Good vs. Bad Command Order in Rhino 3D
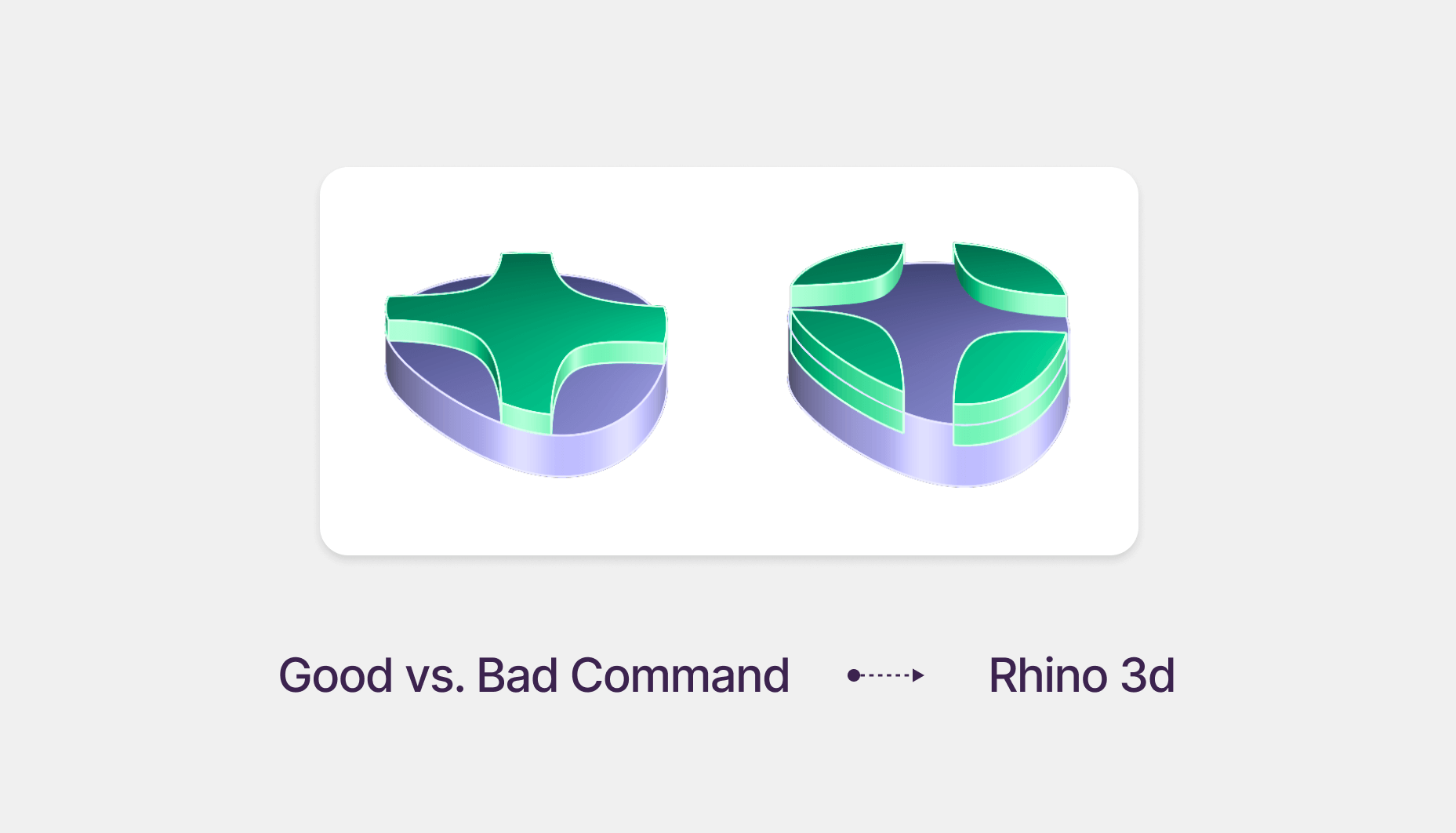
Rhino 3D is a surface modeling tool, yet many users approach it as if it were a solid modeling software. This misunderstanding often leads to unnecessary geometry, failed operations, and frustrating errors. One of the biggest lessons in Rhino modeling is that the order of operations matters!
