Rhinoceros - Grasshopper - Keyshot | Workflow 4
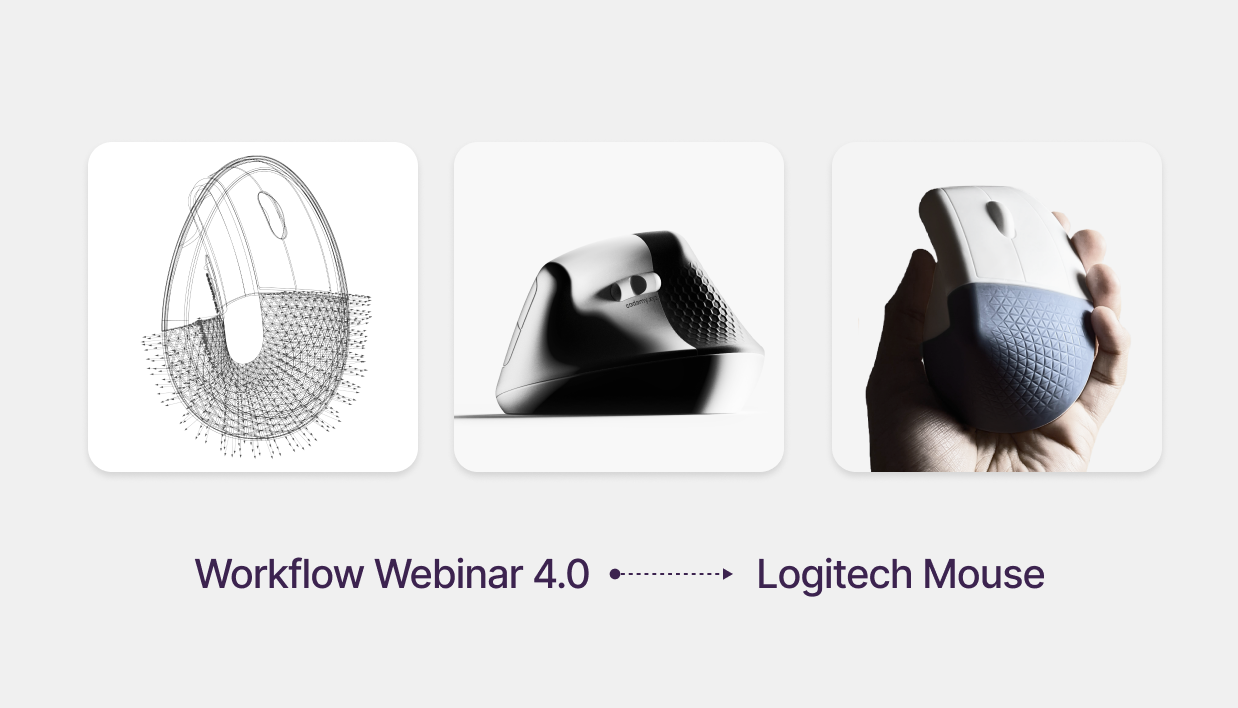
Download Files: cademy.xyz/webinar4
You can watch the full webinar here or at the end of this post.
Logitech Lift Ergo Mouse
The Logitech Lift is an ergonomic and productivity-focused mouse, designed to reduce wrist strain while offering customizable DPI settings.
According to Design Partners, the MX Vertical mouse was developed through extensive ergonomic research, including:
- Multiple functional prototypes
- User tests measuring muscle strain and activity
- Identification of the optimal 57-degree resting angle to reduce wrist tension
- Achieving 10% less muscle strain and 4x less muscle activity compared to a standard mouse
At Cademy, we will CAD model this mouse and explore parametric texture variations for the grip.
