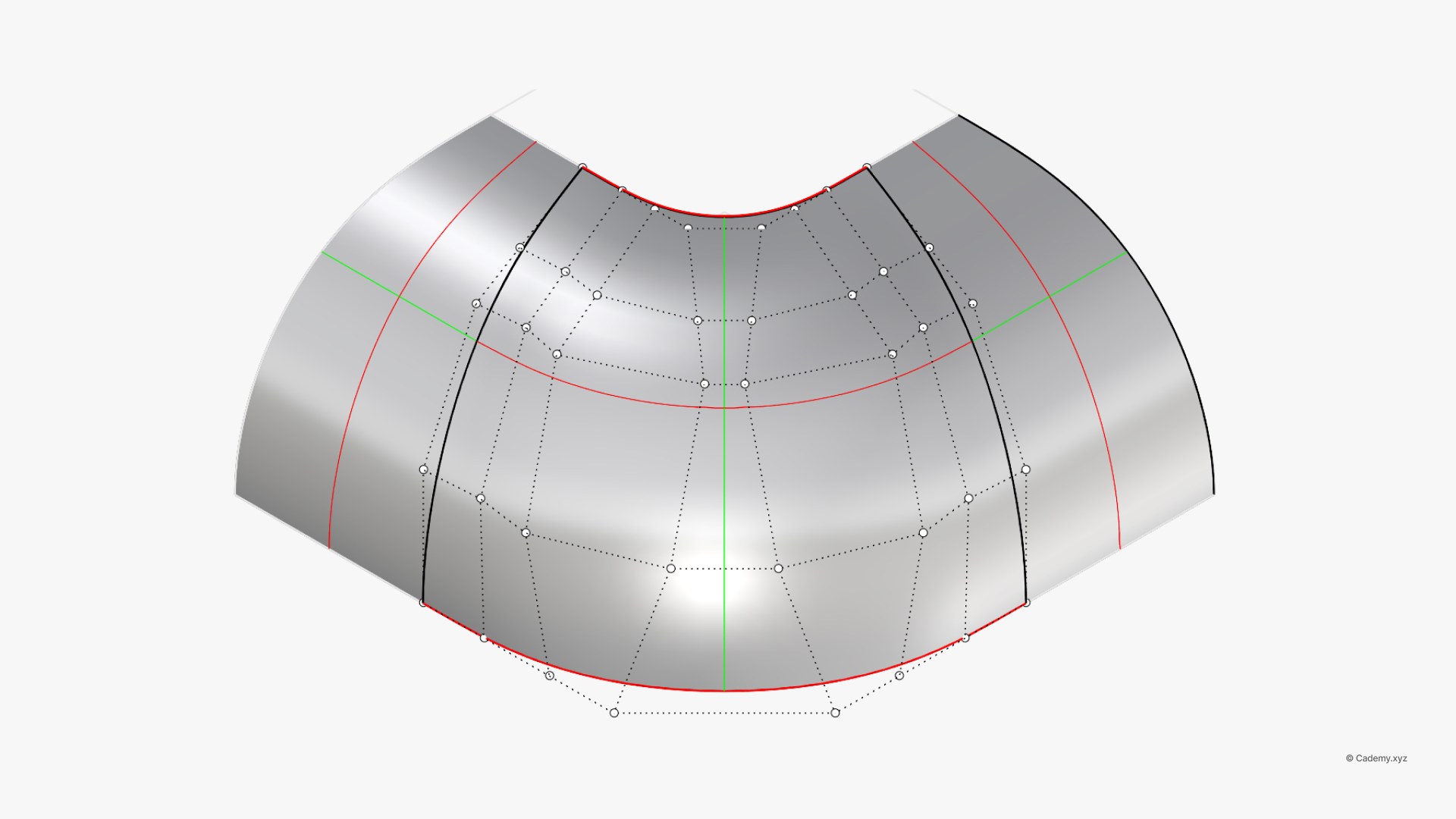
4. _EdgeSrf
10. Constructs a four-sided surface using input boundary curves.
11. Produces clean, single-span surfaces for seamless integration.
12. Requires separate continuity adjustments after surface generation.
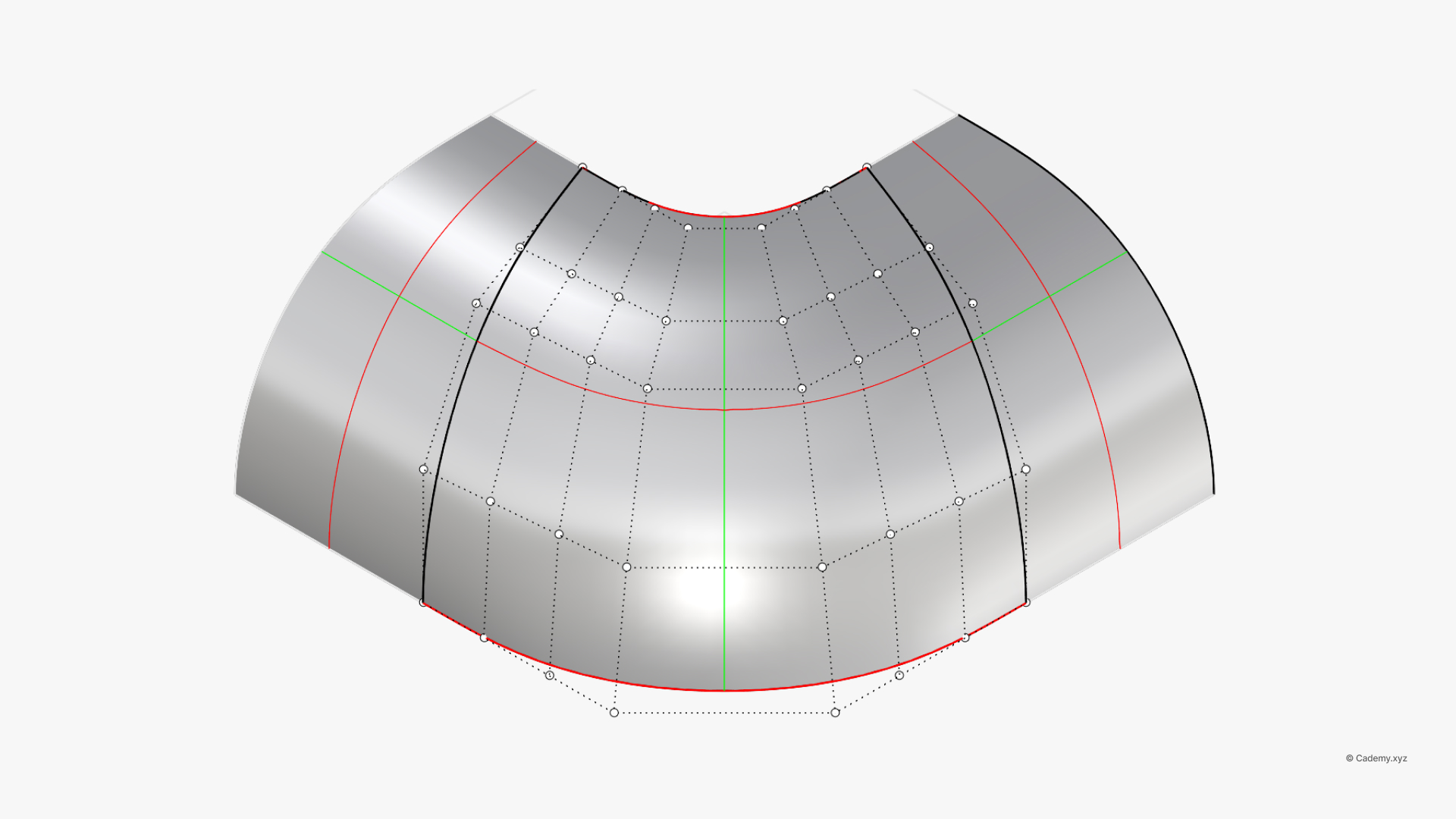
5. _PlanarSrf
