Rhinoceros - Grasshopper - Keyshot | Workflow 5
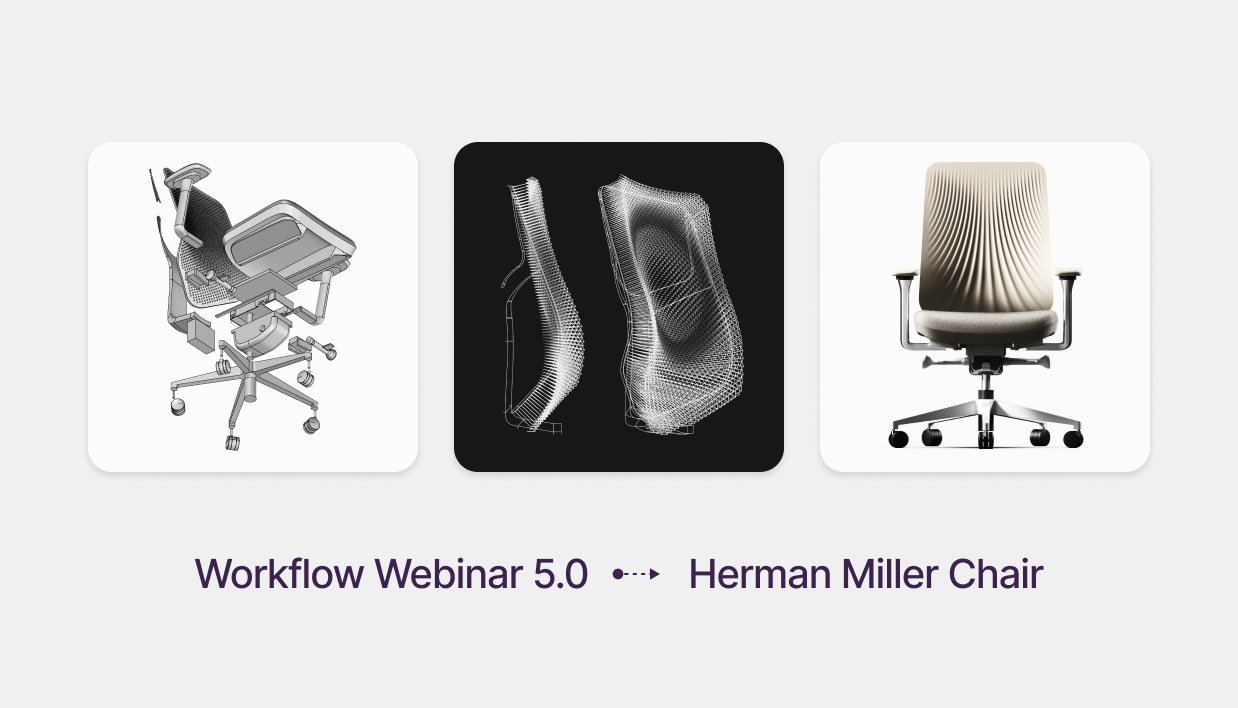
Download Files: cademy.xyz/webinar5
Herman Miller Chair is an ergonomic task chair designed for comfort and support. It features adjustable components like seat height, lumbar support, and armrests. With PostureFit technology, it promotes neutral spine alignment and reduces back strain. Constructed with high-quality materials, including breathable mesh, it enhances user comfort throughout the day.
At Cademy, we’ll guide you through the complete process of modeling this chair and creating custom texture variations for the back support mesh.