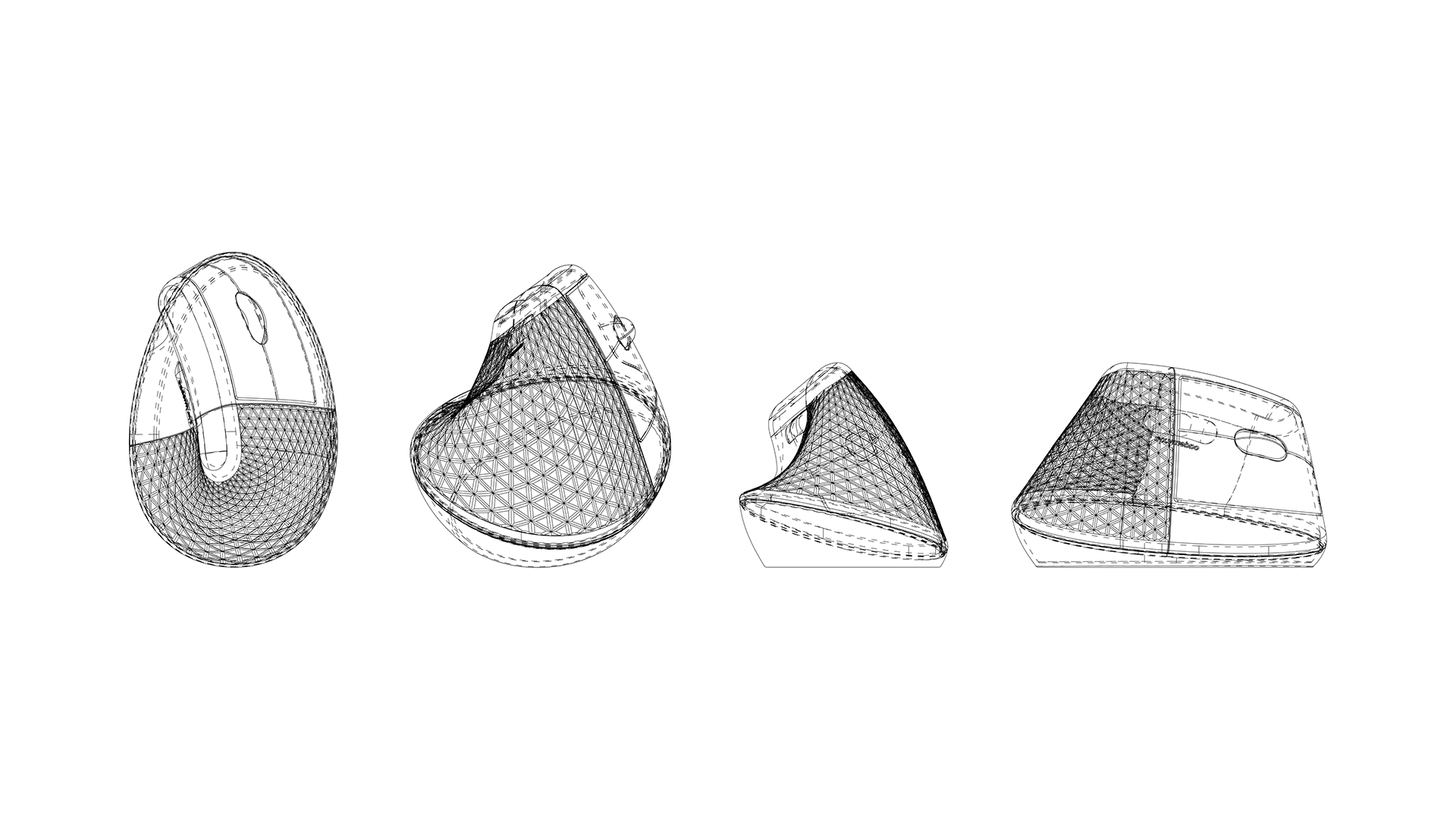
Step 1: 3D Modeling the Base Geometry
1. Open Rhinoceros 3D and set up the workspace.
2. Draw the Top Profile using NURBS curves based on the given technical dimensions.
3. Create the Lateral Cut Profile and extrude it to form the base shape.
4. Rebuild and Deform the extruded curve to project the top profile onto it.
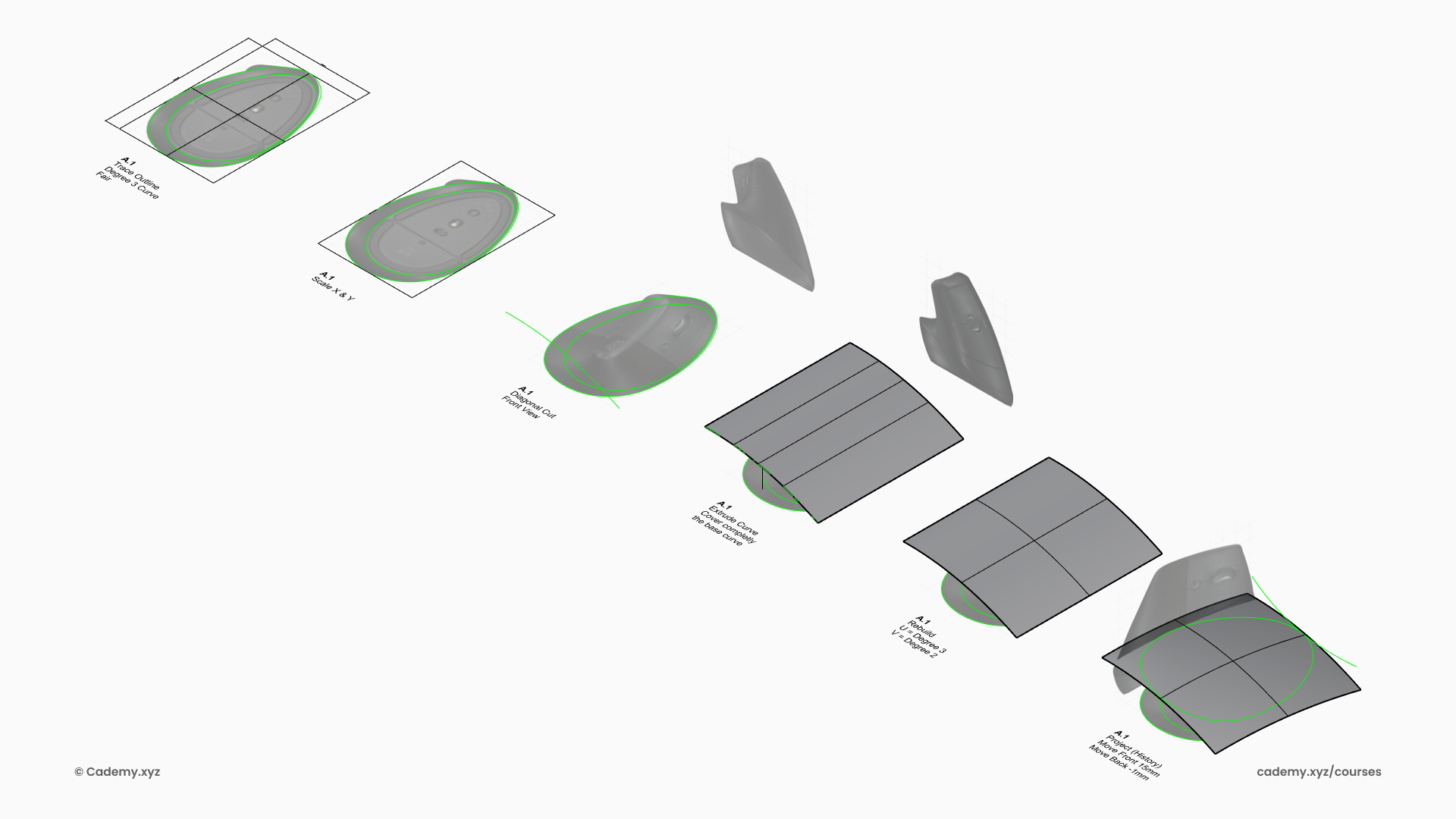
Step 2: Inner Base Profile and Surface Creation
5. Convert the Inner Base Profile into a planar (trimmed) surface.
6. Extrude the Projected Profile to define the main volume.
7. Add Four Intersection Planes to help align the connecting surfaces.
