How to Model a POC Helmet in Rhino, Grasshopper & Keyshot
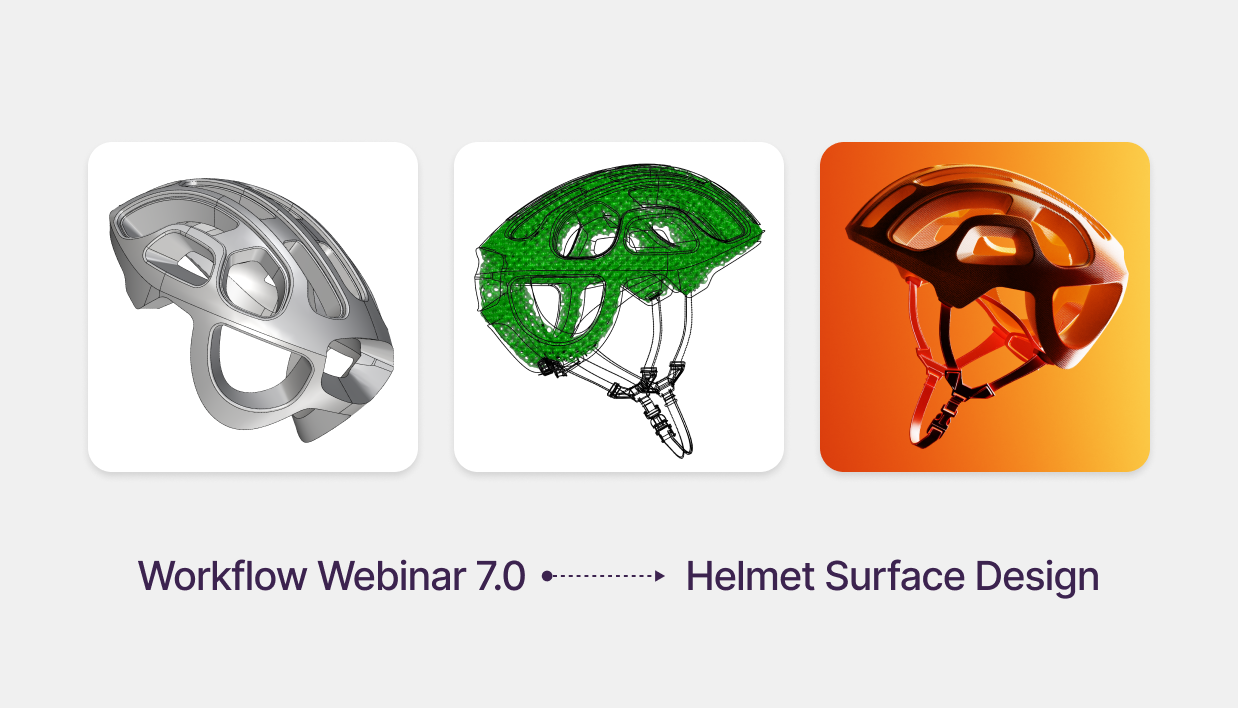
Download Files: cademy.xyz/webinar7
In this session, we explored how to model a POC helmet with internal gyroid lattice structures for impact absorption. This workflow is applicable beyond helmets—automotive parts, consumer products, and structural components all benefit from these techniques.
- High-quality surface modeling in Rhino using NURBS topology
- Generating parametric lattice structures in Grasshopper
- Rendering animations & cross-section views in Keyshot
This workflow applies to a variety of complex, functional geometries beyond helmets, including automotive parts and product design.