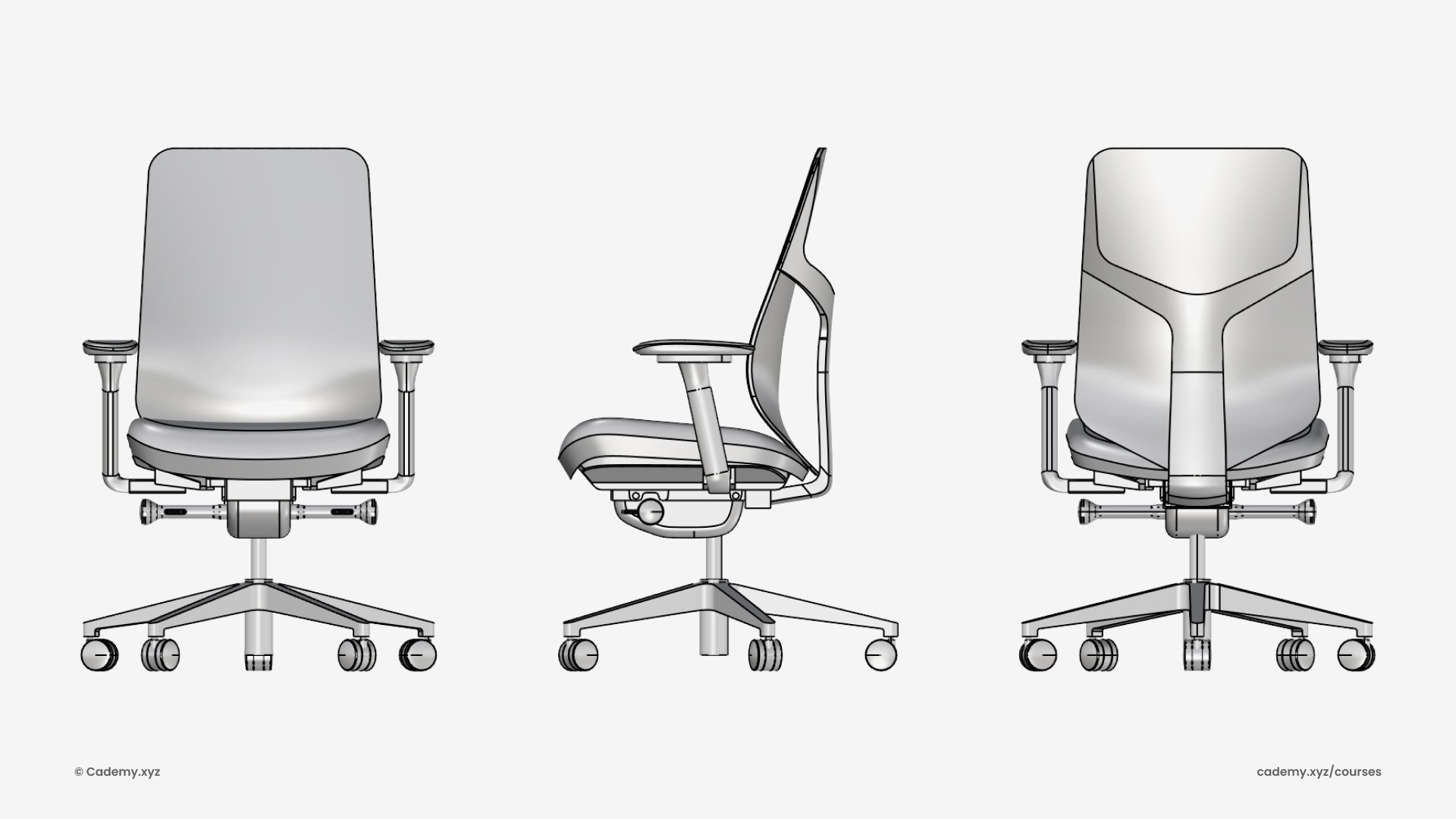
Step 1: Base Structure
1. Create a side profile using the Project command.
2. Use Loft to generate the primary surface for the back support.
3. Add guiding curves and refine the back profile.
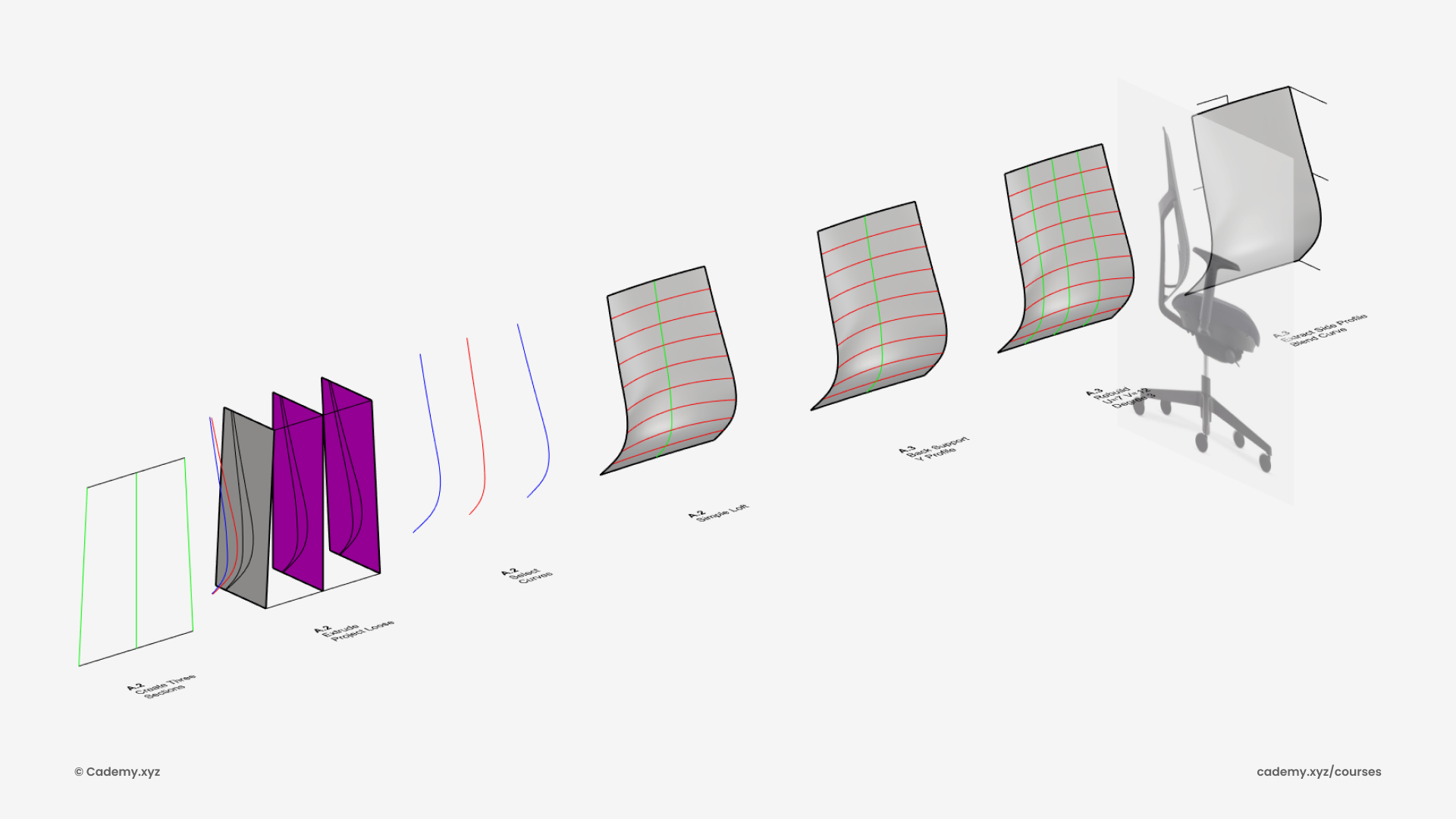
Step 2: Surface Creation
4. Use BlendCrv for smooth curve connections (G0 and G1 continuity).
5. Generate a surface using NetworkSrf from U and V curves.