8. Blend the Surface using the BlendSrf command with G0 (positional) and G1 (tangency) continuity.
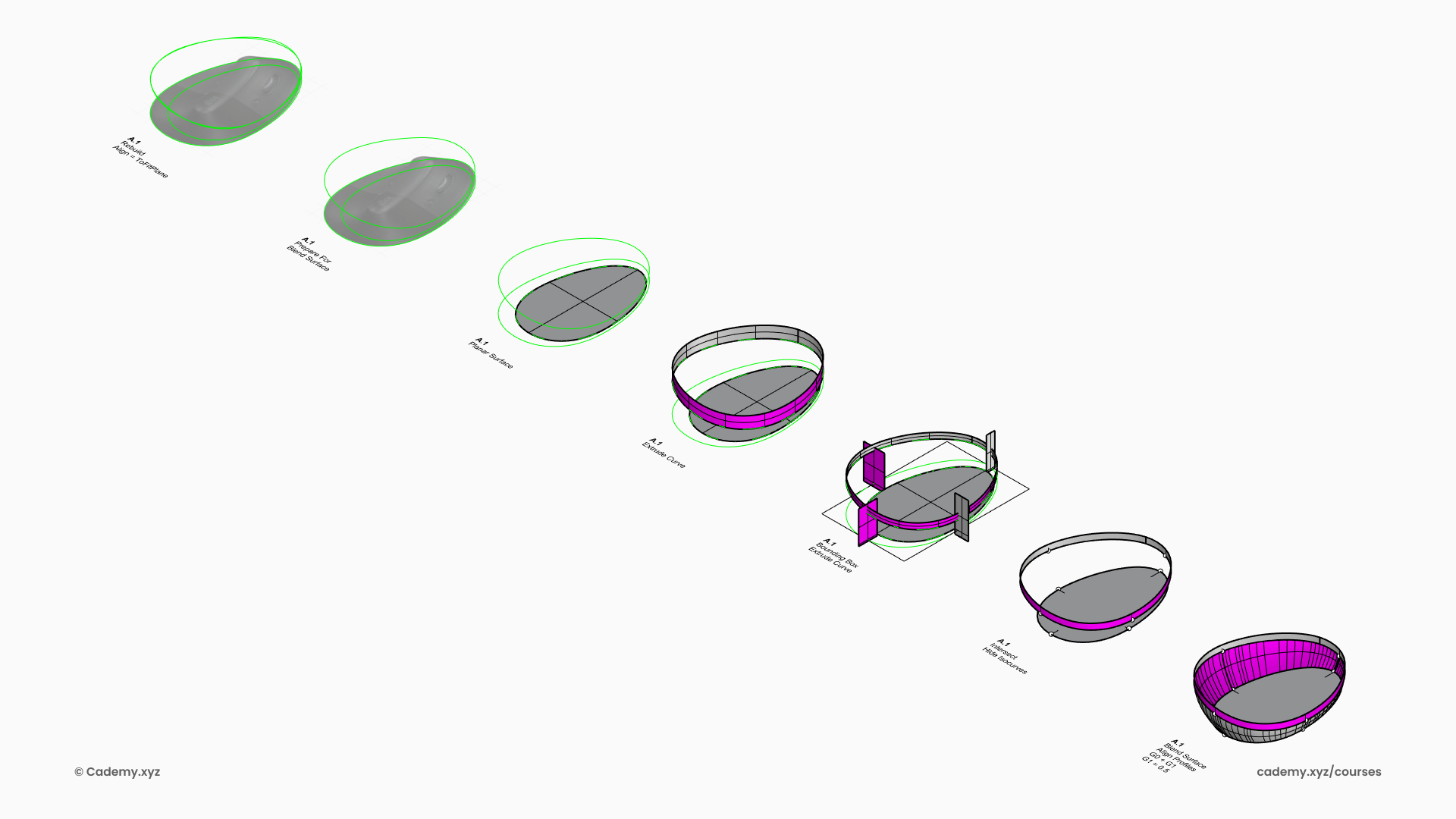
Step 3: Top Part Geometry
9. Align Curve Profiles from different views and create the intersection plane.
10. Intersect a Plane with a Pipe to generate the upper part of the mouse.
11. Trim the Excess Pipe to refine the shape.
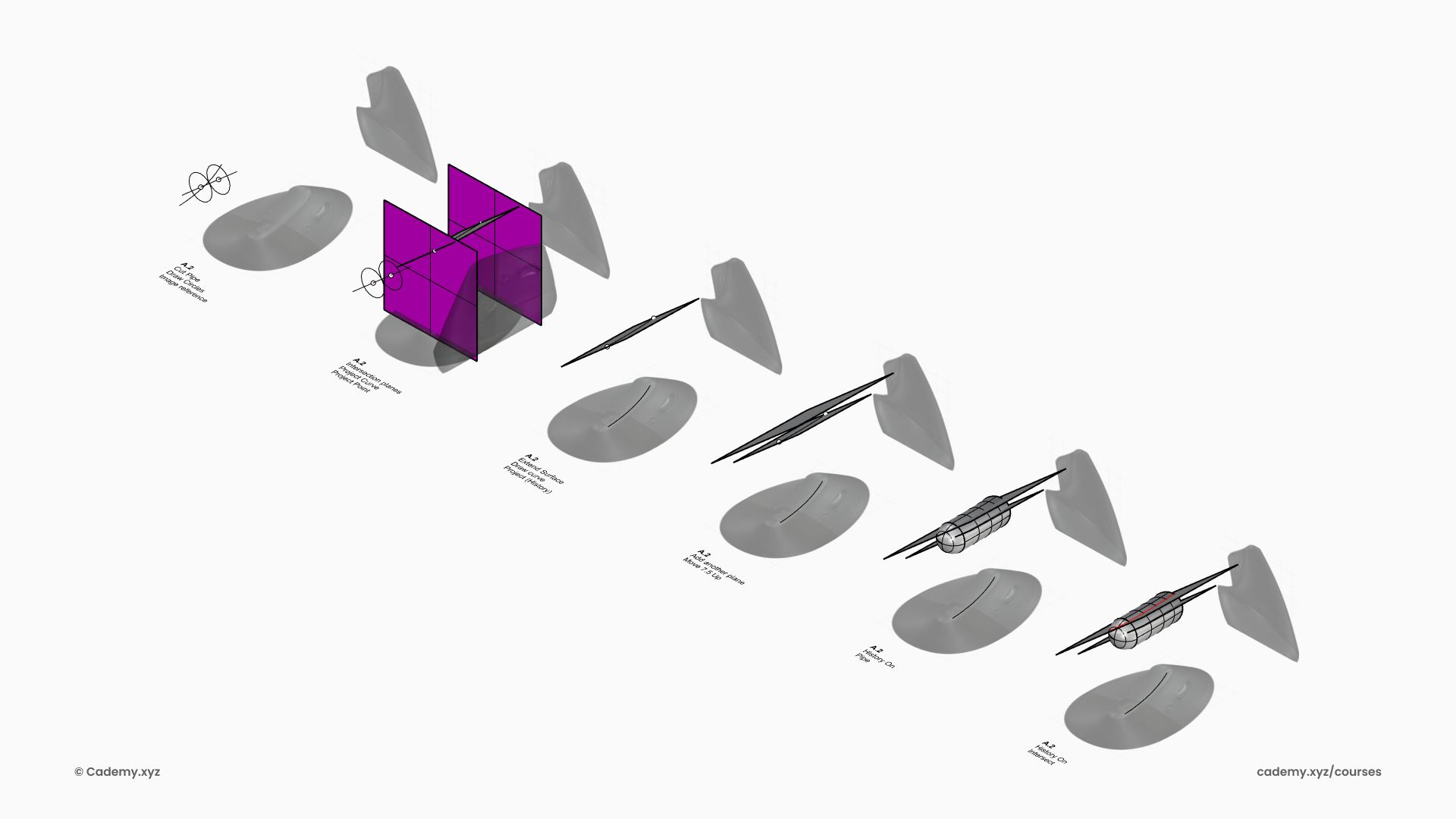
Step 4: Refining the Geometry
12. Extend the Pipe Radius and intersect it with the base blend surface.
13. Create the Lateral Surface using Sweep 2 Rails with four profiles.
14. Rebuild the Sweep to reduce surface complexity using a Degree 5 surface in U & V directions (multispan in the lateral direction).