Tools & Plugins
Software:
- Rhino 3D – For precise surface and solid modeling
- Grasshopper – For generating gyroid lattices and parametric forms
- Keyshot – For realistic rendering & animation
Essential plugins:
- Global Edge Continuity – To check surface continuity in Rhino
- Weaverbird – For smoothing & subdividing meshes
- Dendro – To convert lattices into solid meshes
Step 1: Building the Helmet in Rhino
Importing the 3D Scan & Creating Primary Curves
1. Imported a 3D scan of a helmet
2. Used MeshOutline to extract the silhouette
3. Create Degree 4 single-span curves for a smoothness
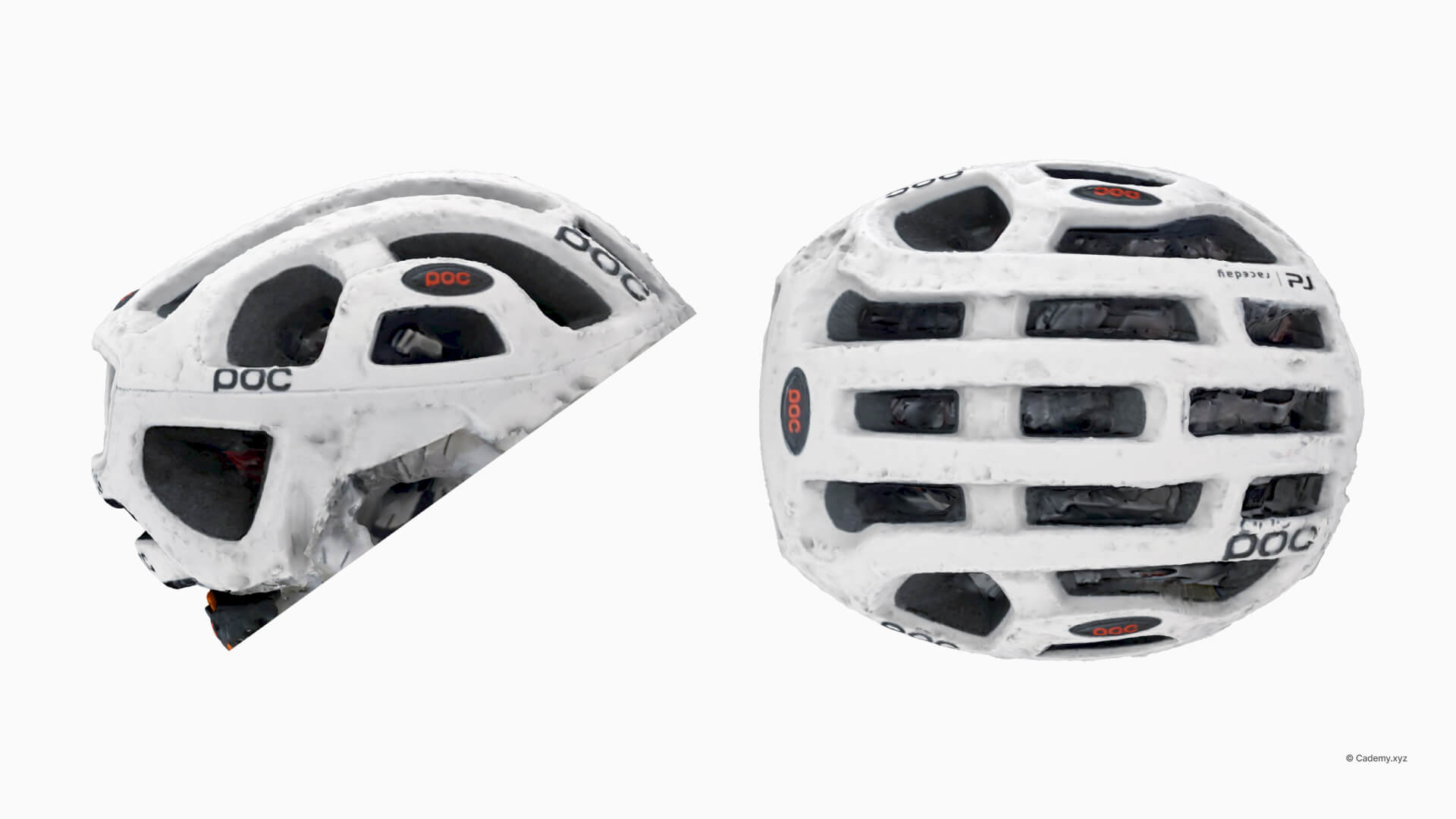
Generating Primary Surfaces
4. Surface from 4 Edges – For an efficient base structure
5. Match Surface – Refined tangency & curvature
6. Trimming – To refine helmet contours
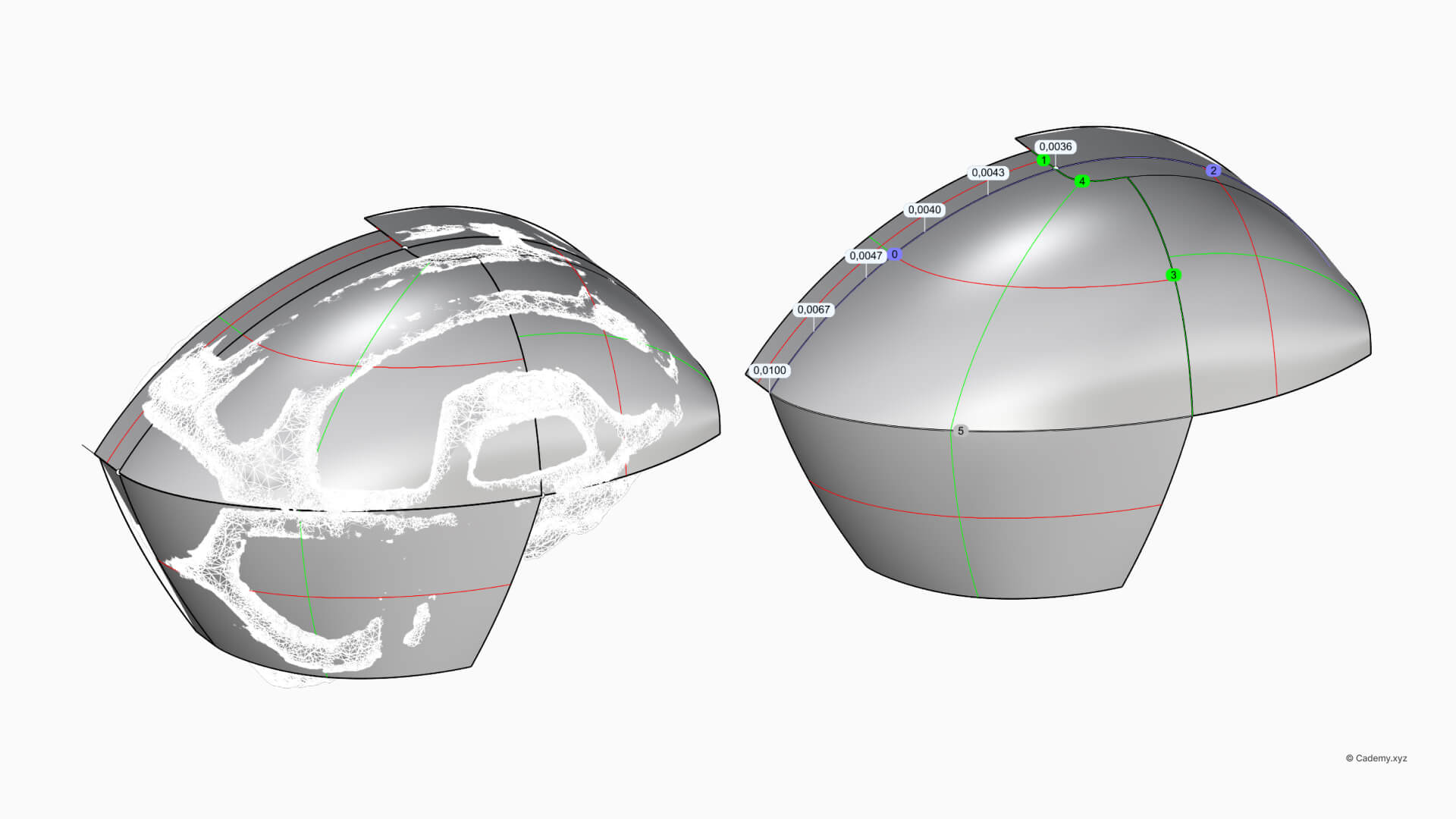
Converting to a Solid Model
7. Connected the front face
8. Blended edges for seamless continuity
9. Scaled & thickened the model for 3D printing compatibility
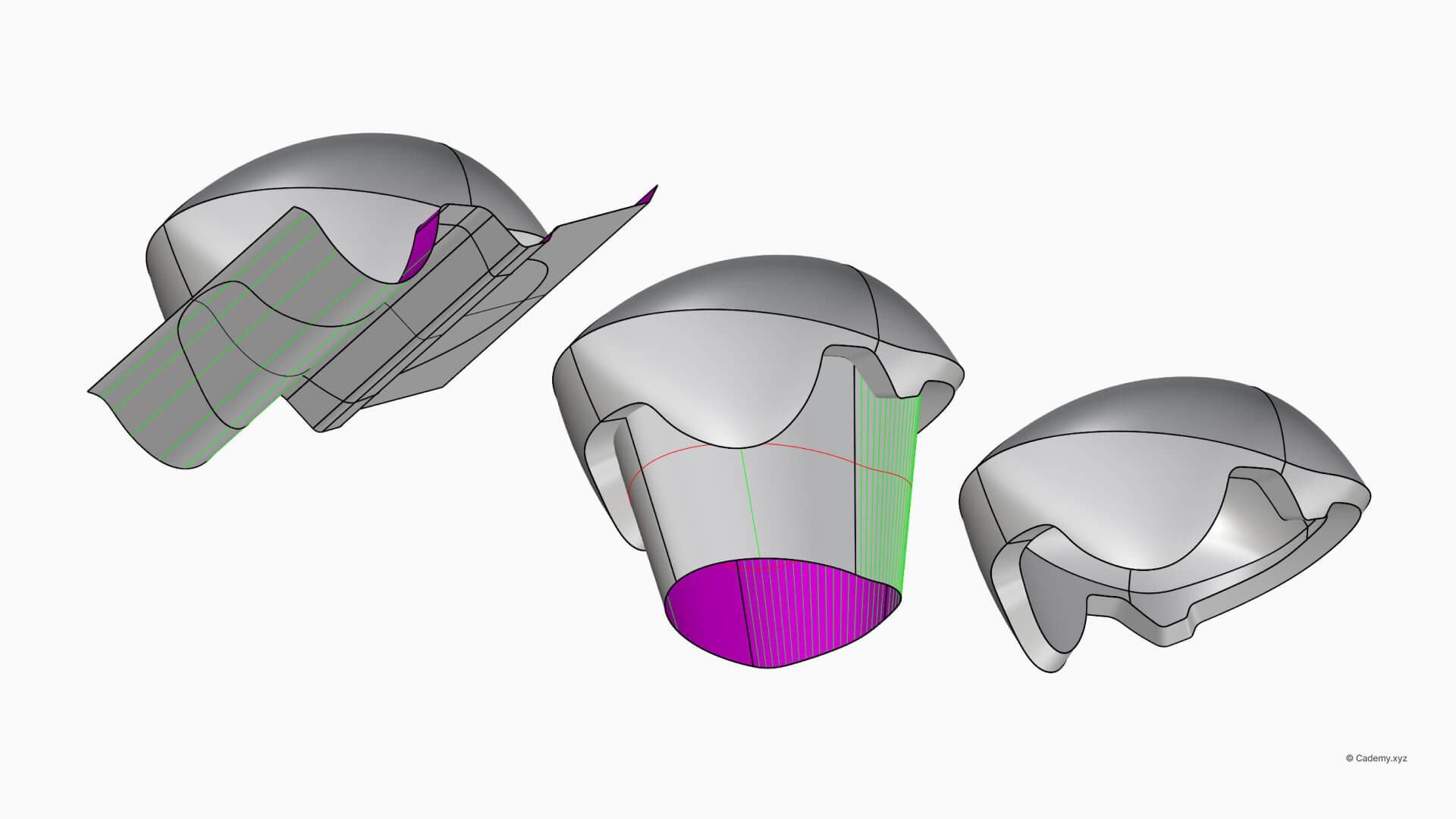