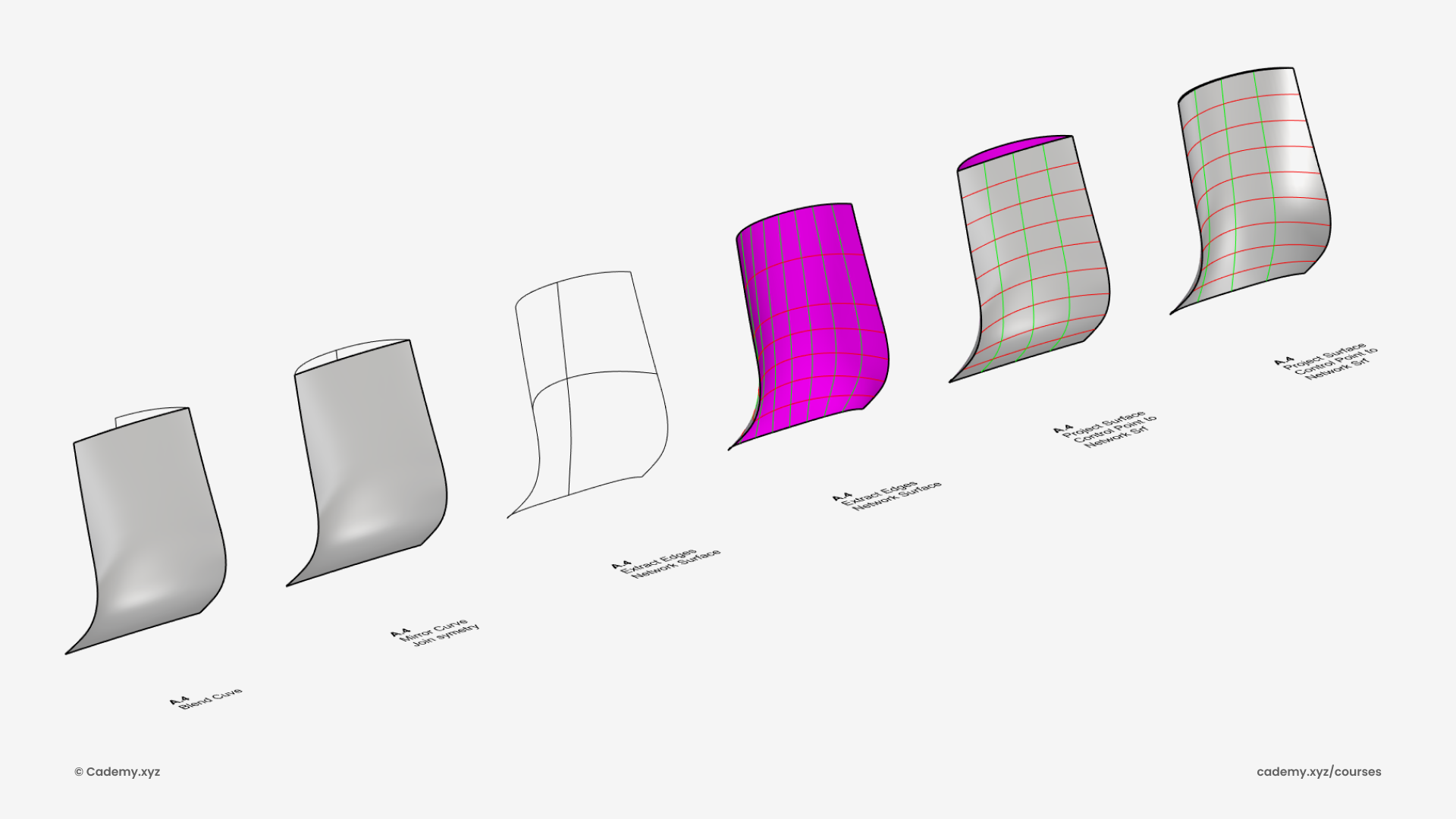
Step 3: Cut-Outs & Refinement
6. Draw outer and Y-shaped cut-out profiles.
7. Trim surfaces using these profiles to refine the chair’s structure.
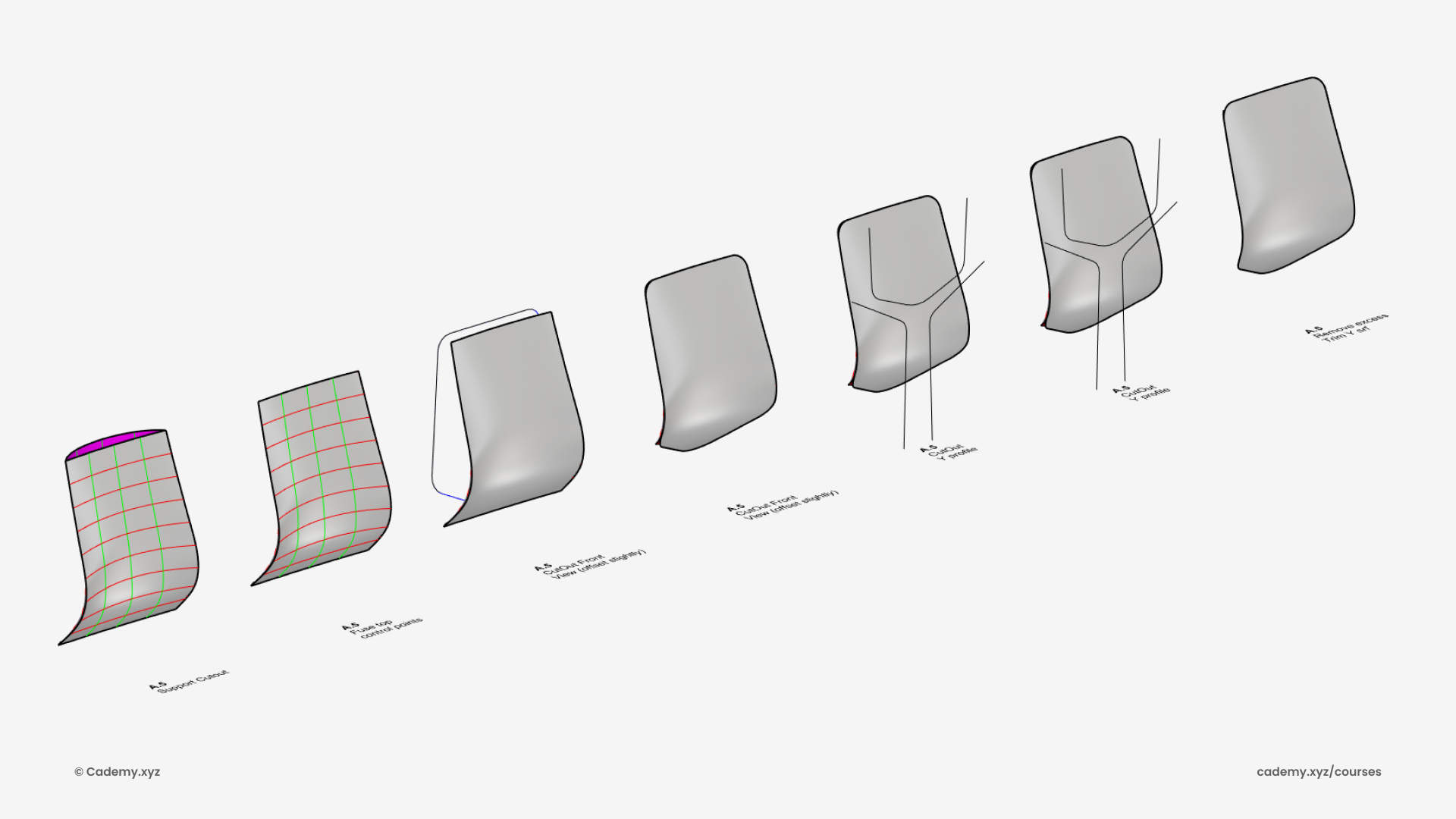
Step 4: Seat & Frame Integration
8. Connect the Y cutout to the seat frame with BlendSrf.
9. Add thickness by scaling the PolySurface and connecting with Loft.
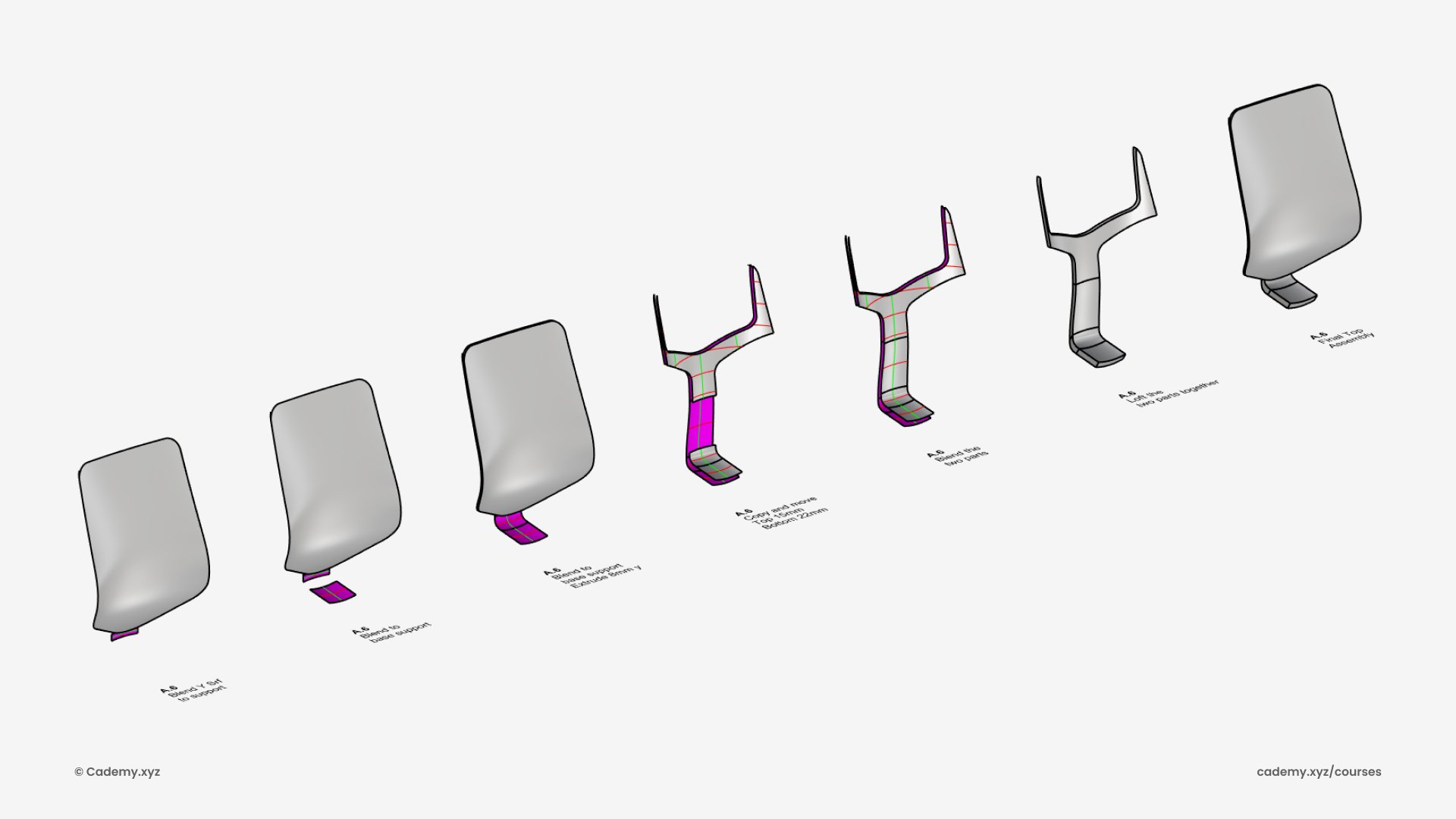