15. Pipe the Top & Bottom Rail, then trim it from the base geometries.
16. Bridge the Trimmed Parts using the Blend Surface command.
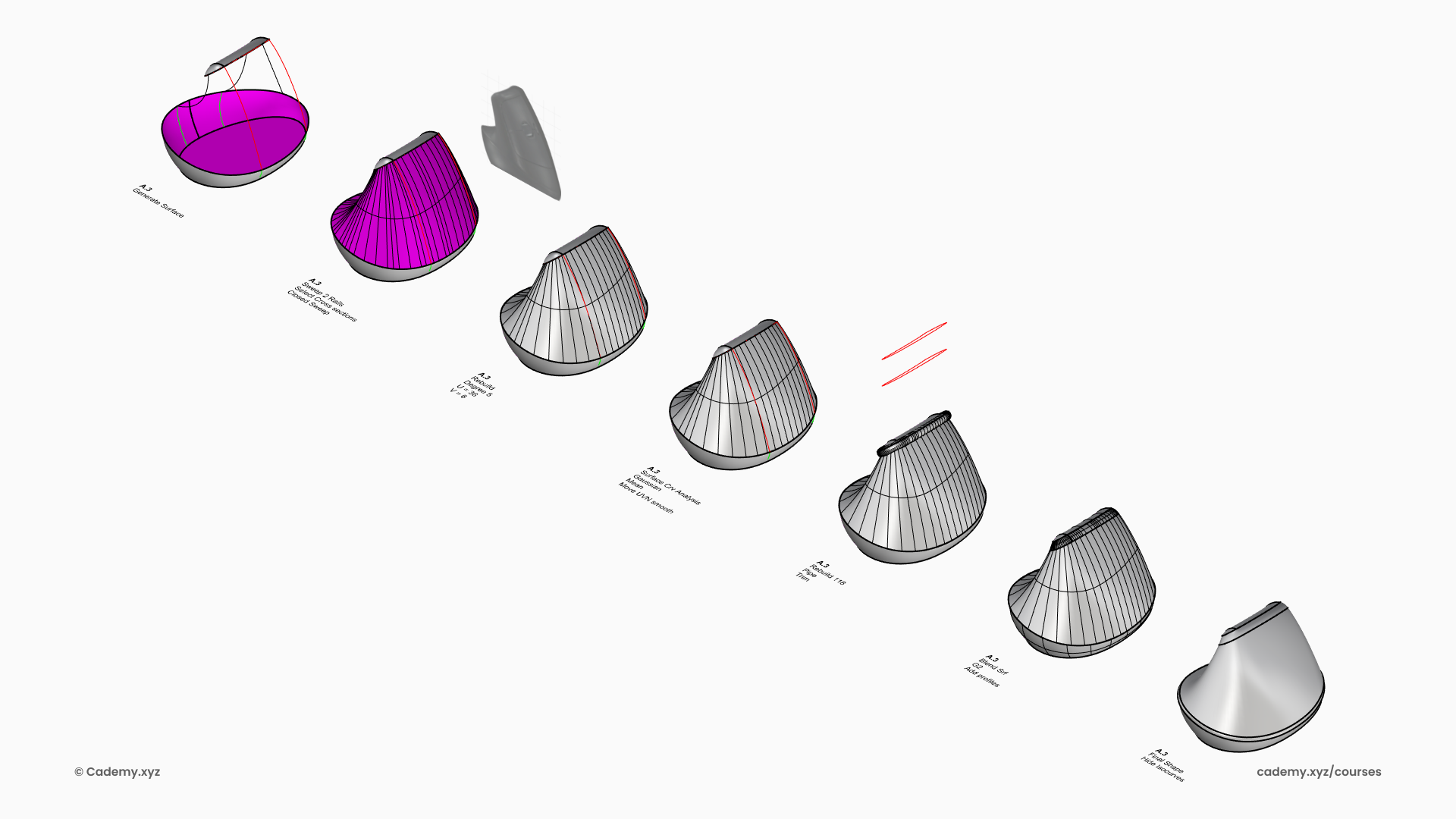
Step 5: Hollowing and Finalizing the Structure
17. Boolean Split the mouse to divide it into two halves.
18. Apply Shell or Polysurface Offset to give the walls thickness.
19. Sweep to Create the Closure Mechanism for assembly.
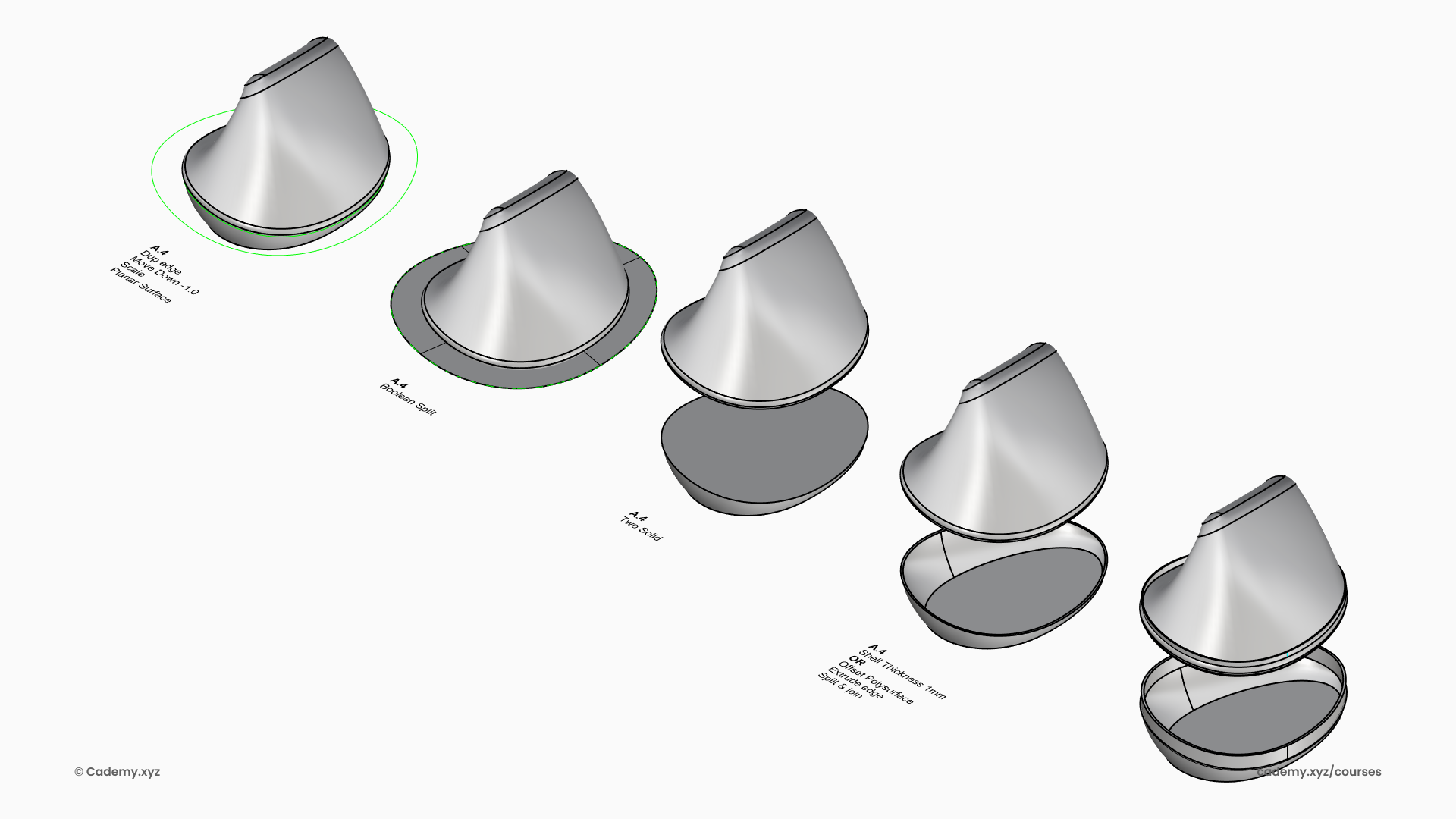
Step 6: Mouse Wheel Integration
20. Project Curves for Grooves onto the mouse body to define wheel placement.
21. Position a Cylinder for the mouse wheel and Fillet the Corners to shape it.
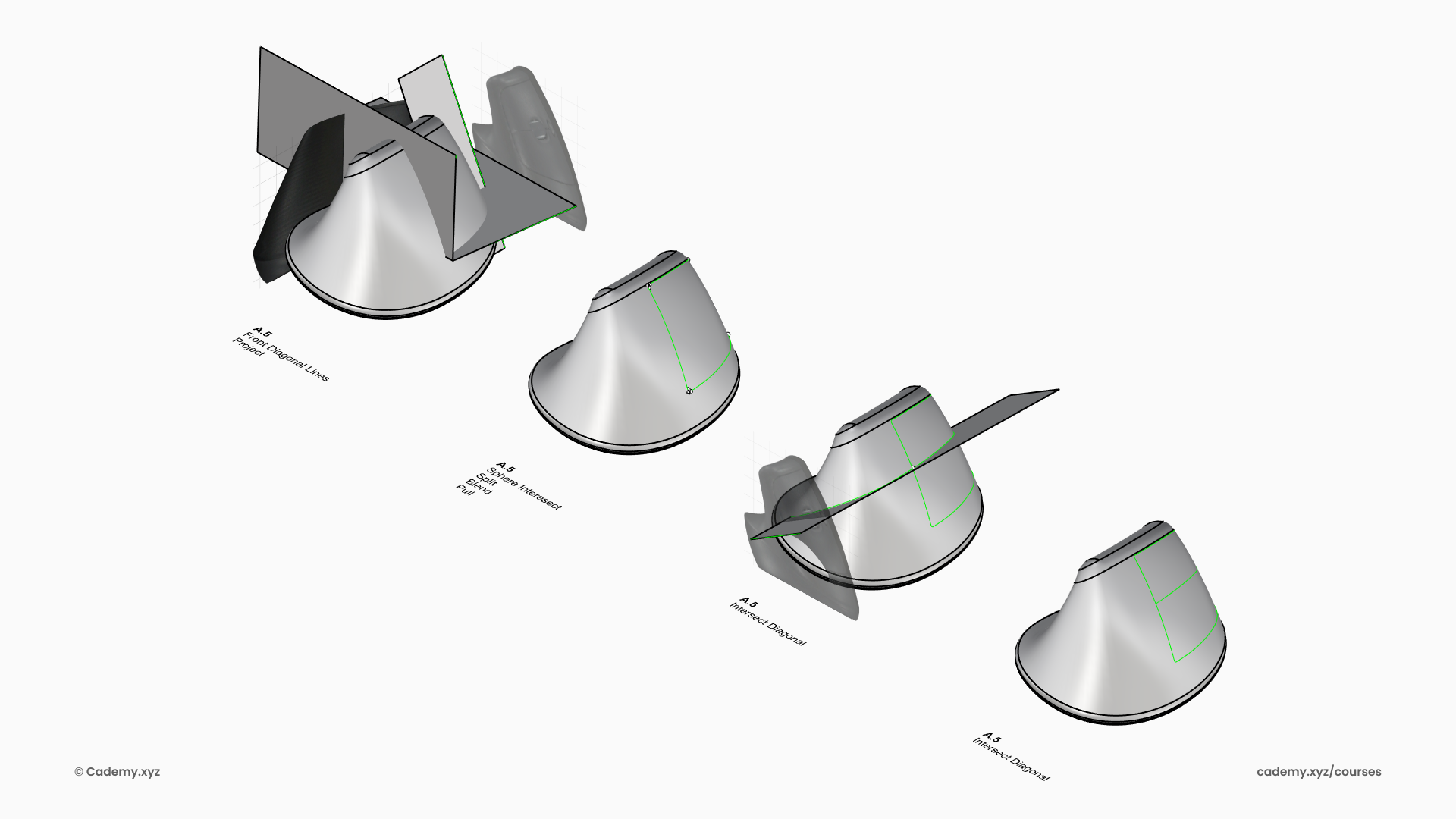