In this article, we’ll look at how a simple modeling task creating a gamepad arrow key can either cause unnecessary complications or result in a clean, efficient model.
Why Order Matters in Rhino Modeling
Many Rhino users approach it like a solid modeling software, leading to:
- Boolean operations failing
- Fillets not working as expected
- Extra edges complicating the model
The key to clean and efficient modeling is not just using the right commands—but using them in the right order. Let’s break it down with an example:
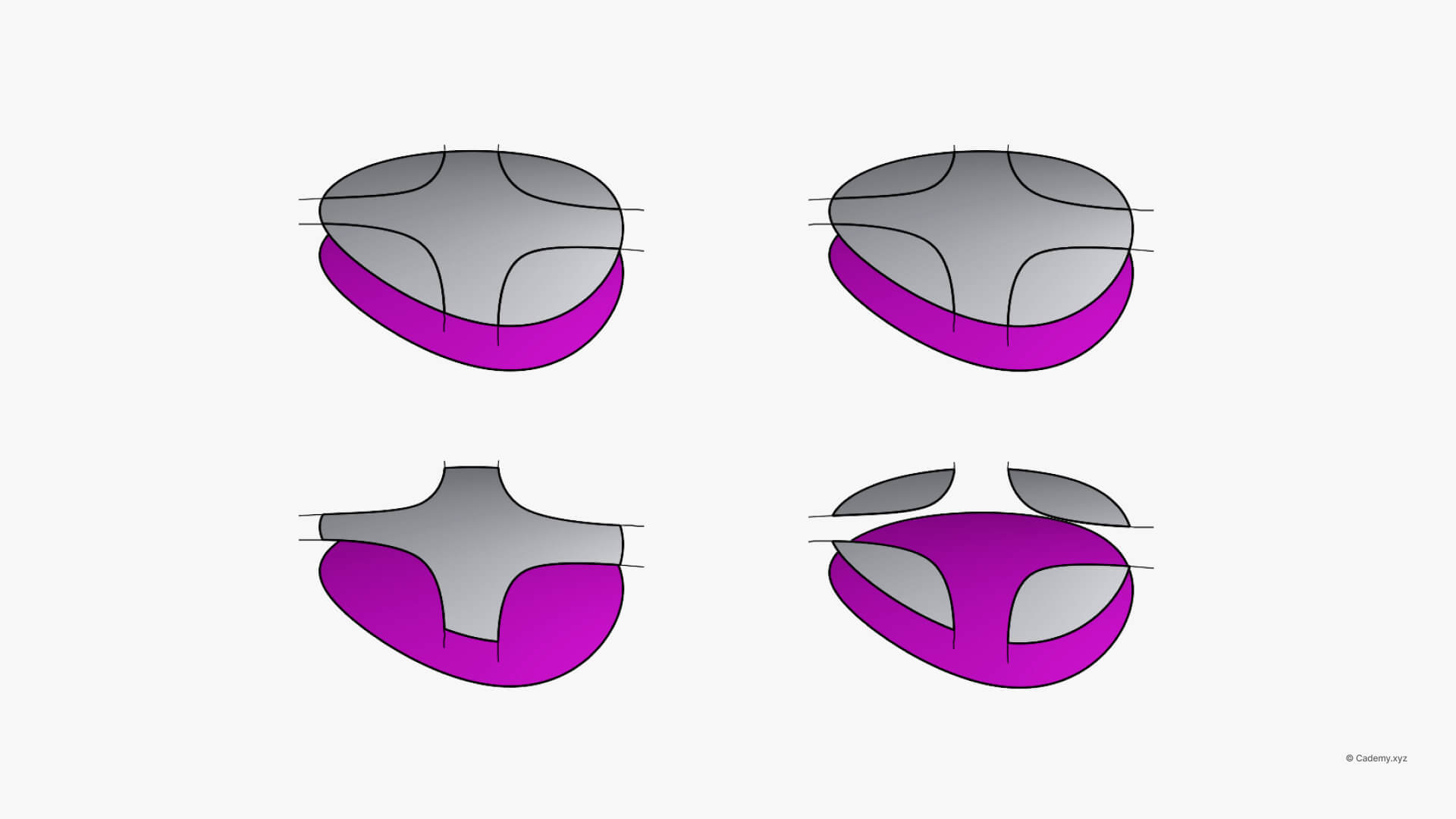
Bad Order: Boolean Union After Extrusion
A common mistake:
- Extruding the top arrow key shape separately
- Extruding the circular base separately
- Joining them with Boolean Union
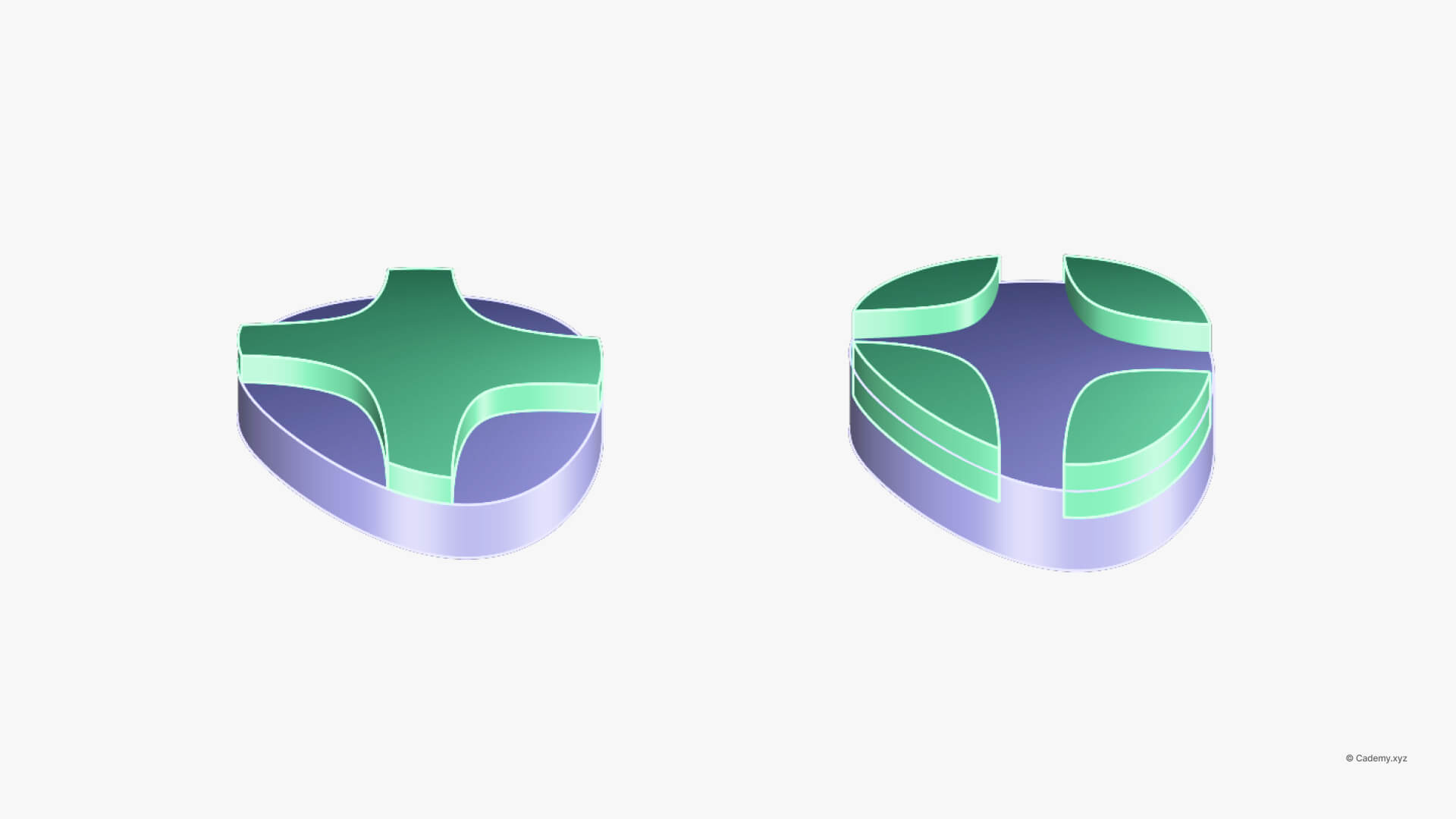
Why is this bad?