Step 5: Cushion Modeling
10. Create three profiles for the cushion.
11. Use Extrude, Rebuild, and BlendSrf for realistic shaping.
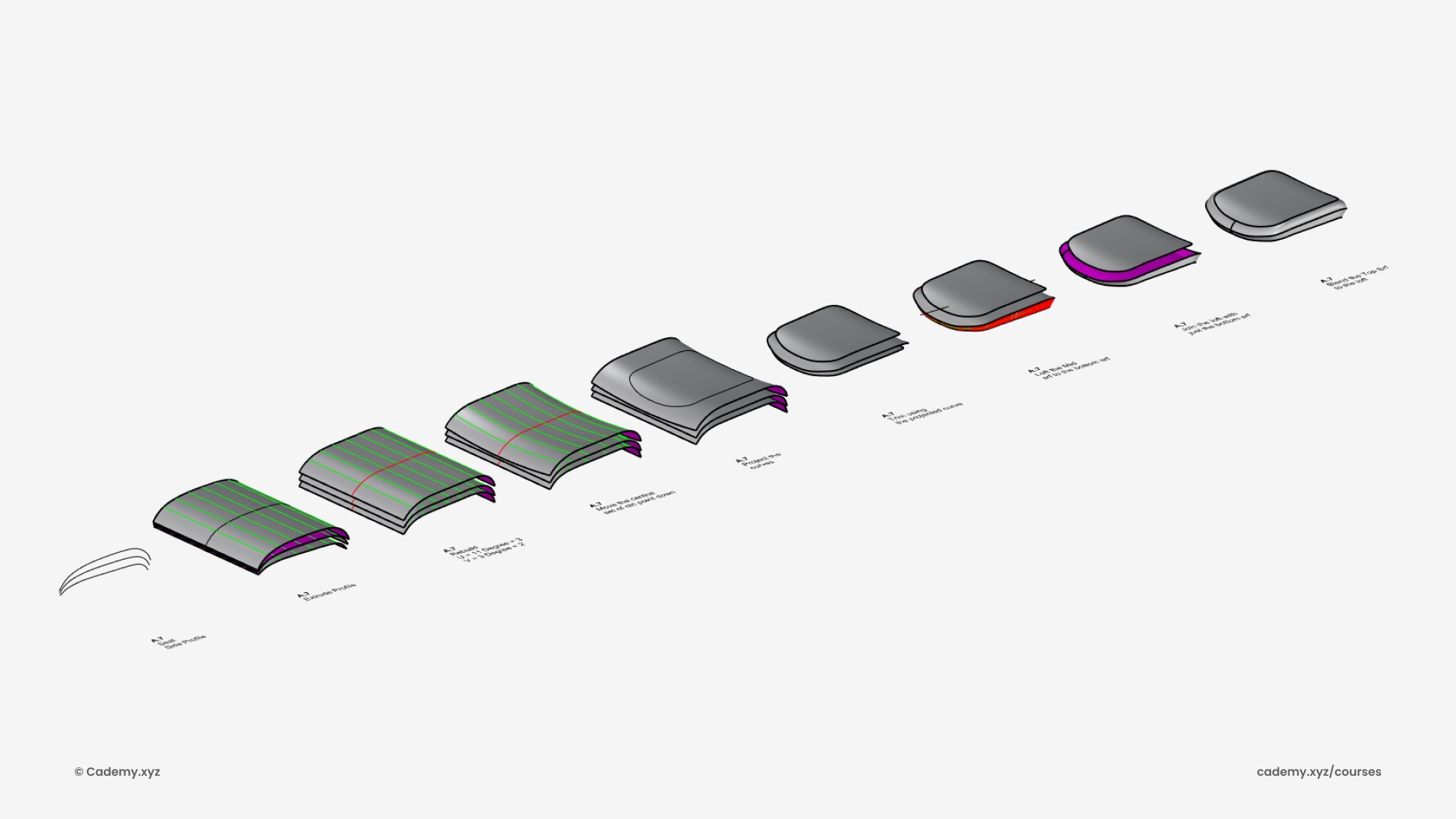
Step 6: Mechanical Assembly
12. Extrude profiles for the chair’s height and angle adjustment system.
13. Use Boolean Intersection to refine mechanical components.
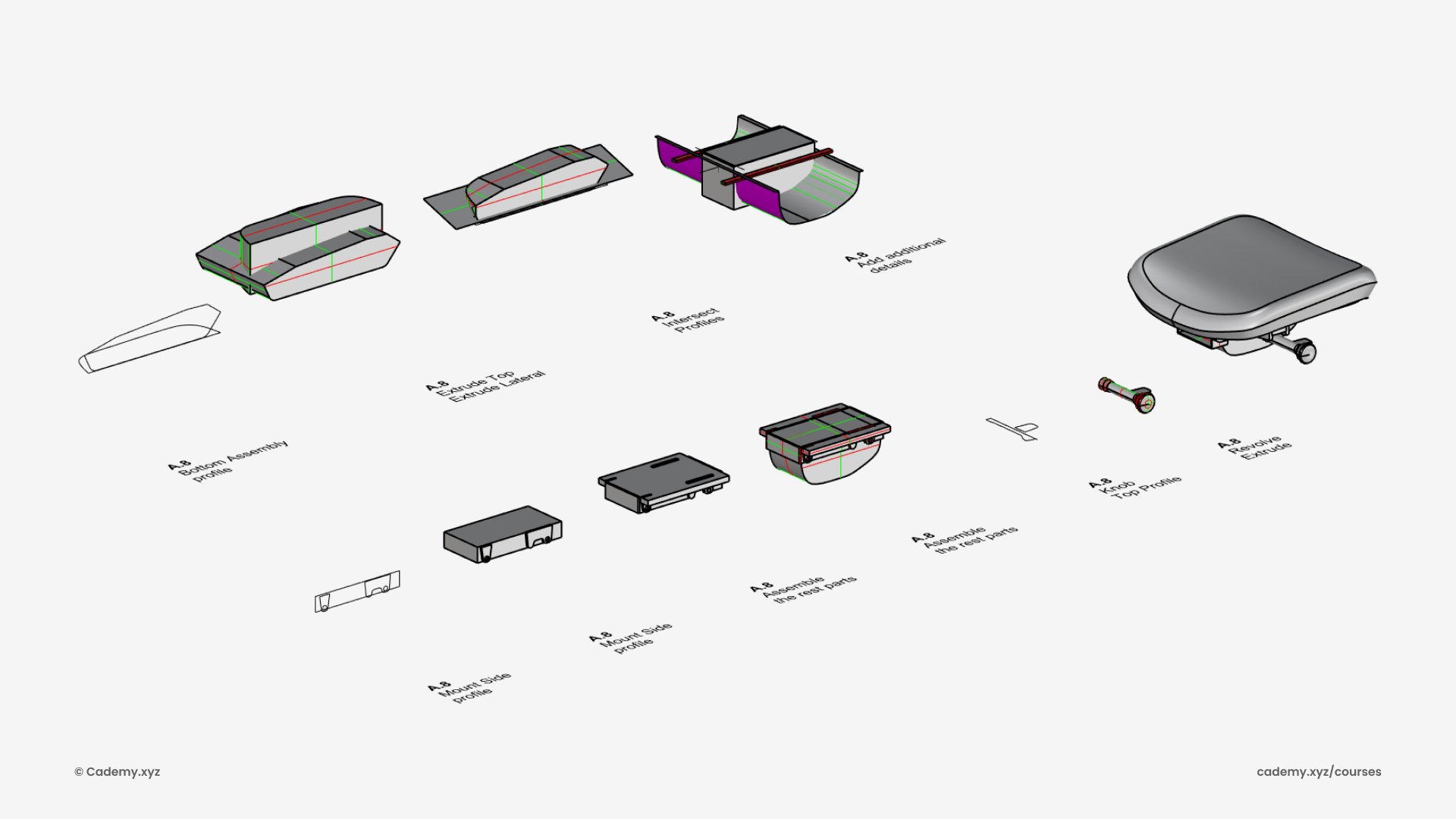
Step 7: Armrest Construction