Step 7: Creating the Side Buttons
22. Pipe a Profile to define the shape of the side buttons.
23. Fillet the Corners for a smooth transition.
24. Generate a Perpendicular Pipe and split it with the button to refine the shape.
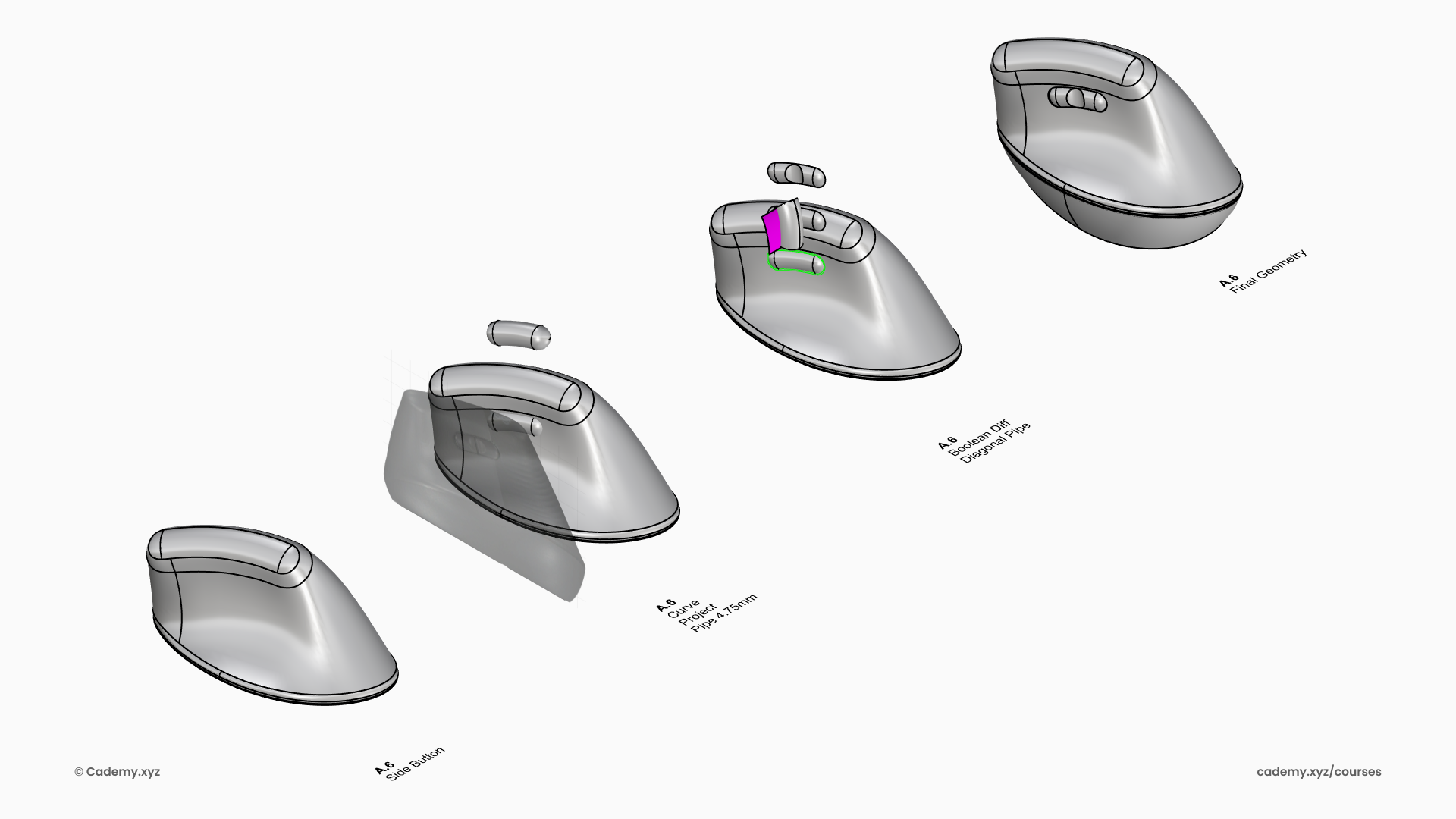
Step 8: Final Geometry Preparation and Texture
25. Explode the Polysurface to separate surfaces.
26. Split the Surface with Isocurves to define grip texture limits.
27. Import into Grasshopper and apply a parametric texture.
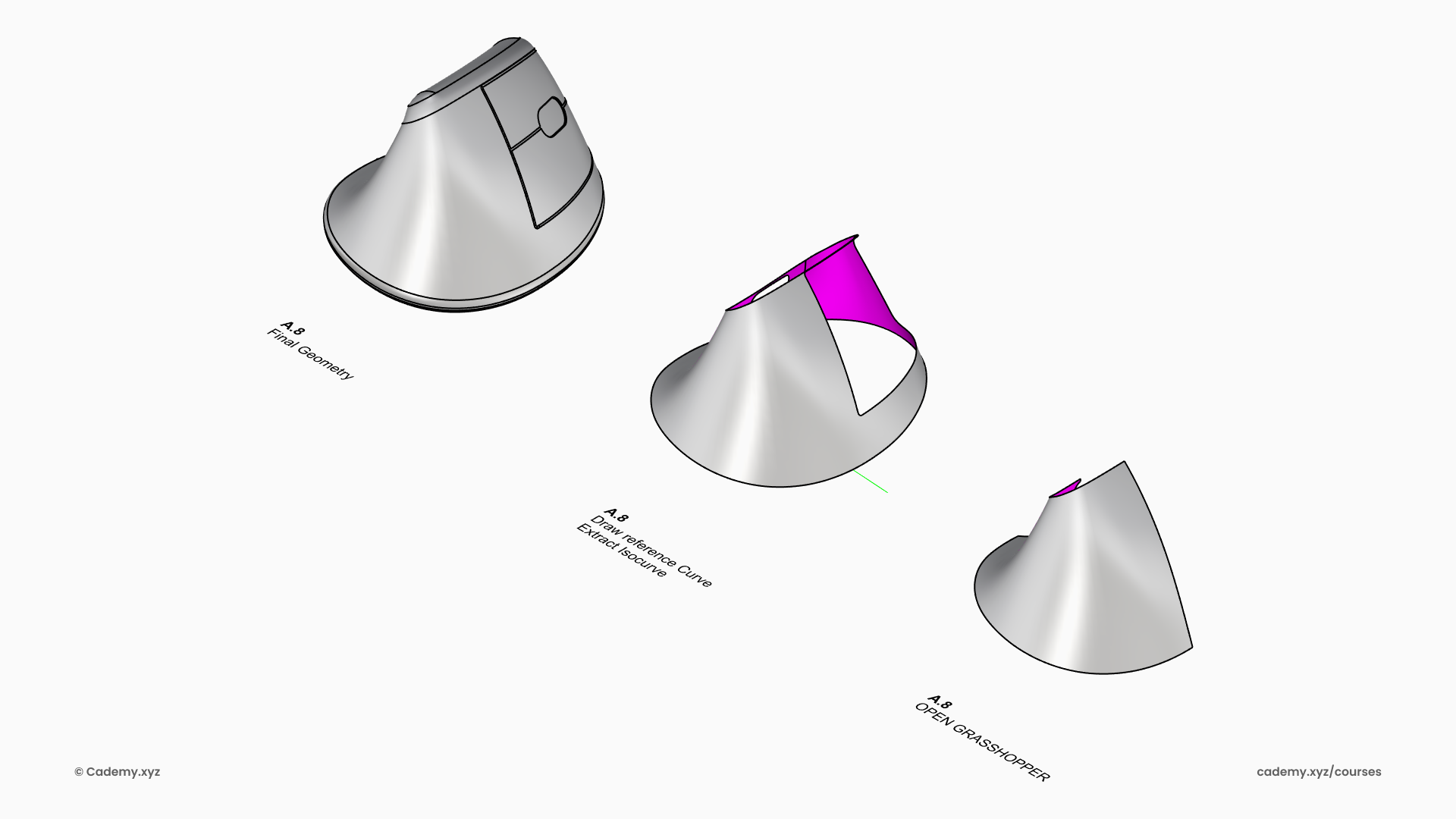
Step 9: Parametric Texture in Grasshopper
28. Apply Triangular Paneling: Use the Triangular Panel node on the base surface.