- Creates an extra edge in the middle
- Fillet operations may fail due to complex geometry
- Coplanar faces don’t merge cleanly
- Causes shading and rendering issues
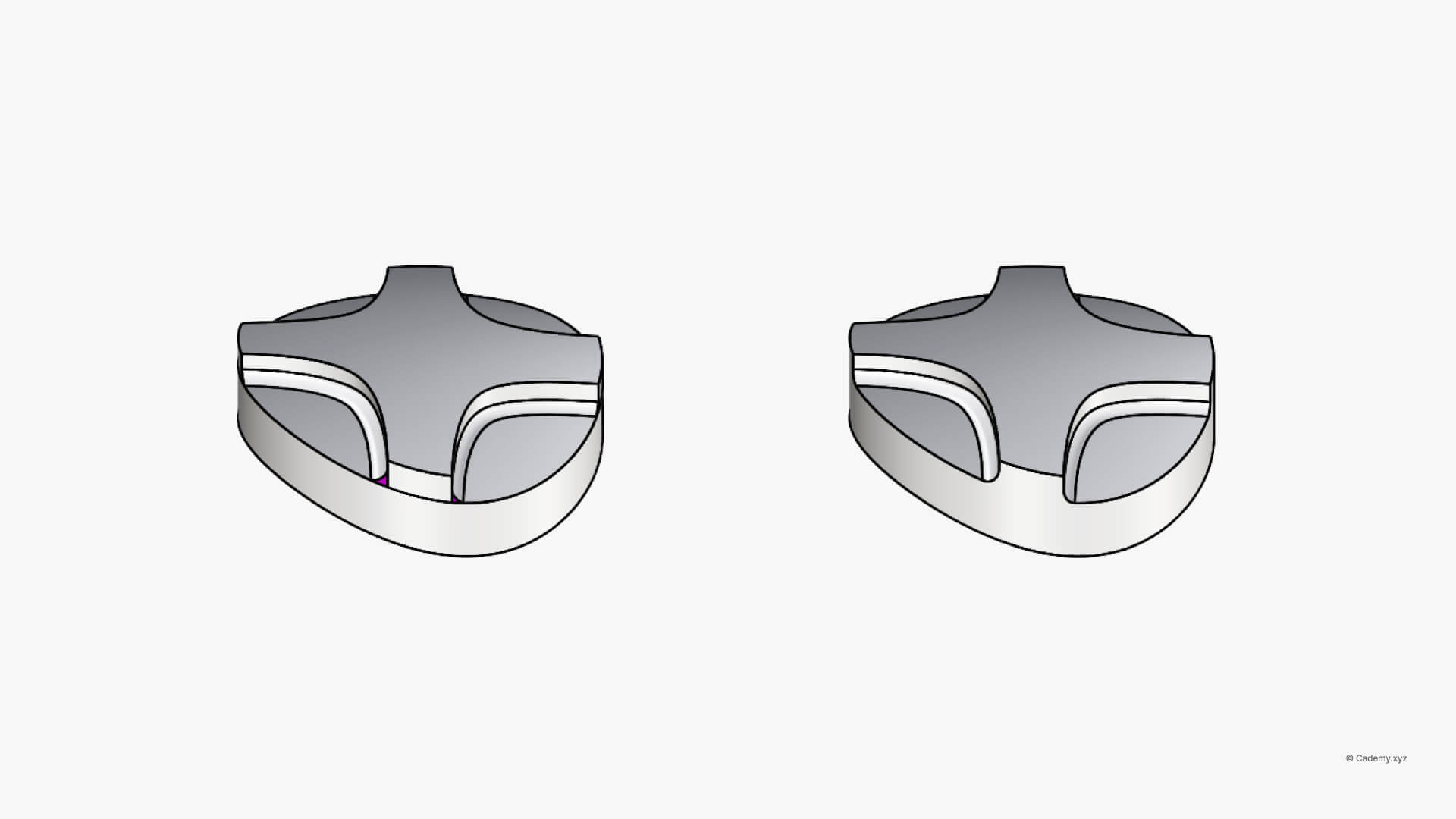
Good Order: Boolean Difference for a Cleaner Model
A better approach:
- Extrude the base part to the final height
- Use the arrow shape as a Boolean Difference to carve out the design
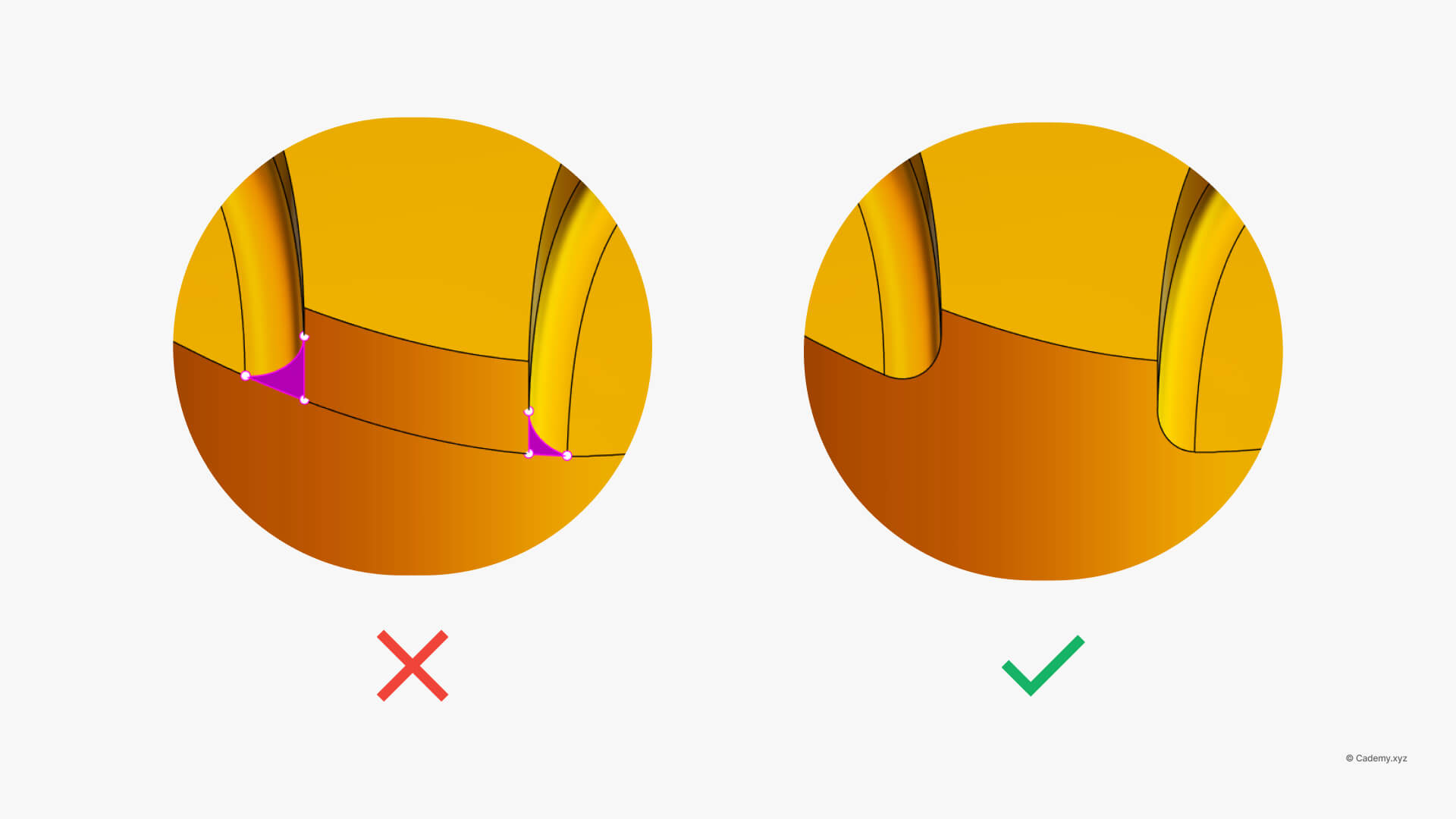
Key Takeaways
- Plan Boolean operations carefully.
- Avoid creating unnecessary surfaces and edges.
- Subtracting is often cleaner than adding.