14. Extrude profiles, split excess surfaces, and use BlendSrf.
15. Apply Fillet for smooth transitions.
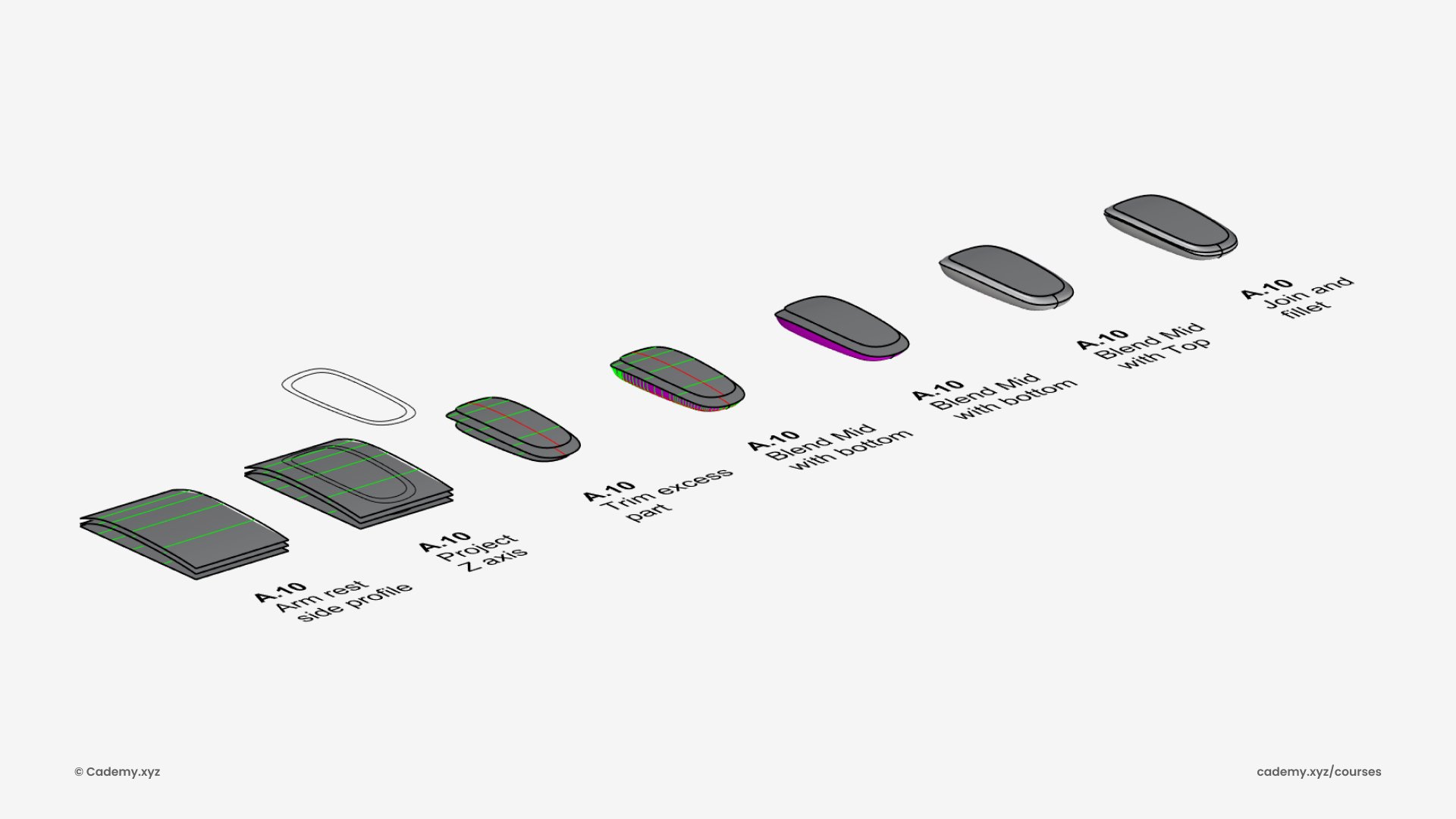
Step 8: Arm Support
16. Structure created with extrusions and BlendSrf.
17. Rotate 35º for ergonomic inclination.
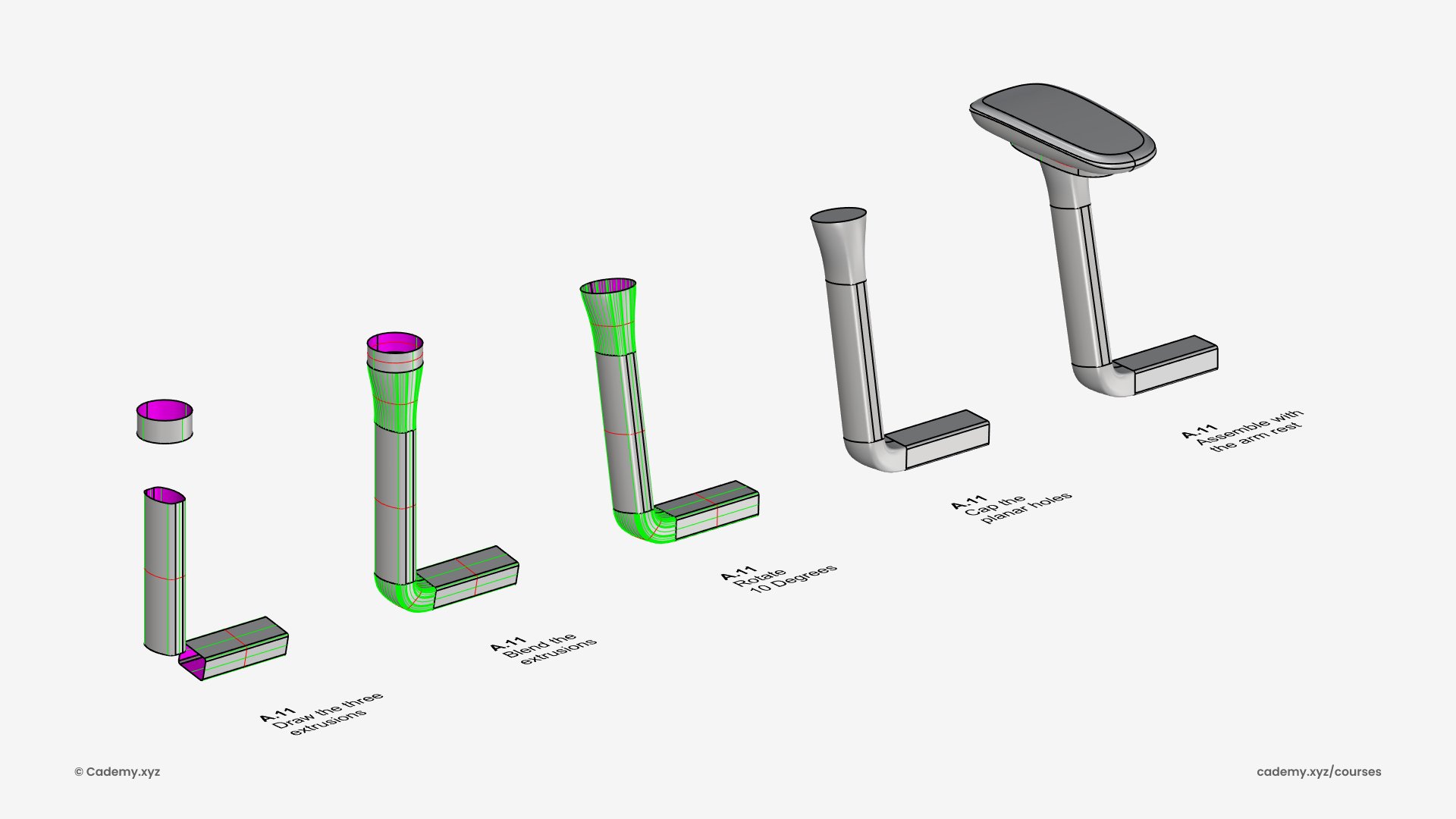
Step 9: Wheel Assembly
18. Use Polar Array for five evenly spaced wheels.
19. Apply Revolve and Boolean operations for support frames.