29. Extend Across Untrimmed Surface: The panels will initially extend over the entire untrimmed surface.
30. Trim to Fit: Pull the curves onto the surface and trim them to match the panel boundaries.
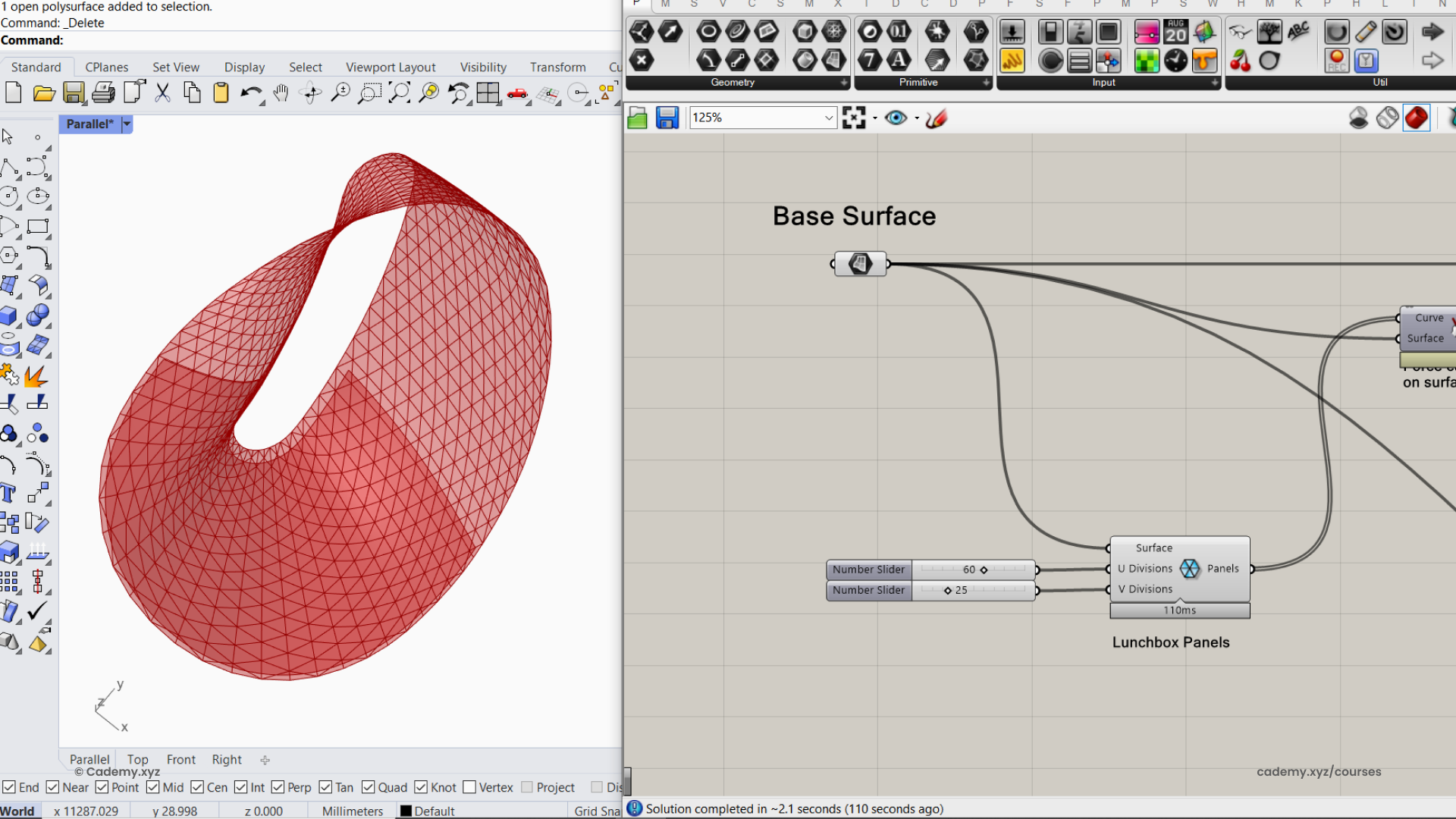
Step 10: Creating Depth Fading Effect
31. Use Surface Naked Edges as Attractor: Define the outer edges of the surface as an attractor shape.
32. Scale Panels Based on Distance: Gradually reduce the panel size based on their proximity to the attractor.
33. Move Panels Along Normal Direction: Offset the panels along the surface normal using the attractor distance parameter to create a depth variation.