13. Creates a flat surface from a closed boundary.
14. Essential for planar sections but may require trimming for non-four-sided boundaries.
15. Trimmed edges introduce multi-span curves, potentially complicating continuity.
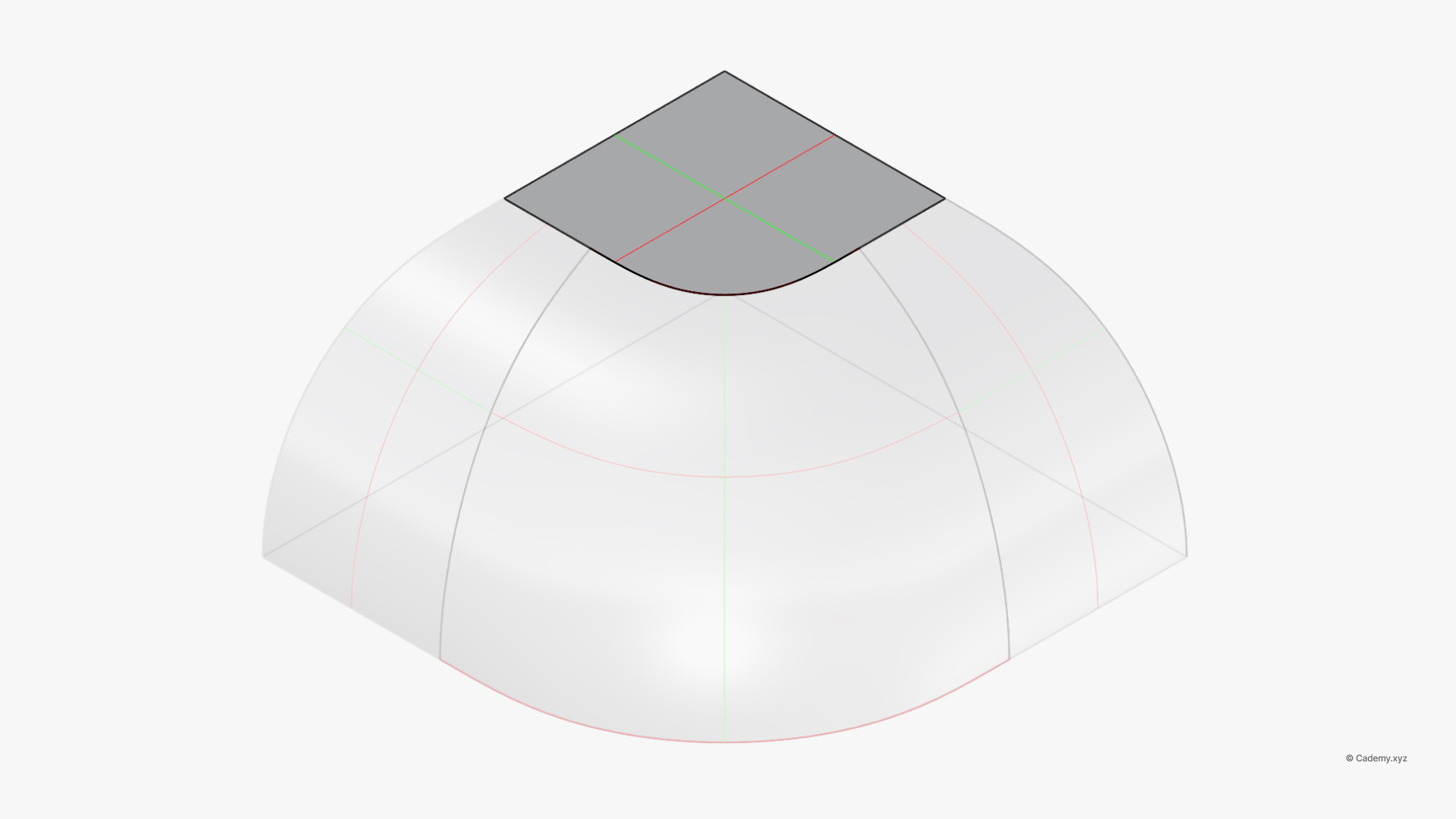
6. _NetworkSrf
16. Generates a surface from a network of input curves.