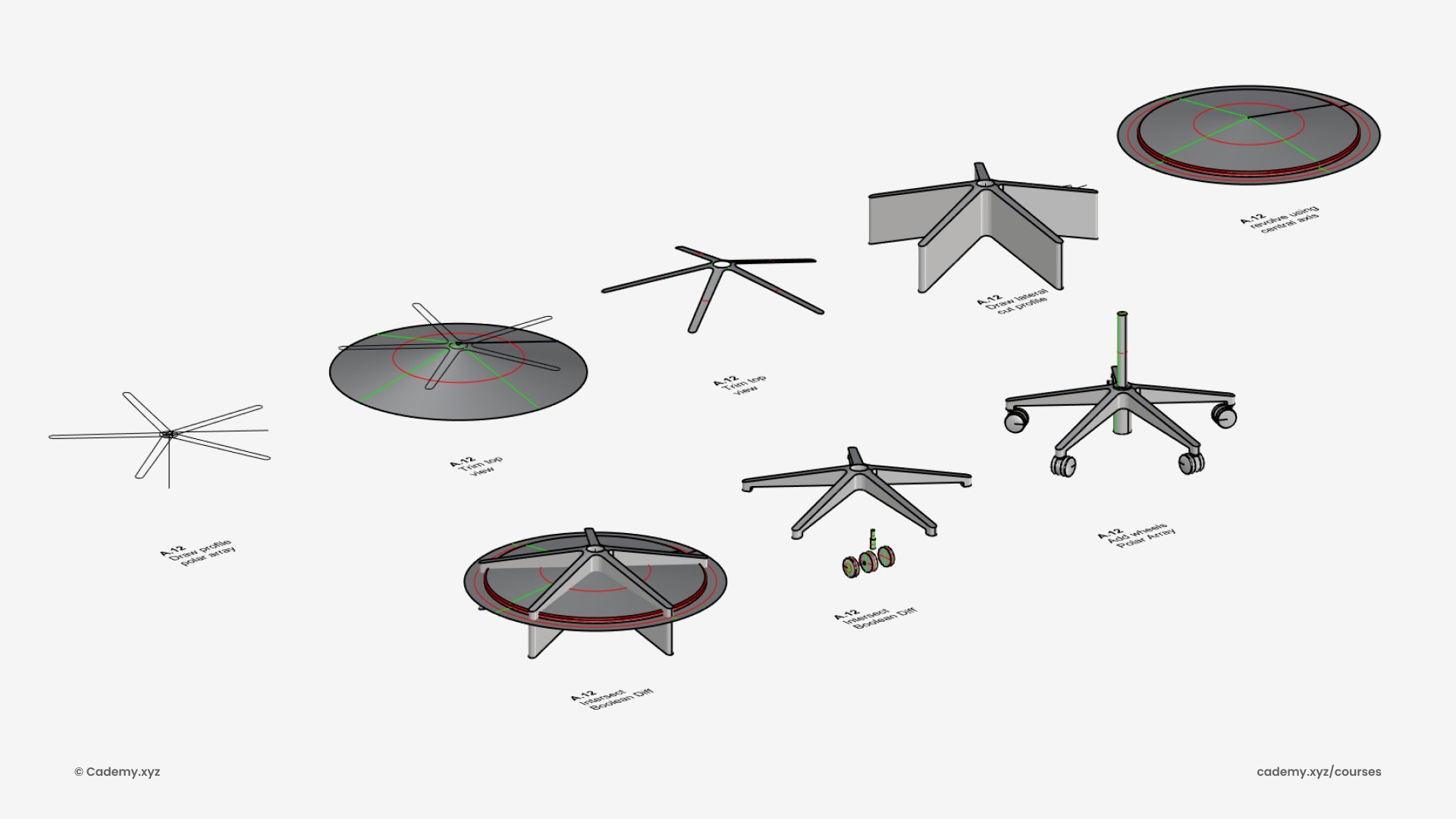
Step 10: Final Assembly
20. Position and align all chair components.
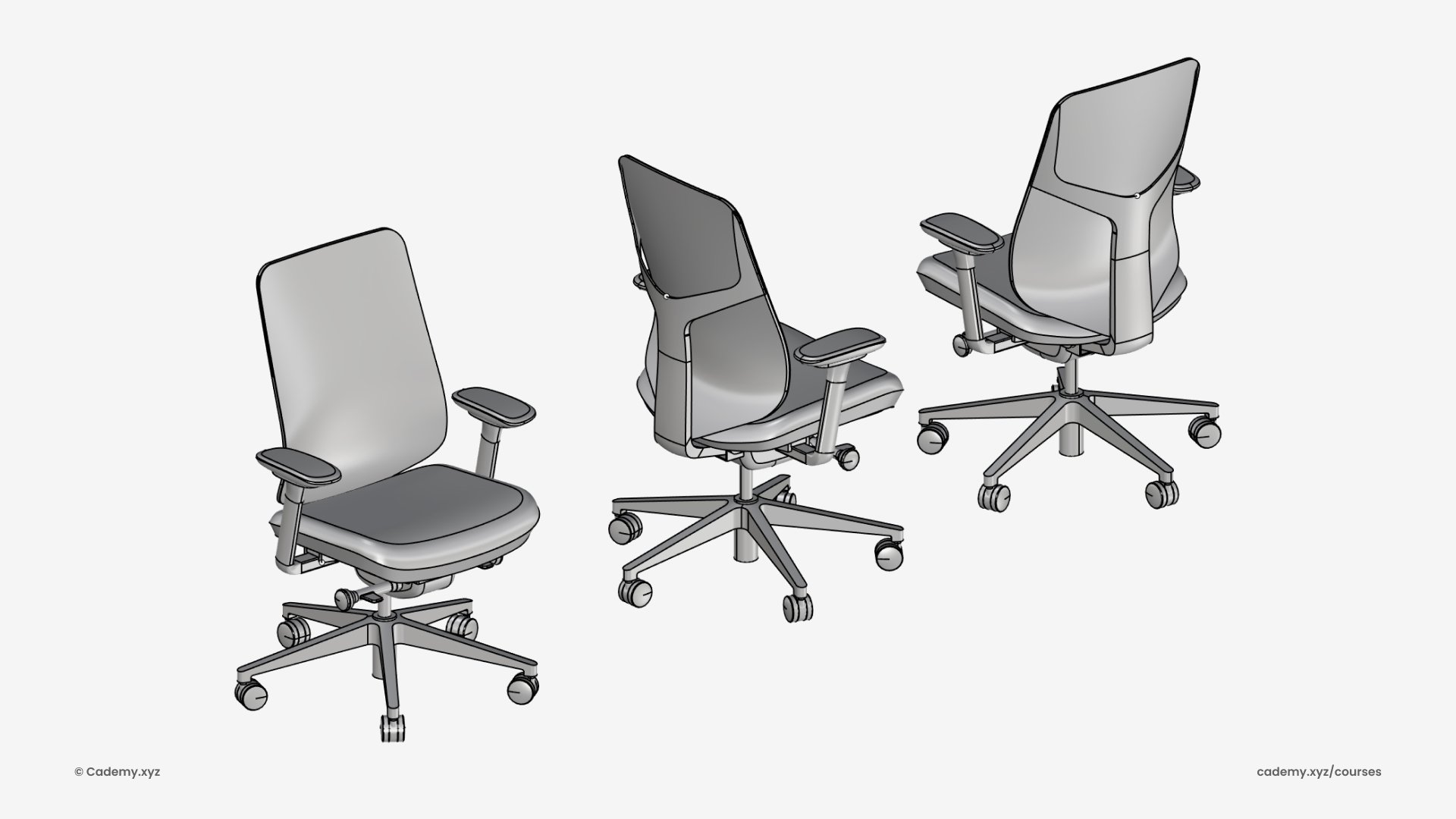
Step 11: Mesh Texturing
21. Extract the back support surface.
22. Use the Lunchbox plugin to refine the isocurves.
23. Apply the staggered panel component for a dynamic texture.
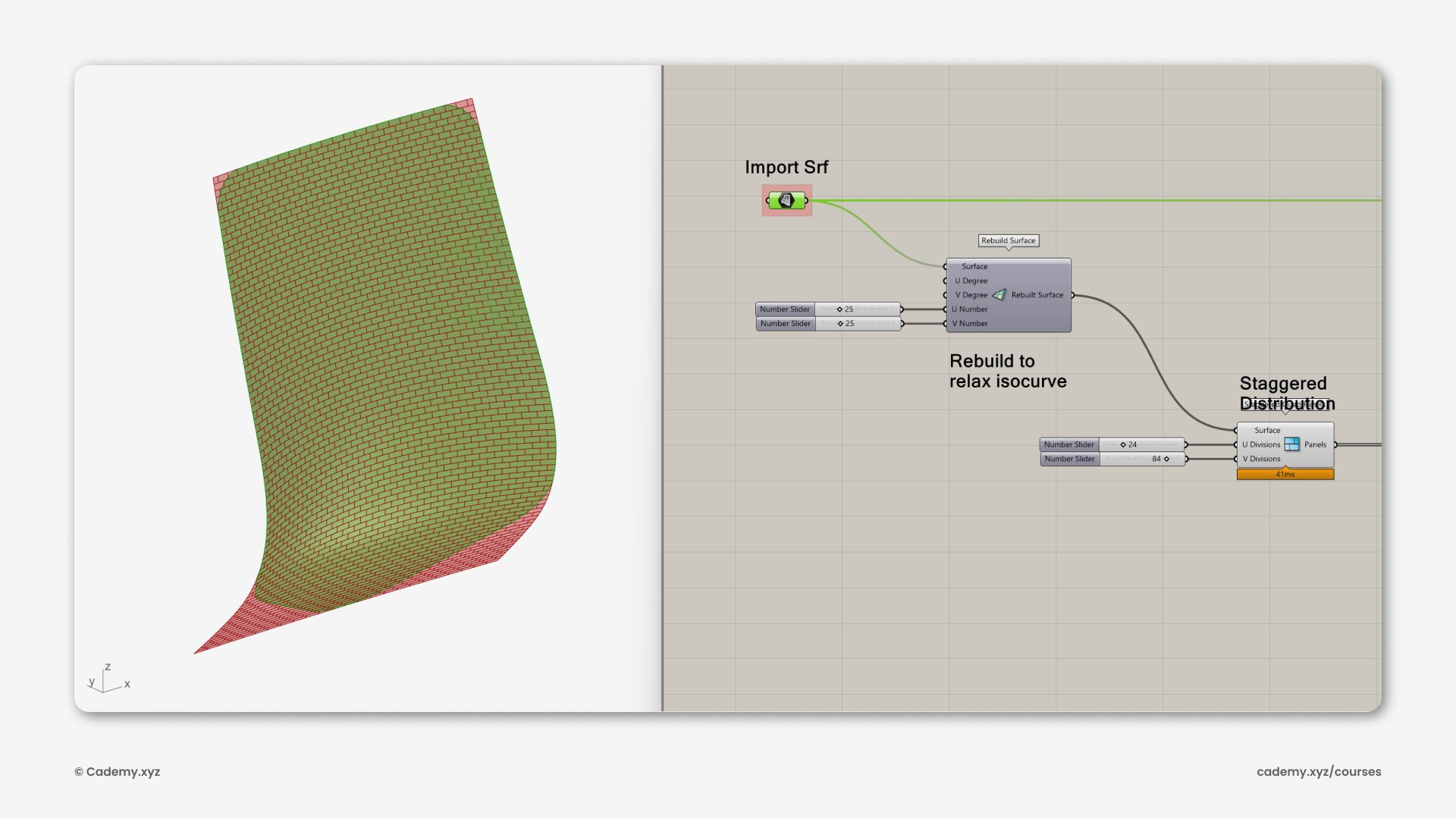
Step 12: Attractor Influence