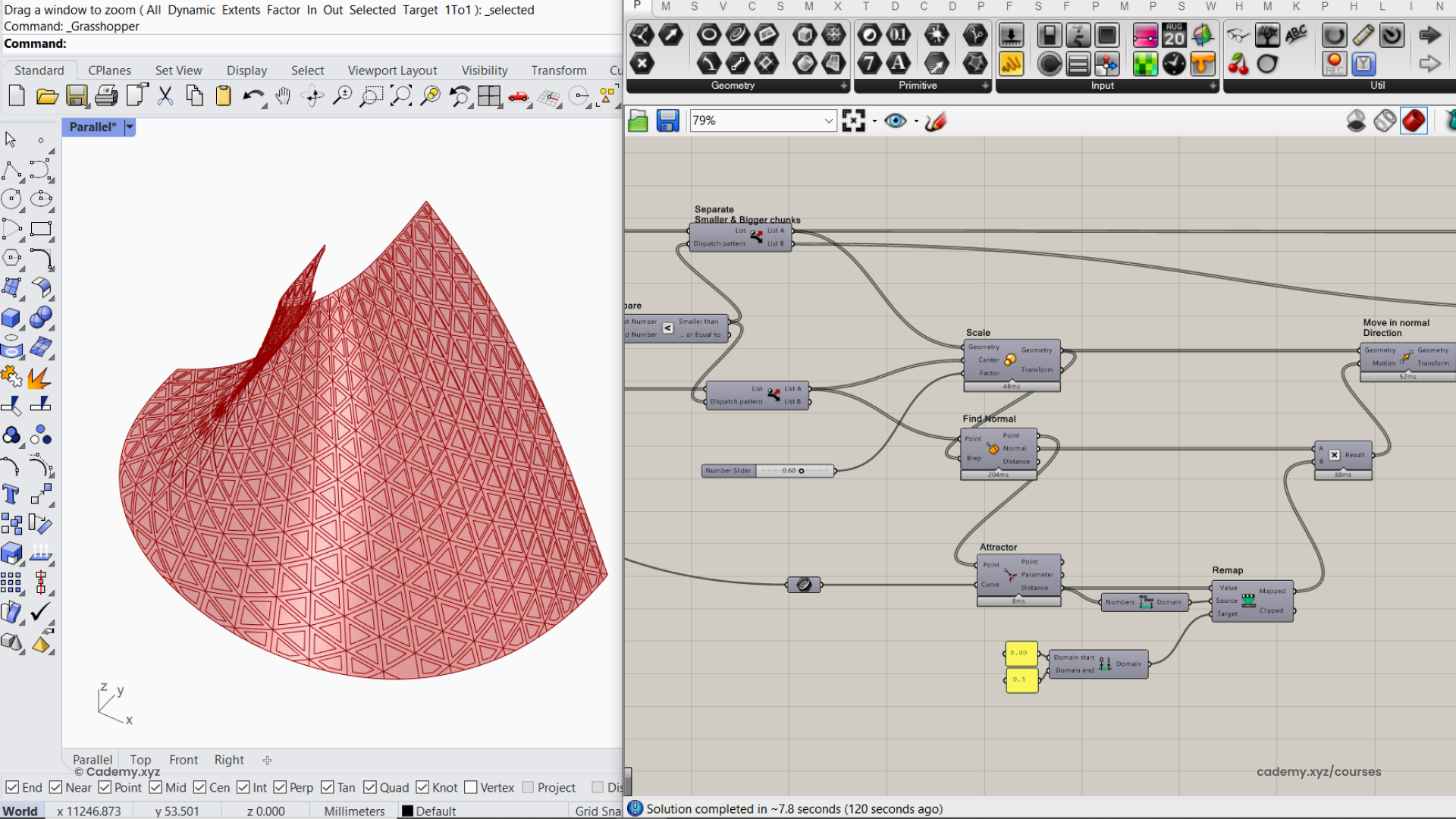
Step 11: Joining the Panels
34. Flatten the List: Before joining the panels, ensure all elements are in a single list by flattening them.
35. Join Individual Panels: Merge all the separate polysurfaces into one continuous geometry.
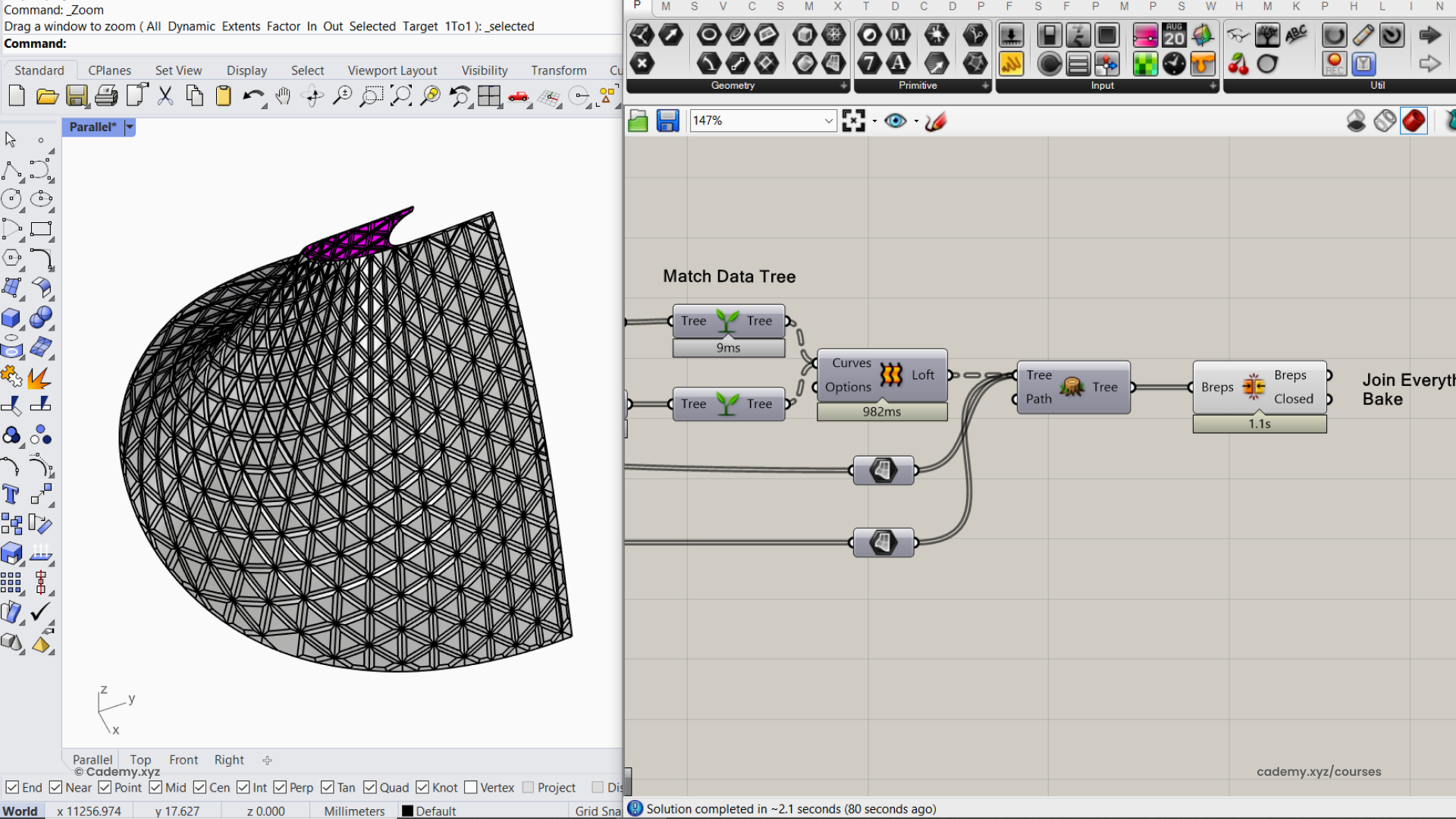
Step 12: Rendering in Keyshot
36. Open the 3D Model: Import the .3dm file (Rhinoceros native format) into Keyshot.
37. Set Up Area Lights: Create two panels and convert them into area lights.
38. Adjust Camera & Composition: Position the camera for optimal framing and composition.
39. Apply Base Material: Use a hard rough plastic material to tweak the lighting and reflections.
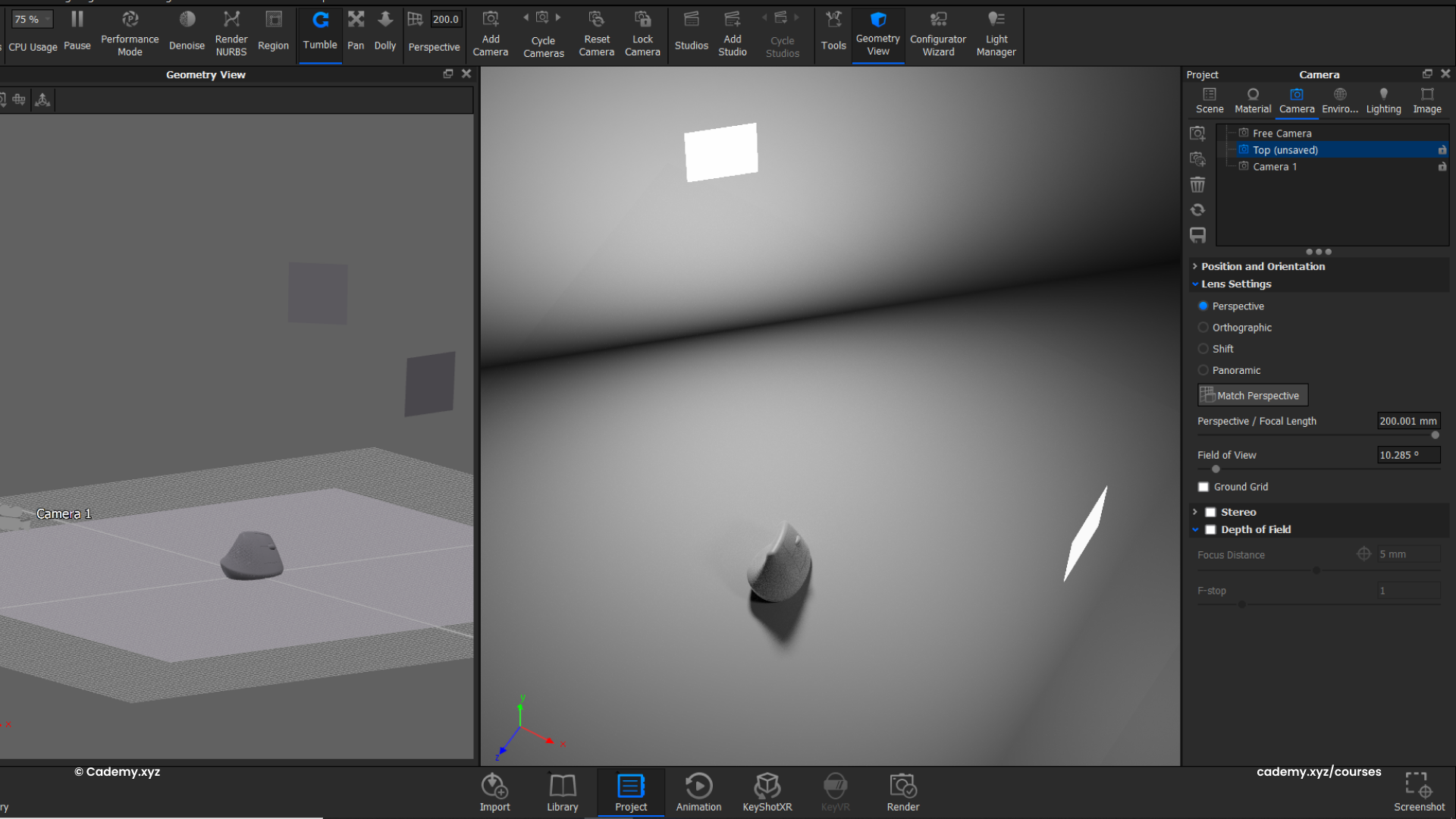
Step 13: Enhancing Material & Lighting
40. Apply Colorful Plastic Materials: Assign vibrant plastic textures to different parts of the model.
41. Set Illumination Preset: Choose the Product or Interior illumination preset for realistic lighting.
42. Add Surface Imperfections: Use the Material Graph workflow in Keyshot to introduce minor surface flaws.
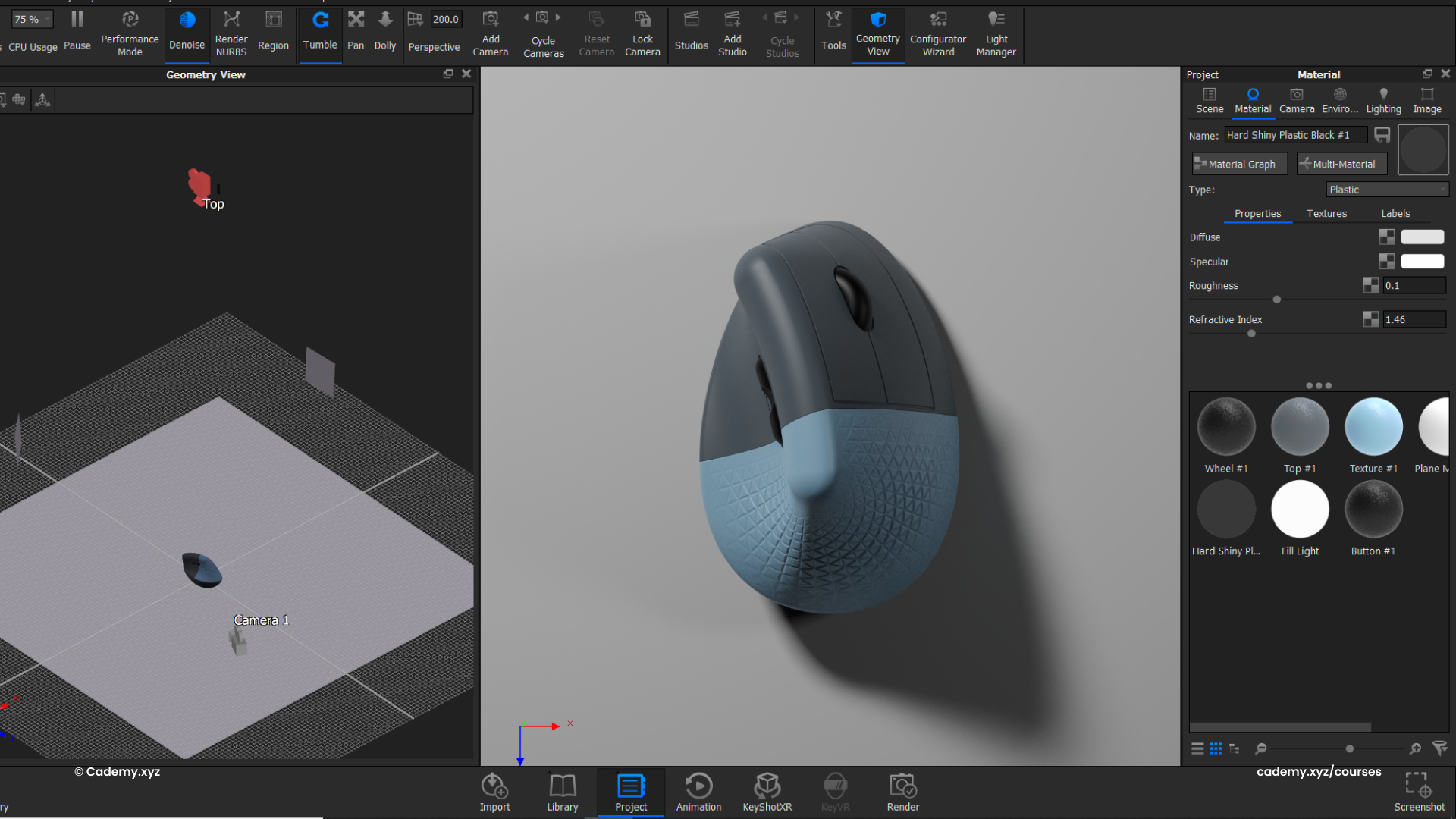
Step 14: Creating Custom HDRI Environment
43. Design a Custom HDRI: Set up a high-dynamic-range environment with colorful lights.