Step 2: Perforations & Bottom Features
Designing Vent Holes
10. Used CurveBoolean to define complex vent profiles
11. Applied Fillet & Offset for smooth edges
12. Projected & Trimmed vents onto the helmet surface
Refining the Bottom Section
13. Duplicated & scaled the bottom edge
14. Extended surfaces for structural integrity
15. Lofted inner layers to reinforce the design
A Global Edge Continuity check ensured a watertight solid ready for fabrication.
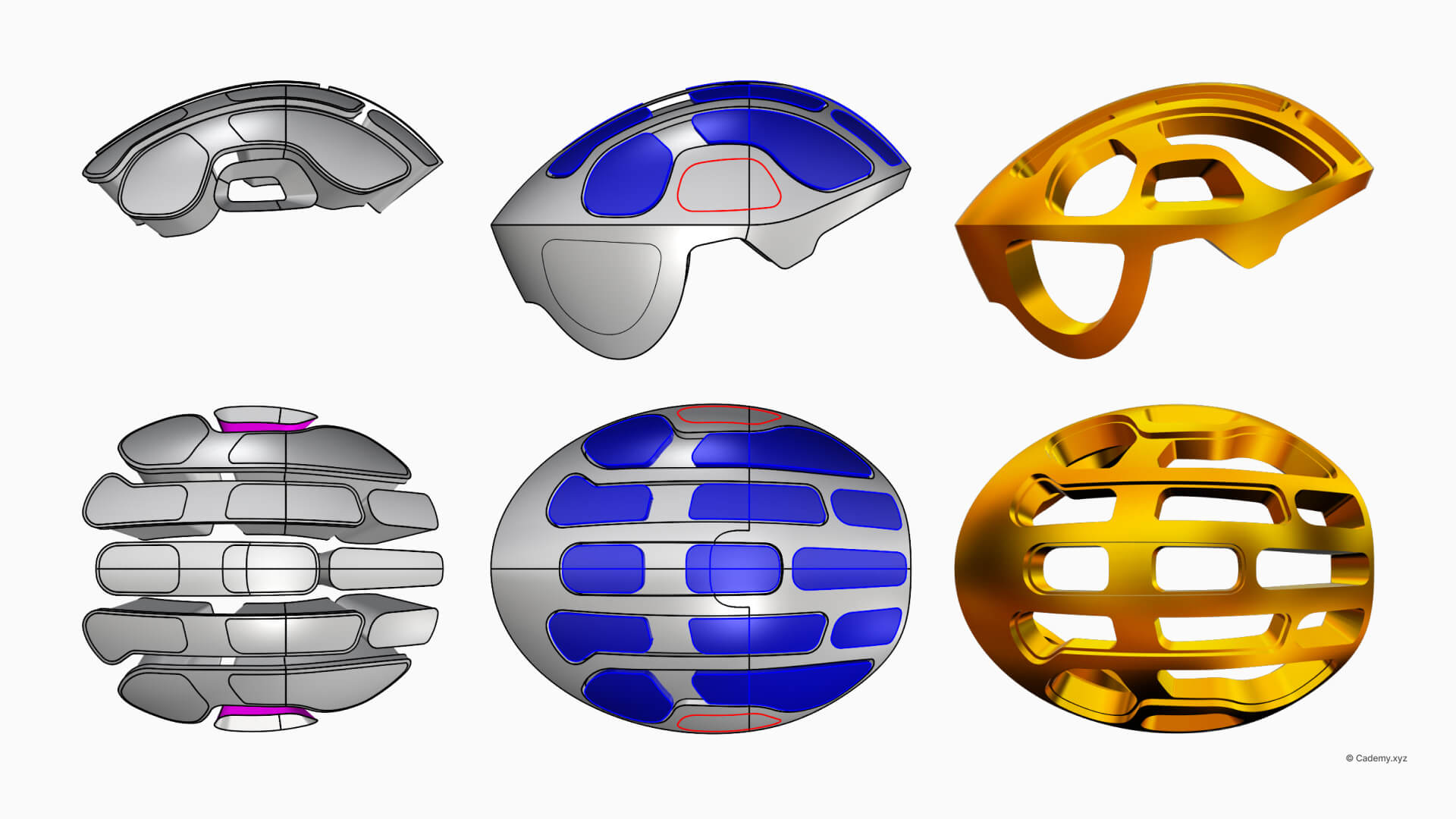