24. Extract surface center and normal using Evaluate Surface.
25. Reparameterize the surface and apply an attractor geometry with Pull Point.
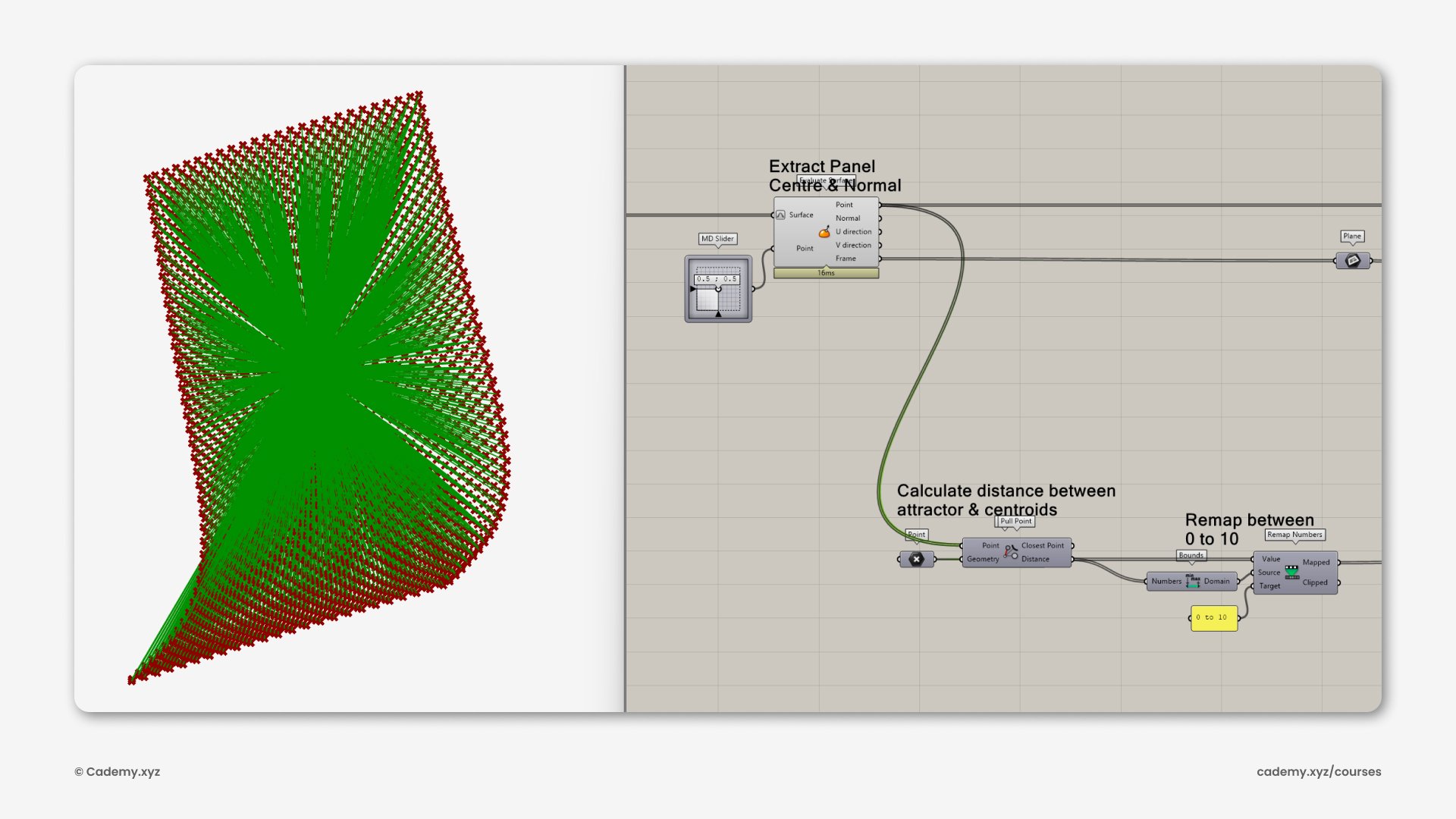
Step 13: Patterned Perforation
26. Use Tween Curves to interpolate between two profiles.
27. Assign curves dynamically using List Item based on the attractor field.28. Extrude and perform Boolean Difference for perforation texture.