17. Creates a Degree 3 surface in both U and V directions.
18. Does not inherit input curve properties, making it more suitable for organic rather than primary Class-A
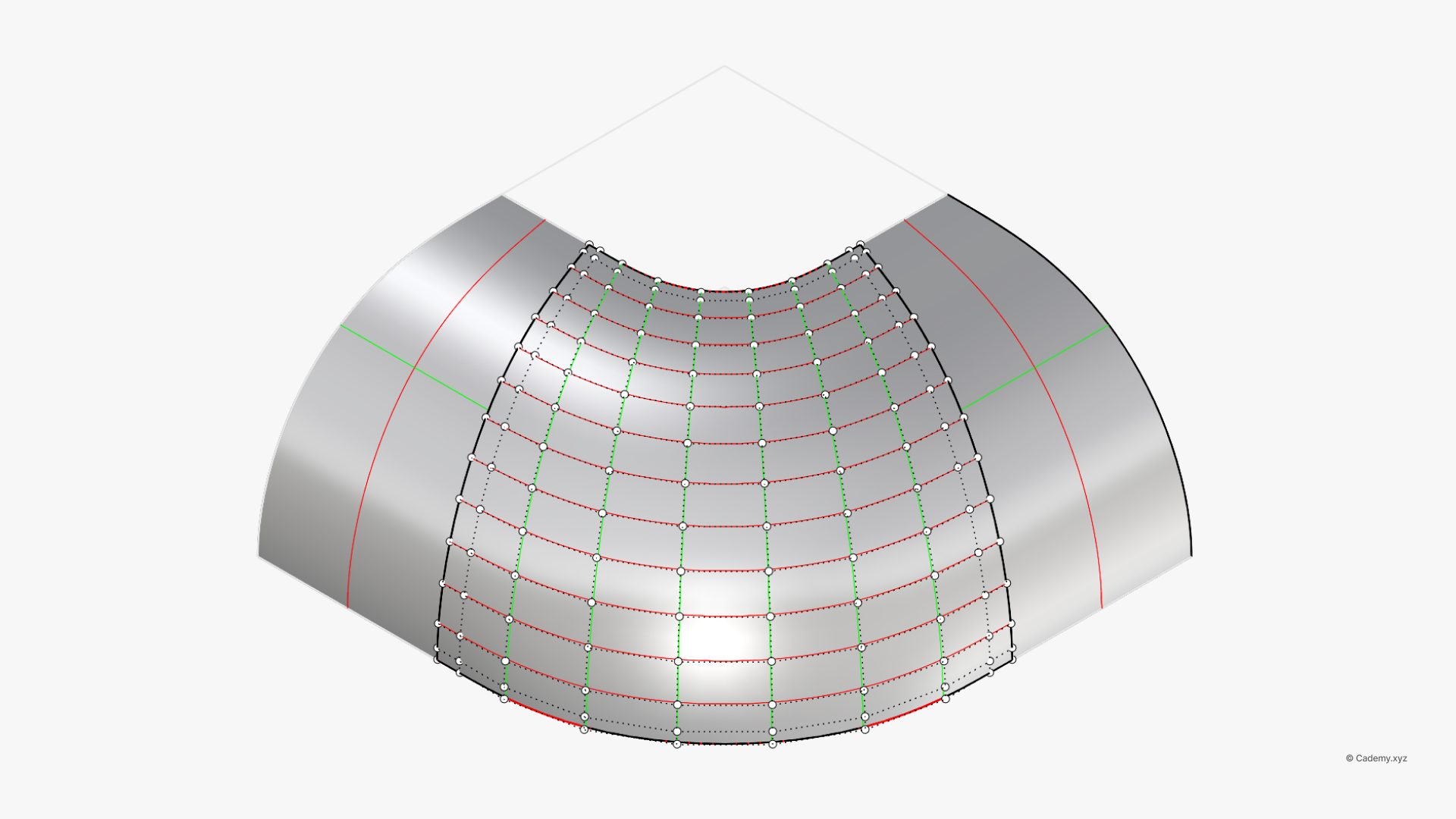
7. _Patch
19. Fills holes and complex gaps where other surfacing techniques fail.