Mastering these fundamental concepts will streamline your Rhino workflow, reduce errors, and help you create high-quality, production-ready models.
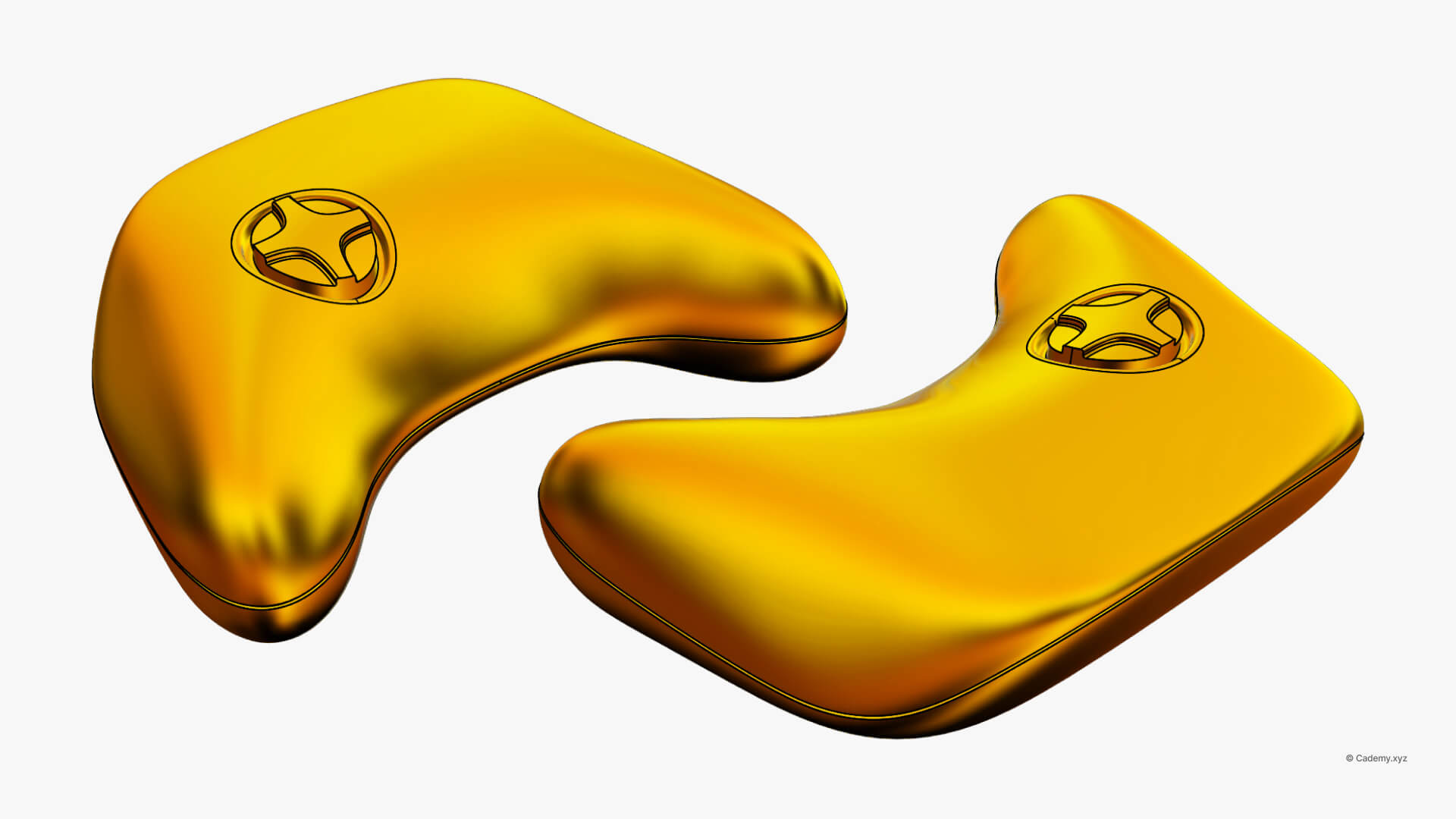
Conclusion
Efficient surface modeling in Rhino isn’t just about knowing commands—it’s