44. Add Metallic Material with Iridescent Effect: Introduce a metallic finish with an iridescent sheen to enhance the color reflections.
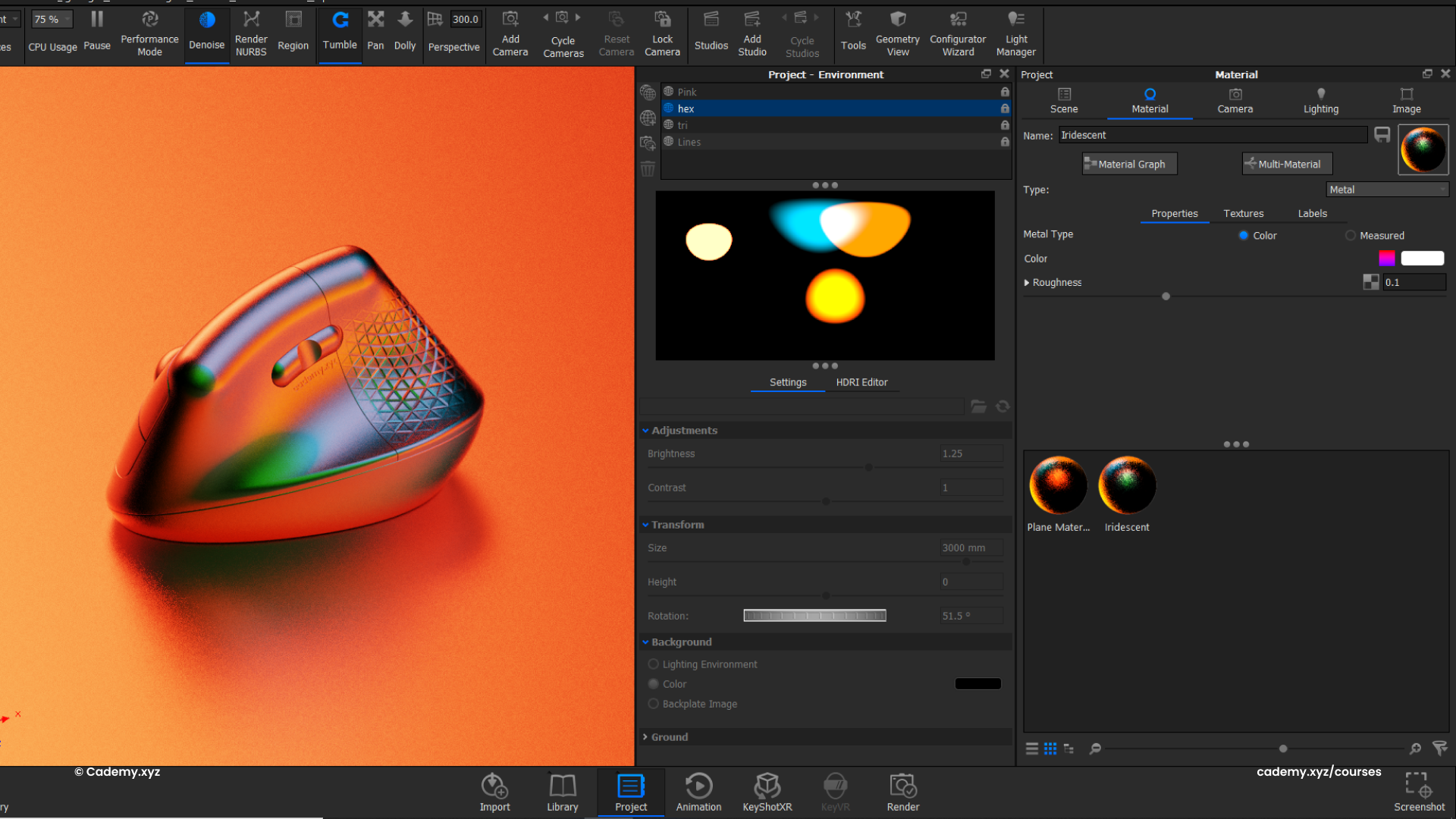
Workflow Breakdown
A. Rhinoceros
- A.1 Image Scaling, Layer Setup & Color Organization
- A.2 Base Curve & Surface Creation
- A.3 Top Curve & Surface Definition
- A.4 Merging & Cleaning (Pipe Fillet)
- A.5 Shelling & Lip Design
- A.6 Detailed Refinements
- A.7 Grasshopper Preparation
B. Grasshopper
- B.1 Basics (Interface, Cables, Reference Geometry)
- B.2 Workflow Overview
- B.3 Paneling for Grip Texture
- B.4 Attractor-based Depth Variation
- B.5 Surface Trimming & Lofting
- B.6 Assembly & Keyshot Preparation
C. Keyshot
- C.1 Introduction (Interface, Environment, Workflow Overview)
- C.2 Model Import & NURBS Data Handling
- C.3 Clay Render Setup
- C.4 Camera Configuration
- C.5 Lighting Setup (Physical & HDRI)
- C.6 Material Assignments
- C.7 Render Settings Optimization
- C.8 Post-Processing (Photoshop Demo)
D. 3D Printing
- D.1 STL Export for 3D Printing
- D.2 SLA & FDM Printing Techniques
Thanks for reading ❤️
Don’t miss out, enroll today.
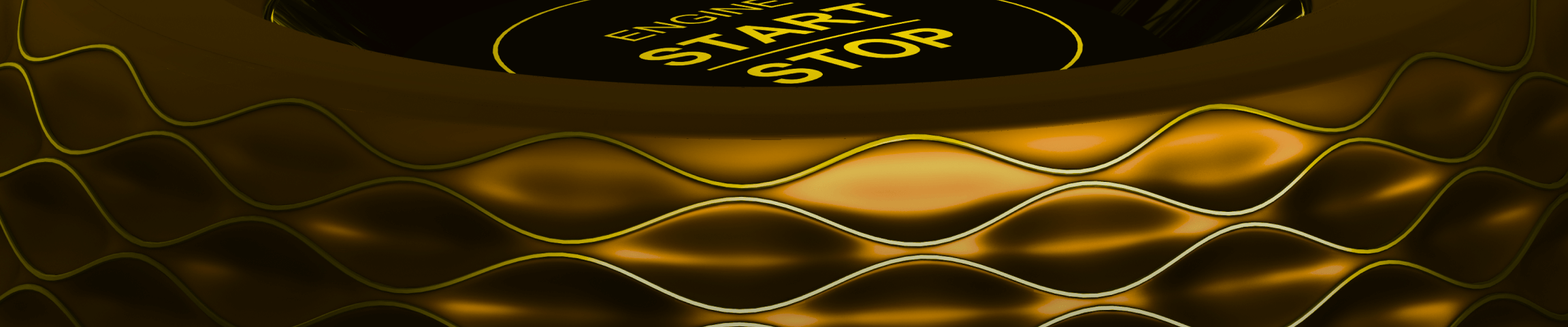