20. Works with boundaries of any shape, making it useful for irregular intersections.
21. Often a last resort due to trimmed, multi-span surfaces that can result in uneven highlights.
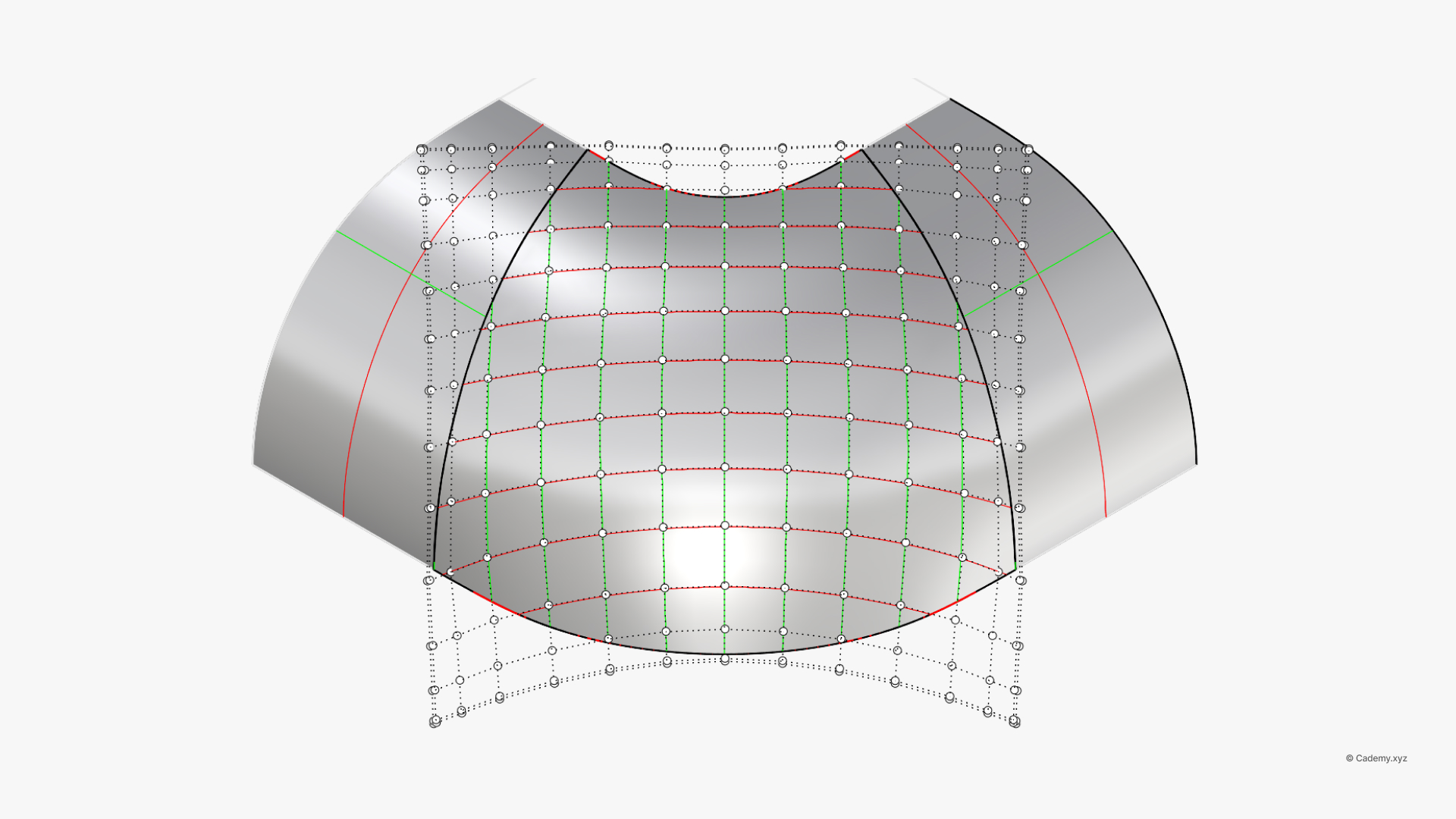
Conclusion
Mastering Class-A surfacing is essential for industrial designers, as it directly