about using them in the right sequence. By avoiding extra edges and optimizing your Boolean workflow, you can achieve:
- Better fillets
- Cleaner topology
- More efficient industrial design
Thanks for reading ❤️
Don’t miss out, enroll today.
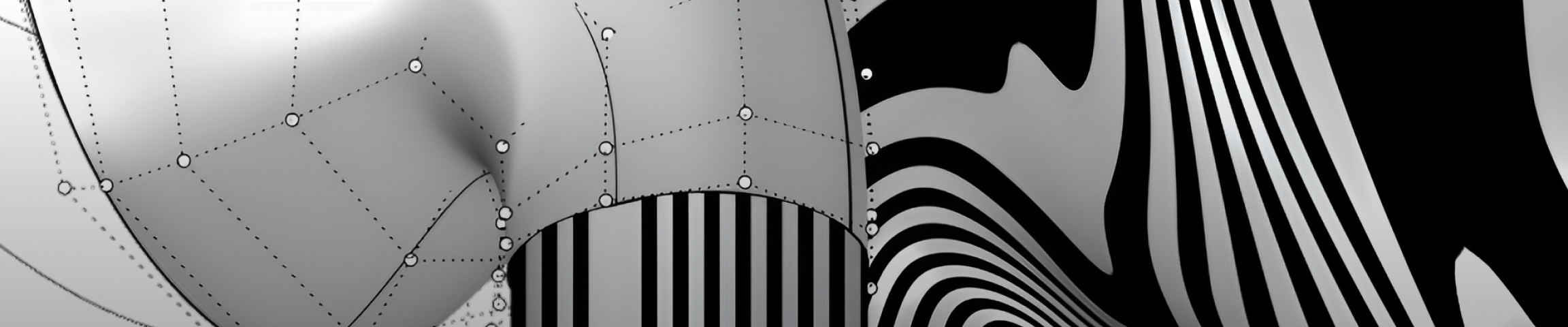