Step 3: Creating Gyroid Lattices in Grasshopper
Preparing the Mesh for Lattice Generation
16. Converted the NURBS model into a mesh
17. Defined a Voxel Grid (20x20x20mm) for lattice distribution
18. Generated a Gyroid Lattice using Crystallon Plugin
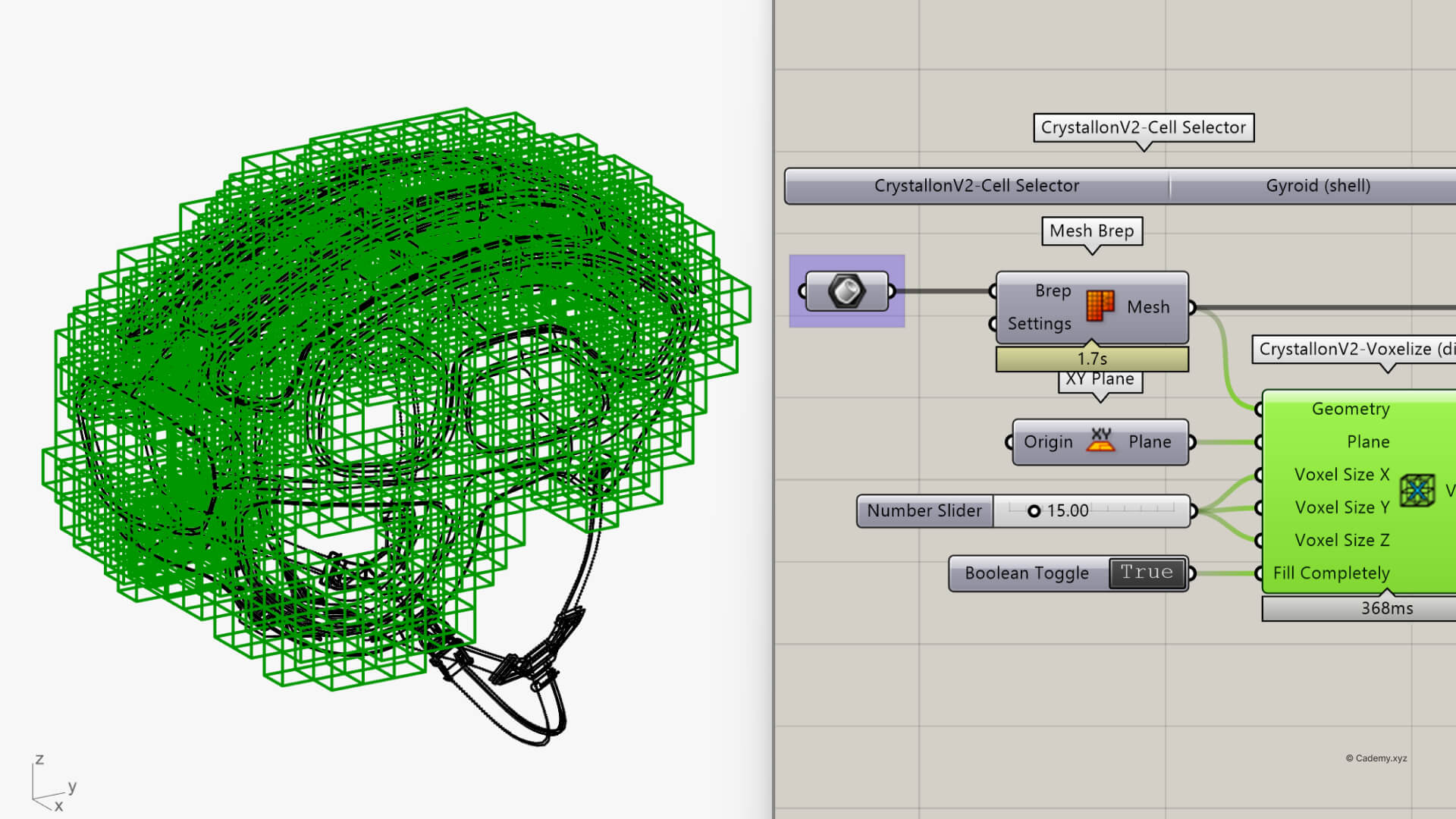
Refining the Structure
18. Trimmed excess lattices for a clean fit
19. Thickened the lattice using Mesh Thicken
20. Applied Catmull-Clark Subdivision for a smooth finish
The final STL export prepared the model for 3D printing.