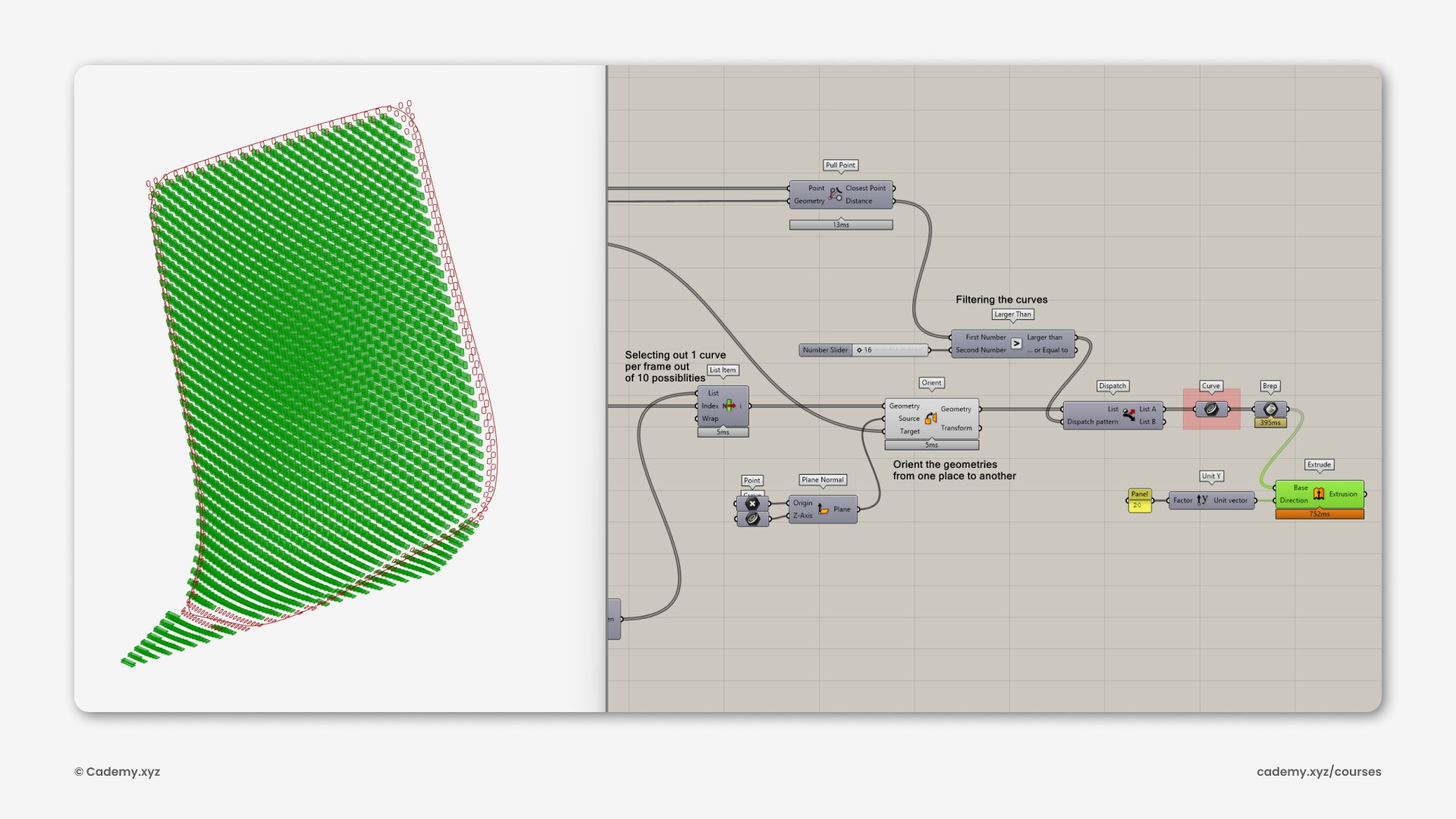
Step 14: Import & Material Setup
29. Open the .3dm file in Keyshot.
30. Apply Solid Glass material with 90% white color.
31. Adjust roughness (0.05) for a frosted effect.
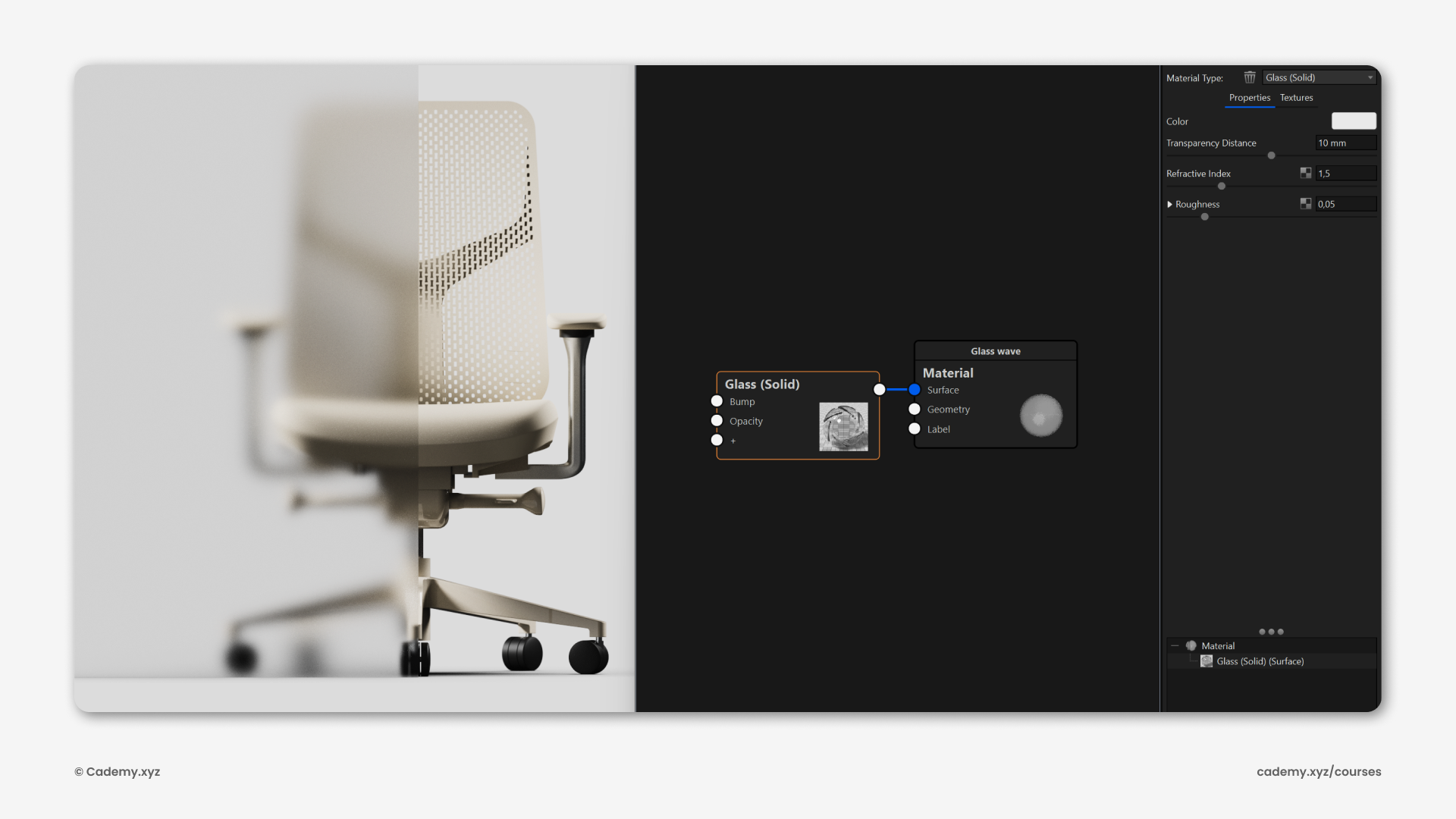
Step 15: Advanced Texturing
32. Use the Mesh procedural node for vertical line effects.
33. Control spacing and thickness, applying the texture as a Bump parameter.
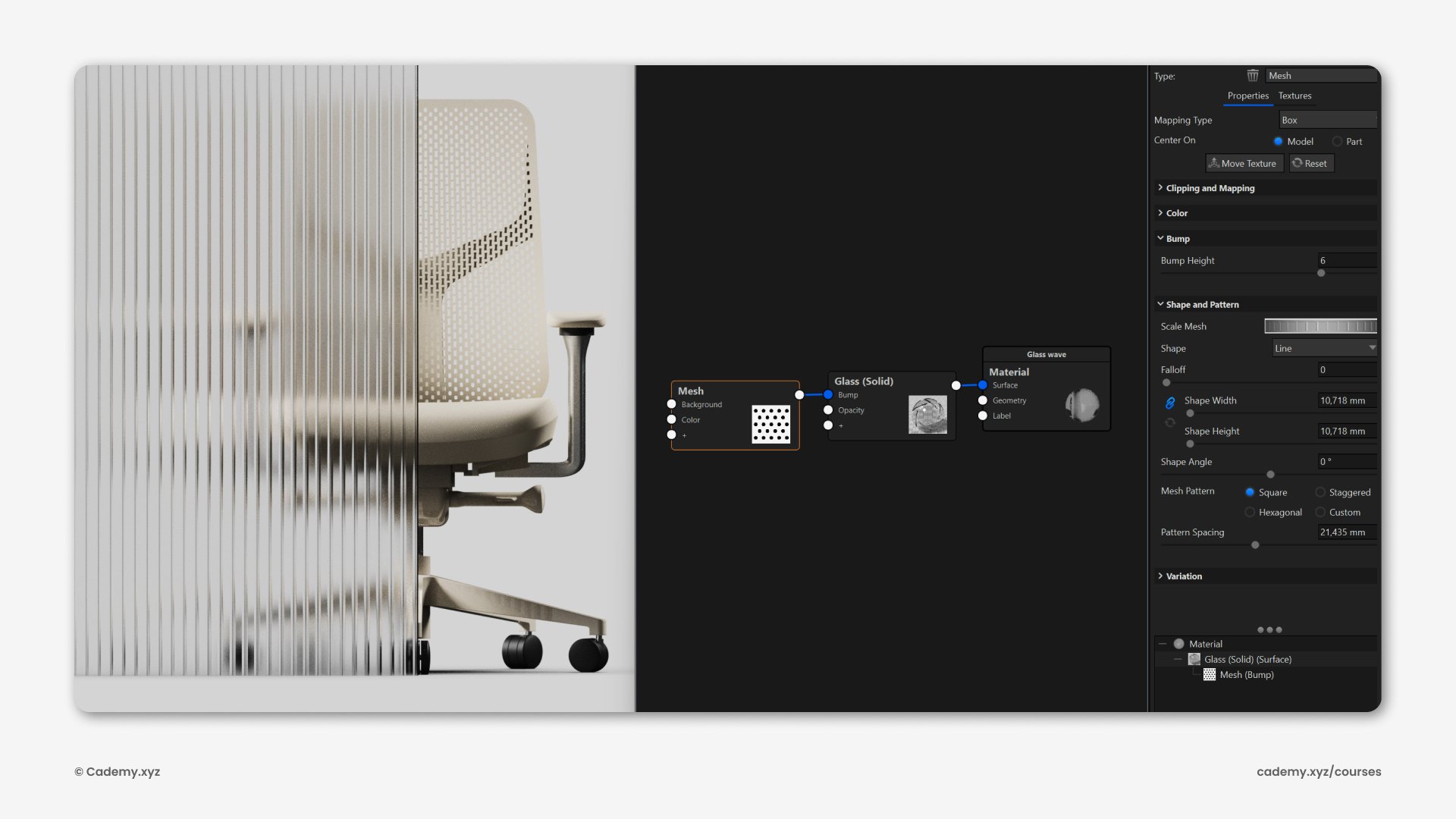
Software Used
- Rhinoceros 3D
- Grasshopper 3D
- Keyshot
- ChituBox
3D Printing Process
- Export STL files.
- Compatible with SLA + FDM printing techniques.
Thank you for reading ❤️
Don’t miss out, enroll today.
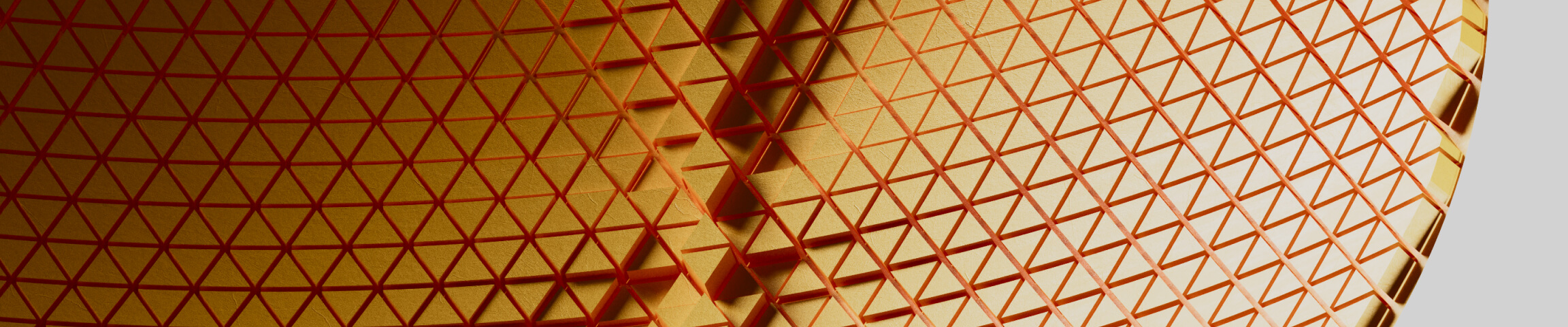