impacts the quality, aesthetics, and manufacturability of a product. Careful selection and application of these commands help maintain smooth transitions, minimize surface complexity, and ensure the highest quality output.
Thanks for reading ❤️
Don’t miss out, enroll today.
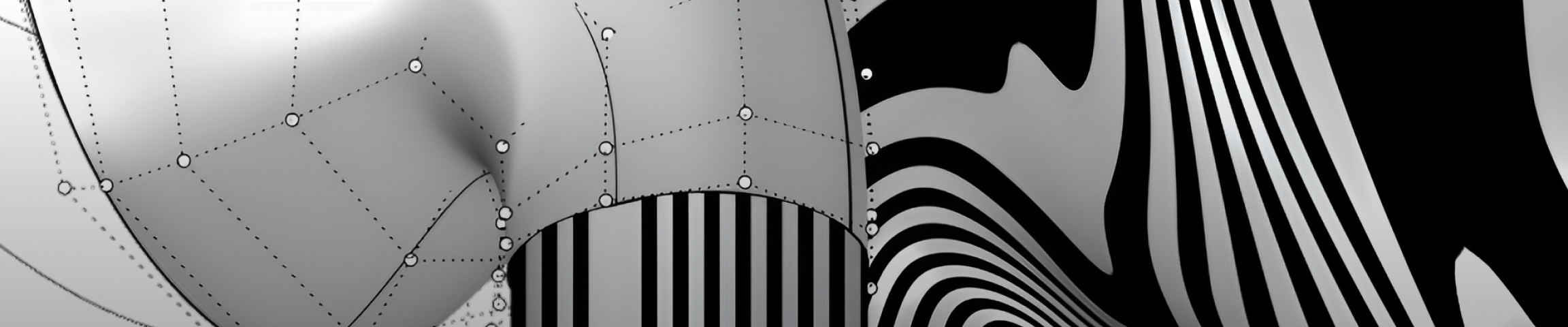