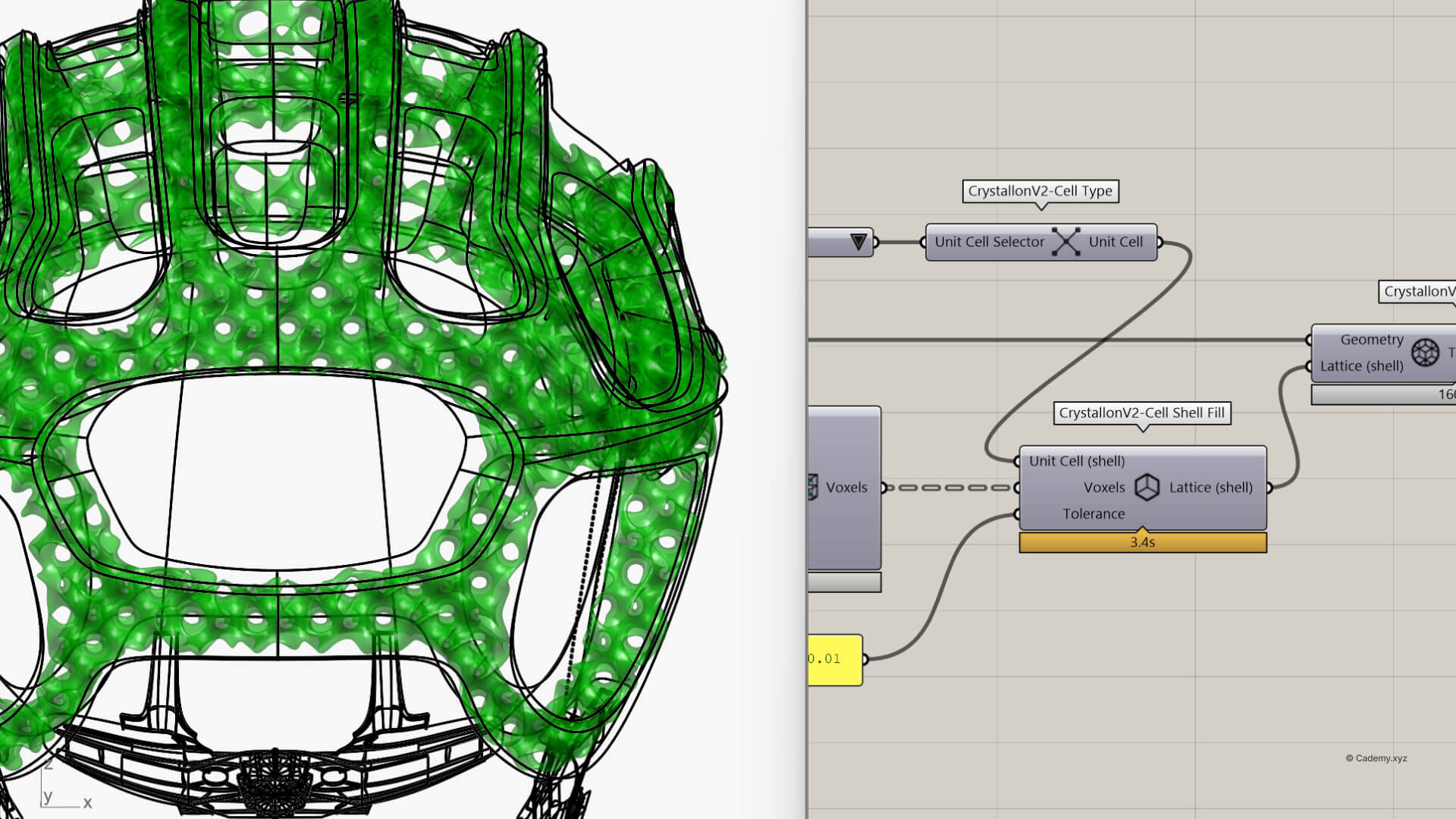
Step 4: Rendering & Animation in Keyshot
Setting Up the Scene
21. Imported the Rhino model into Keyshot
22. Applied realistic materials (e.g., glossy shell, matte gyroid)
23. Adjusted HDRI lighting for depth & realism
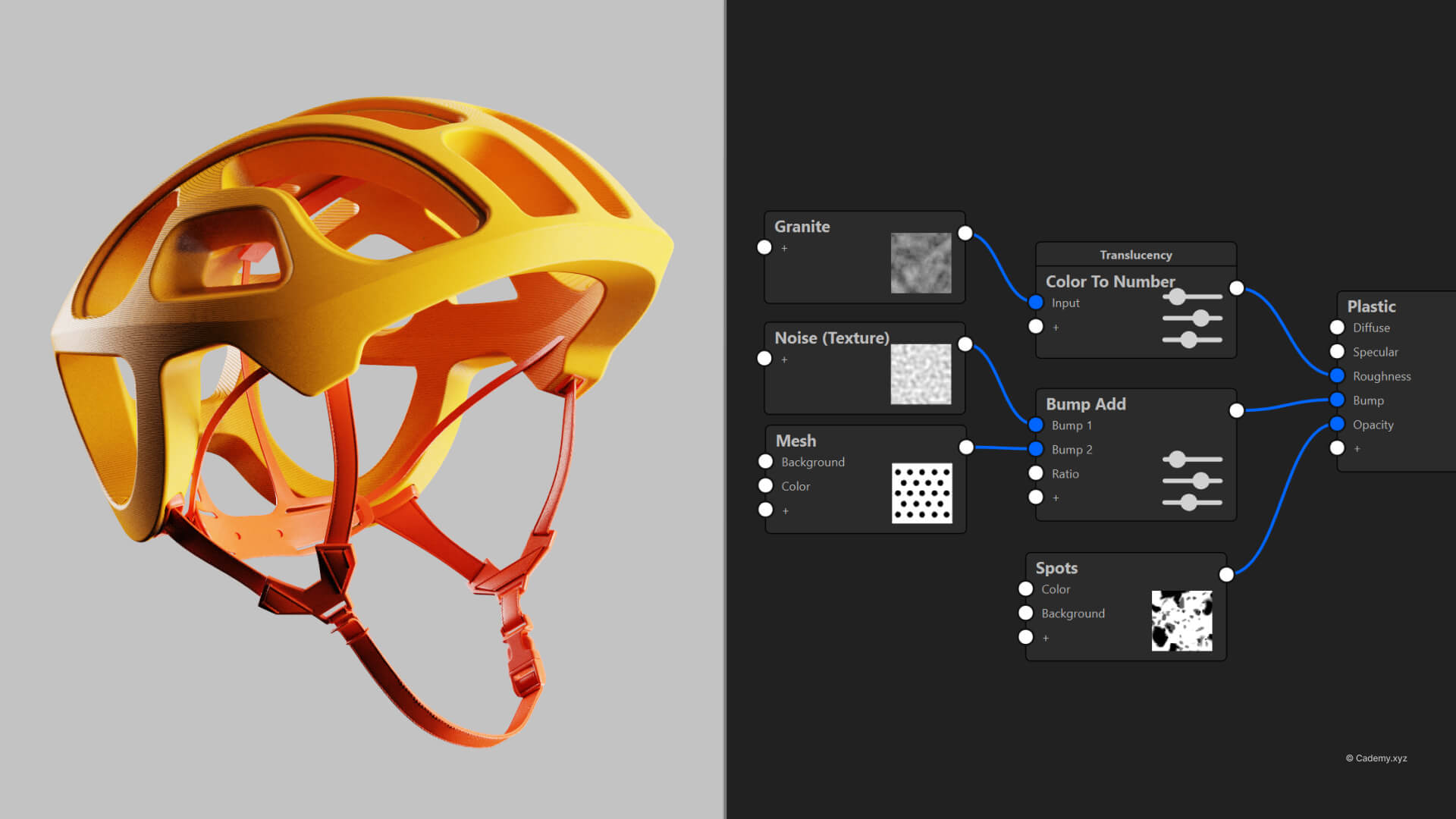
Animating the Reveal
24. Part Fade Animation – Unveiled the internal lattice structure
25. Rotation Animations – Showcased different design angles
26. Cutaway Material – Created dynamic cross-section views
The result? A polished, presentation-ready render highlighting both form and function.
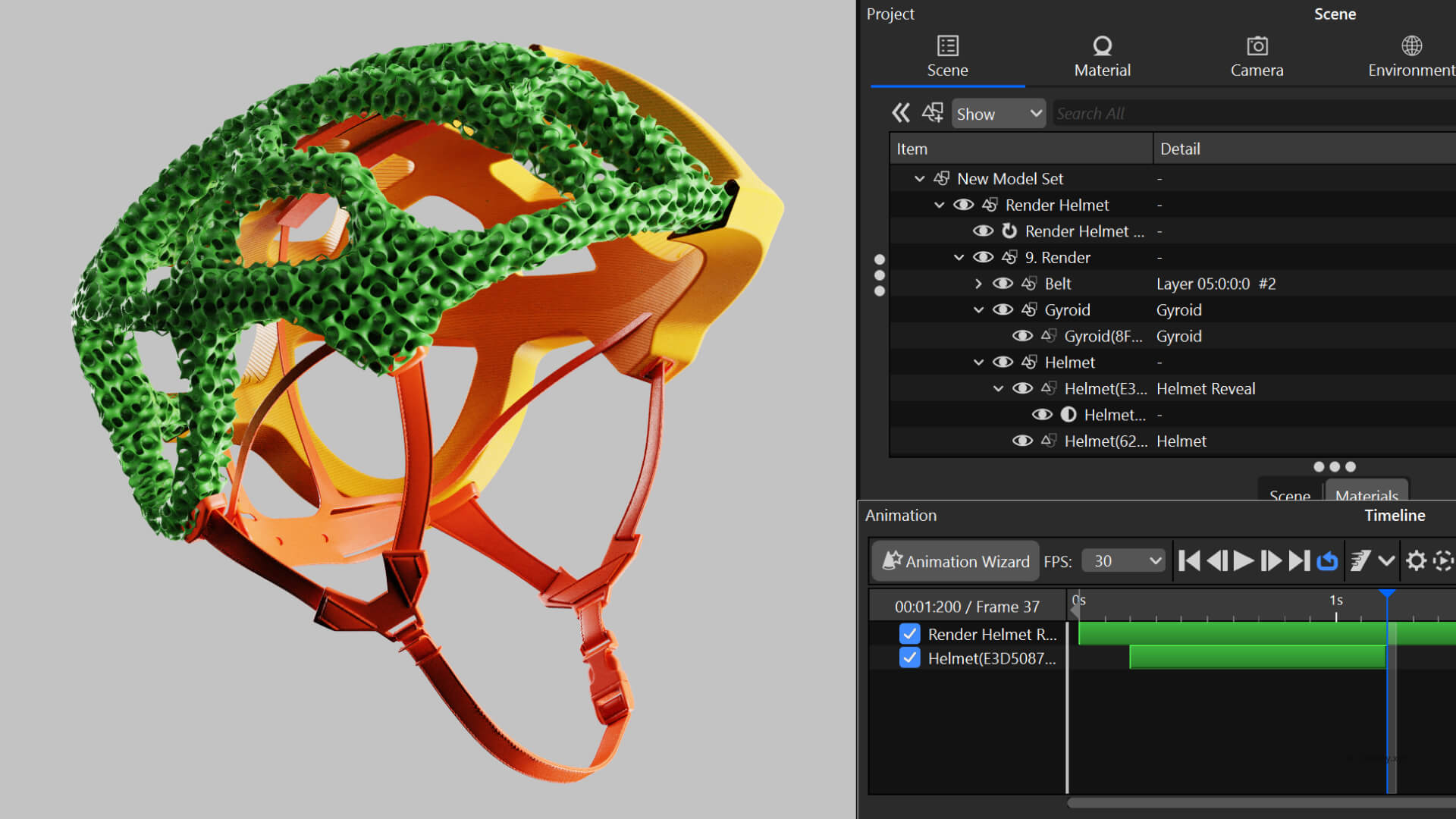
Conclusion
This workflow streamlines the design of complex, functional geometries while maintaining structural integrity. Whether you’re working on helmets, automotive components, or product designs, mastering these tools will elevate your 3D modeling skills.
Thanks for reading ❤️
Don’t miss out, enroll today.
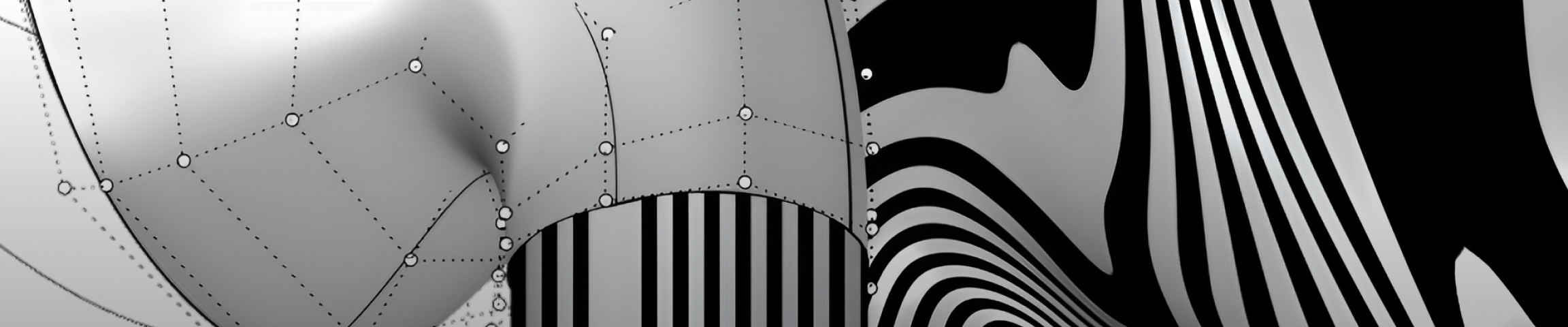